برگردان: مهندس عاطفه کلایی
در واحدهای تولید برای چنین موادی دما باید همواره کم¬تر از میزانی باشد که عامل اسفنجش و یا اتصال عرضی فعال می¬¬شود. هرمن اشنایدر از شرکت کوپریون ورنر توضیح می¬دهد که چگونه می¬توان تمام فرایند تولید ورق¬ها را طی یک مرحله پیوسته با صرفه اقتصادی انجام داد. این فرایند تک¬مرحله¬ای به گونه¬ای طراحی شده است که از فشار وارده آمده به ماده اولیه می¬کاهد و محصول نهایی ورق تولیده شده از کیفیت بالایی نیز برخودار است.
امروزه ورق¬های پلاستیکی ساخته شده از پلی¬پروپیلن PP یا پلی¬اتیلن PE در بسیاری از شاخه¬های صنعت نظیر خودروسازی، ساخت تجهیزات ورزشی تفریحی و هم¬چنین لوازم خانگی برقی به کار گرفته می¬شوند. ویژگی منحصر به فرد این ورق¬ها، یعنی خاصیت اسفنجی آنها و داشتن اتصال عرضی طی یک فرایند اکستروژن مستقیم حاصل می¬شود. در اغلب موارد ورق¬ها پیش از اسفنجی شدن دارای عرض 80 تا 150 سانتی¬متر و ضخامتی بین 2/0 تا 2 میلیمتر می¬باشند که پس از انجام فرایند و افزودن عامل اسفنجی به ماده اولیه می¬تواند تا سه برابر نیز (ضخامتی بین 6/0 تا 20 میلیمتر) افزایش یابد. استفاده در داشبوردها و به کارگیری در ورق¬های عایق صدا بین صفحات فلزی از جمله عمده¬ترین کاربردهای این ورق¬ها به شمار می¬روند.
نیاز به کیفیت بالا
طراحی فرایند تولید این ورق¬ها علاوه بر اطلاعات علمی و فرمول ماده اولیه مورد استفاده به دانش مهندسی بالایی نیز احتیاج دارد. در همین راستا اطمینان از شرایط زیر ضروری است:
• پراکندگی یکسان و همگن تمامی مواد، خصوصا عامل اسفنجش و ایجاد¬کننده اتصال عرضی در ماده اولیه
• دما باید همواره کم¬تر از دمای جوش عامل اسفنجش و اتصال عرضی باشد و در هیچ بخشی از ماده اولیه تحت فرایند نباید دما از حد مجاز تعیین شده تجاوز کند.
• ضخامت ورق¬ها در جهت اکستروژن و هم¬چنین عمود بر آن باید ثابت بوده و یا به میزان بسیار جزئی متغیر باشد. چه حتی اختلاف¬های بسیار کوچک در ضخامت ورق می-تواند باعث تغییر ضخامت ورق¬های اسفنجی به میزان زیادی گردد.
• در کنار تمام محدودیت¬های عملیاتی که فرایند را مشکل می¬سازند، امکان طراحی فرایندی که علاوه بر مزیت¬های فوق صرفه اقتصادی نیز داشته باشد، ممکن است.
به منظور دستیابی به شیوه¬ای اقتصادی باید فرایندی طراحی نمود که تمامی آن از وارد شدن مواد اولیه تا فرآوری نهایی در طول یک مرحله انجام شود. در حقیقت باید دو مرحله ترکیب مواد و اکستروژن باهم تلفیق شوند. جدا کردن این دو فرایند باعث بالا رفتن هزینه-های تولید می¬شود و مشکلاتی از نظر فضای مورد نیاز برای نگهداری مواد گوناگون را به وجود می¬آورد. علاوه بر آن در این شرایط مواد دو بار تحت شوک حرارتی قرار می¬گیرند و احتمال تخریب وجود دارد و به دلیل نیاز به سرمایش و گرمایش مجدد مواد، هزینه انرژی نیز بالا می¬رود.
شکل 1 : تجهیزات مربوط بهtwin screw MEGA compounder ZSK برای اکستروژن ورق-های اسفنجی
مخلوط کن دو ماردان
برای دست¬یابی به فرایندی تک¬مرحله¬ای عملیات اختلاط باید در یک مخلوط کن دو ماردان انجام شود. چه این دستگاه تنها ماشینی است که می¬تواند اختلاط لازم و پراکندگی مناسب بین مواد را در زمان ماند کوتاه مواد در مخزن مخلوط کن، به وجود آورد. با استفاده از یک پمپ دنده¬ای در پائین¬دست فشار پشت دای در نوک ماردان کاهش یافته و فشار مناسب برای اکستروژن فراهم می¬شود. دو فرایند اختلاط و تولید فشار تا حد زیادی از هم مستقل هستند و به همین دلیل می¬توانند به طور جداگانه بهینه شوند. بر اساس این ویژگی¬ها Coperion Werner&Pfleiderer آزمایش¬های اولیه¬ای در مورد اکستروژن ورق¬های اسفنجی و دارای اتصال عرضی انجام دادند که منجر به دست-یابی به فرایند تک¬مرحله¬ای مناسبی برای تولید این ورق¬ها گردید (شکل 1).
سامانه خوراک دهی وزنی
این سامانه می¬تواند برای وارد کردن 10 جز از مواد اولیه به عنوان خوراک طراحی شود و قادر به فرآوری مجدد مواد نیز می¬باشد.
از آنجائی¬که سختی یکی از ویژگی¬های عمده ورق¬های اسفنجی به شمار می¬رود تمام مواد در سامانه خوراک¬دهی با توجه به افت وزنی خوراک وارد دستگاه می¬شوند. این سامانه خوراک¬دهی دقتی معادل با 1± در سه دقیقه دارد و می¬تواند کاهش وزن حتی در کوچک¬ترین مقادیر را نیز تشخیص دهد. برای اطمینان از پیوسته بودن فرایند خوراک دهی، برای خوراک¬دهندهPP یا PE به عنوان جز اصلی و دیگر مواد به عنوان جز فرعی در سامانه تعریف می¬شوند.
برای مخلوط کردن مواد از یک مخلوط¬کن دوماردان ZSK 70 SC استفاده می¬شود که قطر هر ماردان آن 70 میلیمتر و طول بخش فرآوری D36 است. این دستگاه با یک خوراک¬دهنده جانبی، دو هواکش اتمسفریک و یک سامانه میعان دهنده تحت خلا مجهز شده است.
تمامی مواد به جز عامل پف¬دهنده و عامل ایجاد اتصال¬های عرضی از قیف ورودی خوراک دستگاه وارد آن می¬شوند. اولین بخش اکسترودر برای موادی که فرآوری آنها انرژی زیادی نیاز دارد طرحی شده است. در این بخش برخی مواد ذوب می¬شوند و هم زمان به حداکثر دمای ذوب خود یعنی 160 درجه سانتی¬گراد می¬رسند. کنترل سرمایش و گرمایش مخزن مواد به ما اطمینان می¬دهد که دما در طول فرآوری از میزان مجاز تعیین شده فراتر نخواهد رفت.
ذوب شدن، اختلاط و همگن¬سازی
پس از ذوب کردن مواد و یک مرحله همگن¬سازی اولیه، پودر پف¬دهنده مواد (معمولا از آزو دی¬کربنامید اصلاح شده استفاده می¬شود) از خوراک¬دهنده جانبی وارد می¬شود. به منظور فراهم کردن ایمنی مناسب خوراک¬دهنده جانبی به صورت یک سامانه احتراق بسته و عایق طراحی شده است. عامل پف¬دهنده به همراه هوا وارد مواد دیگر شده و در بین آنها پراکنده می¬شود. هوا به تدریج از طریق خوراک¬دهنده جانبی و سامانه میعان دهنده از مخلوط جدا می¬شود.
یک خوراک¬دهنده برای مایعات نیز در بخش میعان¬دهنده تعبیه شده است تا از طریق آن بتوان پراکسید را به عنوان عامل ایجاد¬کننده اتصال عرضی به مخلوط اضافه کرد. پراکسید در دمای بسیار کم بلور می¬شود به همین دلیل برای جلوگیری از این امر پراکسید در شرایط بدون فشار به مخلوط اضافه می¬شود و بعد از آن مجددا فشار لازم برای ذوب مواد در اکسترودر فراهم می¬شود.
پیش از تخلیه مخلوط از دستگاه، مواد از سامانه میعان¬دهنده تحت خلا که فشار خلا در آن کمتر از mbar 50 است عبور می¬کند. این فشار توسط یک پمپ مکنده تامین می¬شود. عبور مواد از این مرحله باعث می¬شود هیچ مواد فراری در مخلوط باقی نماند که بتواند به بافت اسفنجی آسیب برساند. به دلیل زیاد بودن تعداد موادی که با هم مخلوط می¬شوند، خطر تجزیه مواد خصوصا در بخش مارپیچی مخلوط¬کن همواره وجود دارد. بنابراین میزان این خطر باید توسط سامانه¬های کنترل فرایند اکسترودر مشخص شود. به همین دلیل تیغه-های مارپیچ مخلوط¬کن از ماده عایق ضد سایش WP15 پوشیده شده است. تیغه¬های مارپیچ به اندازه کافی صاف و صیقلی هستند تا از چسبیدن مواد به آنها اجتناب شود. سرعت تولید در این دستگاه با توجه به نوع ورق از 250 تا 300 کیلوگرم در ساعت متغیر است.
پمپ دنده¬ای، دای ورق و استفاده از کلندر
در انتهای ZSK مخلوط همگن¬شده از مواد ذوب شده فشاری در حدود bar20 بار دارد. در این مرحله پمپ دنده¬ای این فشار اولیه را به bar 100 می¬رساند. با استفاده از یک تعویض¬گر توری خودکار در انتهای خط ذراتی که در مخلوط به خوبی پراکنده نشده¬اند مشخص می-شوند. تنظیمات موتور دنده¬ای و تعویض¬گر توری به گونه¬ای است که فشار پشت دای به حداقل می¬رسد و به این ترتیب دمای ذوب مواد تغییر چندانی نمی¬کند. پس از این مرحله مخلوط که فشار کم¬تری پیدا کرده است وارد دای و کلندر می¬شود.
در این مرحله فشار در حدود 60 بار است و عبور مخلوط از میان غلتک ها ورق¬هایی صاف با ضخامت یکسان در تمام جهات به وجود آورده است. بعد از این مرحله تمامی ورق¬ها با ماده پوششی پوشیده می¬شوند¬. قابلیت تنظیم فاصله دو غلتکی که بر روی هم قرار گرفته-اند باعث می¬شود تا بتوان ضخامت ورق¬ها را نیز تنظیم نمود. غلتک¬ها به کنترل¬کننده کشش ورق مجهز شده¬اند تا نسبت به ضخامت ثابت ورق در تمام نقاط اطمینان حاصل شود. در حقیقت هدف اصلی از تعبیه پرتوسنج برای اندازه¬گیری ضخامت ورق، کنترل کیفیت آن است. برای ورق¬هایی با ضخامت mm 1 ( یک میلیمتر) تغییر01/0 ± در ضخامت بلامانع است.
حداقل سازی اختلاف ضخامت
سامانه کنترل EpcNT در اکسترودر ZSK بر اساس واپایشگر زیمنس S7 ساخته شده است. این نمونه از آخرین مدل¬های واپایشگر است که در کنترل ضخامت ورق¬ها نقش بسیار مهمی دارد. این سامانه کنترل کلی سامانه را انجام می¬دهد. در واقع تمامی واپایشگرها برای خوراک¬دهنده، پمپ دنده¬ای و غلتک¬ها در EpcNT تلفیق شده¬اند. این واپایشگرقابل نصب روی Windows است و امکان کنترل آسان و صحیح تمام سامانه را فراهم می¬کند.
به منظور فراهم کردن شرایط عملیاتی که در آن تغییرات ضخامت در ورق¬ها بسیار ناچیز باشد، فشار پائین دستی پمپ دنده¬ای (فشار حداقل) به عنوان پارامتر کنترل مرجع در نظر گرفته می¬شود با استفاده از اعمال تغییرات در سرعت و گشتاور اکسترودر، فشار خوراک، سرعت پمپ دنده¬ای و سرعت غلتک¬ها یا ورق¬هایی که از آن خارج می¬شوند فشار پائینی پمپ دنده¬ای به عنوان پارامتر کنترل مرجع در سامانه کنترل ثابت نگه داشته می¬شود. الگوریتم کنترل این سامانه با استفاده از تجربیات Coperion Werner & Pfliederer بدست آمده و در سامانه کنترل ذخیره شده است.
در حال حاضر در بسیاری از واحدهای تولید ورق¬های اسفنجی با اتصالات عرضی با استفاده از دستگاه¬هایی که ویژگی¬های فوق را داشته باشند به روشی مناسب و با صرفه اقتصادی تولید می¬شوند.
واژه نامه
دارای قابلیت تشکیل اتصال عرضی: Cross linkable
اسفنج¬شدنی : Foamable
اکستروژن : Extrusion
آمیزه¬ساز دوماردانه¬ی مگا : twin screw MEGA compounder
پمپ¬دنده¬ای : Gear pump
سامانه خوراک¬دهی وزنی : gravimetric master/ slave feed system
هواکش اتمسفریک : Atmospheric venting
سامانه گاززدای تحت خلا : Devolatilization under vacuum
واپایشگر کشش ورق : sheet traction controller
درباره وب
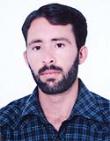
http://www.telegram.me/sajjadshafiee_ir . . . رشته مهندسی پلیمر نسبت به رشتههای مهندسی دیگر تقریبا جوان است و شکوفایی آن از زمان جنگ جهانی دوم آغاز شده است. اما به دلیل کاربرد روزافزون پلیمر در صنایع مختلف، این رشته به سرعت رشد کرده و امروزه جزو یکی از رشتههای مهم کشورهای صنعتی پیشرفته میباشد. هدف رشته مهندسی صنایع پلیمر تولید کلیه محصولات پلیمری از قبیل لاستیک، پلاستیک، الاستومر، چسبها، رزین و سایر مواد مورد نیاز صنعت است. برای مثال طراحی و تولید تایر ماشین در صنایع لاستیک، لولههای پلیاتیلن در صنایع پلاستیک و انواع فایبرگلاسها در کامپوزیت به یاری متخصصان مهندسی صنایع پلیمر انجام میگیرد یا حتی در این رشته شکلدهی رزینها نیز مطرح است که برای مثال میتوان به ساخت ملامین اشاره کرد.حتی کیسههای پلاستیکی و روکش ظروف نچسب ( تفلون ) از مواد پلیمری میباشند. در واقع در رشته مهندسی صنایع پلیمر هر آنچه که به این مواد بر میگردد، مورد مطالعه و بررسی قرار میگیرد. البته پلیمرها فقط کاربرد صنعتی ندارند بلکه کاربرد پزشکی نیز دارند. مثلا اگر کشکک زانوی یک نفر آسیب ببیند و ترمیم آن امکانپذیر نباشد، شبیه به همان کشکک زانو را با مواد پلیمری درست میکنند و بر روی زانو قرار میدهند و یا دندان مصنوعی و لنزهای چشمی همه از مواد پلیمری ساخته میشوند که به این مواد پلیمری «پلیمرهای زیستی» میگویند. فرصتهای شغلی: در صنعت پوشاک پلیمرها در تولید پاپوشها، تنپوشها و کفپوشها بسیار موثر هستند. در صنایع حمل و نقل زمینی (خودروسازی، قطار و ... )، هوایی ( هواپیما و بالگرد) و دریایی (کشتیها و ...) پلیمرها حضوری چشمگیر دارند، و بالاخره در صنایع نظامی، پزشکی، کشاورزی و بستهبندی کاربرد مواد پلیمری بسیار گسترده است.بدر صنعت پوشاک نیز پلیمرها در تولید پاپوشها، تنپوشها و کفپوشها بسیار موثر هستند. در صنایع حمل و نقل زمینی (خودروسازی، قطار و ... )، هوایی ( هواپیما و بالگرد) و دریایی (کشتیها و ...) پلیمرها حضوری چشمگیر دارند، و بالاخره در صنایع نظامی، پزشکی، کشاورزی و بستهبندی کاربرد مواد پلیمری بسیار گسترده است. باتوجه به کاربرد وسیع پلیمرها در صنایع، فارغالتحصیلان این رشته تواناییهای کافی در زمینههای ایجاد و برنامهریزی واحدهای تولیدی تبدیل پلیمر خام به مواد مصرفی و اشتغا
جستوجو
ویژه مدیریت وب
نویسندگان
لینک دوستان
برچسبها وب
مدیریت (23)
عکس (4)
مدیریت در اسلام (4)
اندروید (3)
فناوری نانو (2)
و (2)
یراق کابینت (1)
کائــوچو (1)
کائوچو طبیعی (1)
کاندیدای (1)
کوبه (1)
نوستالژی (1)
قفل حیاطی (1)
قفل لوکس (1)
قفل یونیک (1)
قفل کتابی (1)
قفل کمدی (1)
گالری یراق کوبه (1)
لاهیجان (1)
مجلس (1)
مدیر موفق (1)
مرد و زن (1)
مرودشت (1)
مزایای بیوپلیمر (1)
ملامین چیست (1)
مدیریت دانش (1)
انقلاب صنعتی (1)
ایام (1)
ایران (1)
اکسترودر (1)
پاسارگاد (1)
پلی اتیلن ، (1)
پلی پروپیلن (1)
پلی ونیل کلراید (1)
ارسنجان (1)
اسلامی (1)
اسلحه پلیمری (1)
امیرکبیر (1)
پی وی سی - PVC (1)
تاسوعا (1)
تسلیت (1)
تولدم مبارک (1)
جزوه الاستومر (1)
حسینی (1)
داستان (1)
داستانهای زیبا (1)
در (1)
دستگیره درب (1)
دهمین (1)
دوره (1)
سوپر جاذب (1)
شعر (1)
شهرستان های (1)
شورای (1)
عاشورا (1)
حامیان بلک اسکین
تاریخ : پنج شنبه 90/11/6 | 11:3 صبح | نویسنده : مهندس سجاد شفیعی | نظرات ()