هدف آزمایش
تهیه پلی استایرن به روش پلیمریزاسیون زنجیری
تئوری آزمایش
بطور کلی ، پلیمریزاسیون زنجیری به واکنش ترکیب مولکولهای منومر با یکدیگر و تشکیل مولکولهای بزرگ پلیمری گفته میشود. در این روش ، تغییر در ترکیب عنصری بوجود نمیآید و در روند پلیمریزاسیون ، به هیچ وجه ، محصول جانبی بدست نمیآید. واکنش پلیمریزاسیون زنجیری ، برای ترکیباتی که دارای یک و یا چند بند سیر نشده میباشند، مورد استفاده قرار میگیرد.
پلی استایرنها ، پلاستیکهایی هستند که در ساخت آنها ، از منومر استایرن استفاده شده باشد. معروفترین پلاستیکها از این خانواده پلی استایرن ، پلی استایرن اصلاح شده ( ایمپکت پلی استایرن )، استایرن آکریلونیتریل (SAN ) و آکریلونیتریل بوتادین استایرن ( ABS ) است.
وسایل مورد نیاز
-
4 عدد لوله آزمایش که بوسیله شعله از قسمت دهانه کشیده شدهاند
-
4 عدد بشر 100 میلی لیتری
-
4 عدد ظرف پتری
-
استایرن
-
بنزن و یا تولوئن
-
اتیل الکل و یا اتر نفت
روش آزمایش
داخل هر یک از 4 لوله آزمایش ، 2 گرم (2,2 میلی لیتر) استایرن میریزیم. لولههای آزمایش بکمک شعله بدقت کشیده شده و مسدود میشوند. لولههای آزمایش 1 تا 4 بترتیب در دماهای ثابت 100 ، 120 ، 140 و 160 درجه سانتیگراد بمدت 3 ساعت داخل حمامهای گلیسیرین قرار داده میشوند. پس از پایان زمان فوق ، لولههای آزمایش به آرامی سرد شده و بدقت باز میشوند و بر روی هر کدام از لوله های آزمایش ، 10 الی 15 میلیلیتر بنزن و یا تولوئن جهت انحلال پلیاستایرن اضافه میشود.
باید به این نکته توجه داشت که در دماهای آزمایش بالاتر از 100 درجه سانتی گراد ، حلال بتدریج به پلیمر اضافه شود. پلیمرهای حل شده به بشرهای حاوی 40 الی 50 میلی لیتر الکل اتیلیک و یا اتر نفت ، ریخته شده ، پلیمر رسوب میکند. سپس رسوب به دقت جدا شده و دوباره با 10 الی 15 میلی لیتر رسوب دهنده شسته میشود. پلی استایرن جامد بدست آمده ، ابتدا در هوا (محیط) و سپس در اتوخلاء در دمای 60 الی 70 درجه سانتی گراد خشک شده و توزین میگردد.
نتیجه آزمایش
در قدیم ، پلی استایرن بعنوان عایق در صنایع الکتریکی مصرف میشد و همینطور زمانی بعنوان لاستیک مصنوعی بکار میرفت. ارزانی ، قالب پذیری خوب و سایر خواص پلی استایرن سبب شده که این پلیمر در اغلب صنایع مانند صنایع تولید وسایل خانگی ، صنایع غذایی ، صنایع بسته بندی ، صنایع تولید اسباب بازی و صنایع تولید عایق الکتریسته و عایق حرارت کاربرد داشته باشد.
مصارف کشپاری پلی استایرن شامل تایر ، شیلنگ ، تسمه ، کفش ، الیاف پوشش دار و عایق الکتریکی میشود. کاربردهای پلاستیکی شامل فیلم بسته بندی ، قطعات خودرو ، ظروف ، چمدان ، اسباب بازی ، لوله های آب گذر و فاضلاب ، لایههای یخچال ، محصولات اسفنجی (کولر و فنجان قهوه) و جعبه تلویزیون است. اسامی تجارتی پلی استایرن ( PS ) ، لوسترکس ، هوستیرن ، استیروسل و استیروفرم است.
سوالات
-
میتوانید تحقیق کنید و بدانید که تاریخچه تولید پلی استایرن به چه زمانی بر میگردد؟
-
فرمول گسترده پلی استایرن به چه شکلی است؟
-
میدانید چرا پلی استایرن را بعد از تولید در اتوخلاء قرار میدهند؟
چرا پلی کربنات چند جداره را برای نصب انتخاب کردیم ؟ ورق پلی کربنات چند جداره , به لحاظ ویژگی های برتر آن نسبت به شیشه در صنعت ساختمان اعتبار جدیدی برای خود باز نموده است ورقهای پلی کربنات, به لحاظ سبک بودن و مقاومت بیشتر , می تواند بطور معمول جایگزین شیشه گردد ویژگی های فیزیکی ورق های دوجداره پلی کربنات , در تقلیل صدا و عبور نور و داشتن پوشش ماورای بنفش و زیبایی , باویژگی های فیزیکی انسان همخوانی دارد
| |
اثرات بلایای طبیعی مقاومت ورق های پلی کربنات در برابر نیروهای جانبی باد و زلزله نسبت به پوششهای مشابه بیشتر است و در شرایط آسیب پذیری بر اثر زلزله , قطعات جداشده از ورق بقدری سبک است که ایراد صدمات آن به انسان و محیط در حد اول انتظار میباشد
| |
کاربرد ورق های پلی کربنات دو جداره و سه جداره
| |
![]() |
پوشش استخر
پوشش گلخانه
پوشش سقف پاساژ و بازارچه
پوشش سقف ورزشگاه
پوشش نورگیرهای منازل
پوشش نورگیرهای سالنهای صنعتی
پوشش نورگیرهای انبارها
پوشش نورگیرهای سالنهای اجتماعات
پارتیشن های جدا کننده سالن های اداری و نمایشگاه ها
|
![]() | |
![]() | |
![]() | |
![]() |
انواع تولیدات , و ابعاد محصولات
انواع تولیدات , دو نوع ساده و چندجداره می باشد
| ||||
![]() |
![]() |
| ||
| ||||
ابعاد ورقهای ساده ضخامت 2 تا 12 میلی متر حداکثر عرض 2050 میلی متر طول بنا به درخواست مشتری سایز استاندارد : 3050 * 2050 میلی متر
|
![]() | |||
| ||||
ورقهای چندجداره ضخامت 4-6 میلی متر دوجداره ضخامت 8-10 میلی متر دو جداره ضخامت 16 میلی متر سه جداره حداکثر عرض 2100 میلی متر |
Located in northern California, the Monticello Dam"s is the largest morning glory spillway all over the world. This funnel-shaped outlet, allows water to bypass the dam when it reaches capacity, as it swallows a rate of 48,400 cubic feet per second (1370 m³/s).
The distance from the funnel to the exit point - which is situated in the south side of the canyon - is about 700 feet. This type of spillway is basically a giant cement funnel. The hole"s largest diameter is 72 feet and narrows to about 28 feet. For obvious reasons, swimming near the glory hole is both prohibited and stupid. There are buoys strung across the lake to discourage boaters and swimmers from approaching the glory hole and the dam. Furthermore, the glory hole is well fenced off from the land.
گزارش کار آزمایشگاه شیمی عمومی 1 (دانشگاه امیر کبیر)
آشنایی با کامپوزیت های پلیمری 









در کاربردهای مهندسی، اغلب به تلفیق خواص مواد نیاز است. به عنوان مثال در صنایع هوافضا، کاربردهای زیر آبی، حمل و نقل و امثال آنها، امکان استفاده از یک نوع ماده که همه خواص مورد نظر را فراهم نماید، وجود ندارد. به عنوان مثال در صنایع هوافضا به موادی نیاز است که ضمن داشتن استحکام بالا، سبک باشند، مقاومت سایشی و UV خوبی داشته باشند و .... از آنجا که نمی توان مادهای یافت که همه خواص مورد نظر را دارا باشد، باید به دنبال چارهای دیگر بود. کلید این مشکل، استفاده از کامپوزیتهاست. کامپوزیتها موادی چند جزئی هستند که خواص آنها در مجموع از هرکدام از اجزاء بهتر است.ضمن آنکه اجزای مختلف، کارایی یکدیگر را بهبود میبخشند. اگرچه کامپوزیتهای طبیعی، فلزی و سرامیکی نیز در این بحث میگنجند، ولی در اینجا ما تنها به کامپوزیتهای پلیمری میپردازیم. در کامپوزیتهای پلیمری حداقل دو جزء مشاهده میشود:
تقسیم بندیهای مختلفی در مورد کامپوزیتها انجام گرفته است که در اینجا یکی از آنها را آوردهایم:
خواص کامپوزیتها به عوامل مختلفی از قبیل نوع مواد تشکیل دهنده و ترکیب درصد آنها، شکل و آرایش تقویت کننده و اتصال دو جزء به یکدیگر بستگی دارد. از نظر فنی، کامپوزیتهای لیفی، مهمترین نوع کامپوزیتها می باشند که خود به دو دستة الیاف کوتاه و بلند تقسیم میشوند. الیاف میبایست استحکام کششی بسیار بالایی داشته، خواص لیف آن (در قطر کم) از خواص توده ماده بالاتر باشد. در واقع قسمت اعظم نیرو توسط الیاف تحمل میشود و ماتریس پلیمری در واقع ضمن حفاظت الیاف از صدمات فیزیکی و شیمیایی، کار انتقال نیرو به الیاف را انجام میدهد. ضمناَ ماتریس الیاف را به مانند یک چسب کنار هم نگه میدارد و البته گسترش ترک را محدود میکند. مدول ماتریس پلیمری باید از الیاف پایینتر باشد و اتصال قوی بین الیاف و ماتریس بوجود بیاورد. خواص کامپوزیت بستگی زیادی به خواص الیاف و پلیمر و نیز جهت و طول الیاف و کیفیت اتصال رزین و الیاف دارد. اگر الیاف از یک حدی که طول بحرانی نامیده میشود، کوتاهتر باشند، نمیتوانند حداکثر نقش تقویت کنندگی خود را ایفا نمایند. الیافی که در صنعت کامپوزیت استفاده میشوند به دو دسته تقسیم میشوند: ب)الیاف طبیعی کارایی کامپوزیتهای پلیمری مهندسی توسط خواص اجزاء آنها تعیین میشود. اغلب آنها دارای الیاف با مدول بالا هستند که در ماتریسهای پلیمری قرار داده شدهاند و فصل مشترک خوبی نیز بین این دو جزء وجود دارد. از الیاف متداول در کامپوزیتها میتوان به شیشه، کربن و آرامید اشاره نمود. در میان رزینها نیز، پلی استر، وینیل استر، اپوکسی و فنولیک از اهمیت بیشتری برخوردار هستند. در بخشهای بعدی، رزینها و الیاف و روشهای شکل دهی کامپوزیتها را مورد بحث قرار دادهایم. |
این مطلب از سایت دوست عزیزم . ( عمار قاسمیان عزیزی ) اقتباس شده است
در پروژه ای تحقیقاتی که هم اکنون در دست دارم مجبور به بررسی حلال های پلی استایرن ( Polystyrene ) و پلی بوتادین ( Polybutadiene ) شدم که در این راستا حلال های تعداد دیگری از پلیمر ها را هم گردآوری کردم که در این پست در اختیار دوستان عزیزم قرار میدهم و امیدوارم که به درد پروژه های تحقیقاتی شما هم بخوره . وقت نکردم که Solubility Parameter ( پارامتر حلالیت ) مربوط به این پلیمر ها را در این پست قرار بدهم که ان شاا... در وقتی مناسب حتما اضافه میکنم ولی دوستانی که به این پارامتر ها احتیاج فوری دارند حتما با من تماس بگیرند تا براشون ارسال کنم . مجدد عرض میکنم که درخواست های علمی از جانب دانشجویان به طور رایگان پاسخ داده خواهد شد .
Repeating Unit Solvents
Acetylene Isopropylamine, aniline
Acrylamide Morpholine, water
Acrylate esters Aromatic hydrocarbons, chlorinated hydrocarbons, THF, esters, ketones
Acrylic acid Alcohols, water, dilute aqueous alkali
Acrylonitrile Phenylenediamines, ethylene carbonate, sulfuric acid
Alkyl vinyl ethers Benzene, halogenated hydrocarbons, methyl ethyl ketone
Amic acids DMF, DMSO, tetramethylurea
Aryl sulfonates DMF
Butadiene Hydrocarbons, THF, higher ketones
?
-Caprolactam (Nylon 6) m-Cresol, chlorophenol, formic acidCellulose Trifluoroacetic acid, aqueous solutions of cupriethylenediamine
Cellulose ethers Aqueous alkali
Cellulose triacetate Methylene chloride, THF, ethylene carbonate
Chloroprene Benzene, chlorinated hydrocarbons, pyridine
Ethylene Above 80°C: halogenated hydrocarbons, higher aliphatic esters and ketones
Ethylene phthalamide Sulfuric acid
Ethylene terephthalate Trichloroacetaldehyde hydrate, phenol, chlorophenol
Ethylene oxide Chloroform, alcohols, esters
Formaldehyde At elevated temperature: phenol, aniline, ethylene carbonate
Hexamethylene adipate (Nylon 6/6) Trichloroethanol, phenols, sulfuric acid
Isobutene Chlorinated hydrocarbons, THF, aliphatic ethers
Isoprene Hydrocarbons, THF, higher ketones
Lactic acid Chloroform, dioxane
Maleic anhydride Dioxane, ethers, ketones
Methacrylate esters Benzene, methylene chloride, methyl ethyl ketone
Methacrylic acid Alcohols, water, dilute aqueous sodium hydroxide
Phenylene sulfone Methylene chloride, DMSO
Phenyl glycidyl ether Xylene (hot), 1,2-dichlorobenzene (hot)
Propylene Above 80°C: halogenated hydrocarbons, higher aliphatic esters and ketones
Propylene oxide Benzene, chloroform, ethanol
Pyromellitimides m-Cresol, conc. sulfuric acid
Siloxanes Aromatic and chlorinated hydrocarbons, esters
Styrene Benzene, chlorinated aliphatic hydrocarbons, methyl ethyl ketone, ethyl acetate
Tetrafluoroethylene Perfluorokerosene (350°C)
Thiophenylene Biphenyl, dichlorobiphenyl
Ureas Phenol, m-cresol, formic acid
Urethanes Phenol, m-cresol, formic acid
Vinyl acetal Benzene, chloroform, THF
Vinyl acetate Toluene, chloroform, methanol
Vinyl alcohol Glycols (hot), water, piperazine
Vinyl butyryl Methylene chloride, alcohols, ketones
Vinyl chloride THF, methyl ethyl ketone
Vinyl carbazole Chloroform, chlorobenzene, dioxane
Vinylidene chloride THF(hot), trichloroethane
Vinylidene fluoride Cyclohexanone, ethylene carbonate
N-Vinyl pyrrolidone Chloroform, ethanol, pyridine
این مطلب از سایت دوست عزیزم . ( عمار قاسمیان عزیزی ) اقتباس شده است
Poly(phenylene oxide), or PPO, is one of those high-performance polymers we like to call engineering thermoplastics. Its biggest strength is its resistance to high temperatures. It has a very high glass transition temperature, 210 oC. But there"s a price for being heat-resistant. Most polymers are processed at high temperature in a liquid-like state. But if your polymer won"t become liquid-like at reasonable temperatures, you can"t process it! For this reason, PPO is often made into blends with high-impact polystyrene (HIPS for short). Blending PPO with HIPS makes the PPO easier to process, plus it gives PPO some resilience. PPO needs this toughening because by itself PPO can be brittle in some situations. General Electric makes PPO/HIPS blends and sells them under the name NorylTM.
Structurally, PPO is made of phenylene rings linked together by ether linkages in the 1,4 or para- positions, with a methyl group attached to carbon atoms in the 2 and 6 positions.
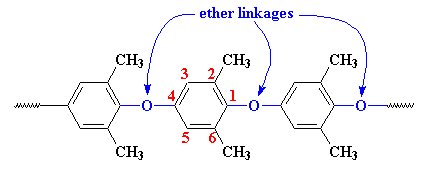
This polymer should really be called poly(2,6-dimethylphenylene oxide), but we call it poly(phenylene oxide) because we"re lazy.
PPO is made by what we call oxidative coupling polymerization of the monomer 2,6-dimethylphenol. Water is a by-product, and so this is a condensation polymerization.
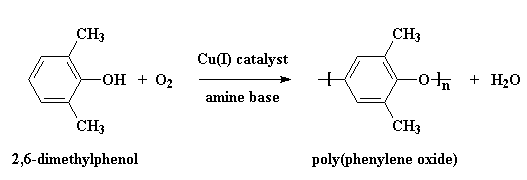
ترموپلاستیک الاستومر ها
Keywords
covalent bond, secondary interaction
We all know that elastomers are wonderful. Crosslinking makes this all possible. But crosslinked polymers can"t be recycled very easily. So in the interests of keeping the earth from becoming a giant landfill, we"ve come up with a new approach, the thermoplastic elastomer. The idea behind thermoplastic elastomers is the notion of a reversible crosslink.
Normal crosslinked polymers cannot be recycled because they don"t melt. They don"t melt because the crosslinks tie all the polymer chains together, making it impossible for the material to flow.
This is where the reversible crosslink comes in. Normal crosslinks are covalent, chemically bonding the polymer chains together into one molecule. The reversible crosslink uses noncovalent, or secondary interactions between the polymer chains to bind them together. These interaction include hydrogen bonding and ionic bonding.
The beauty of using noncovalent interactions to form crosslinks is that when the material is heated, the crosslinks are broken. This allows the material to be processed, and most importantly, recycled. When it cools again, the crosslinks reform.
Two approaches have been tried, ionomers and block copolymers.
Ionomers
Ionomers are a kind of copolymer. They are copolymers in which a small portion of the repeat units have ionic pendant groups attached to them. Not a lot, now, just a few. Normally the polymer backbone chain will be nonpolar. We all remember the rule, like dissolves like. It works here, too. The nonpolar polymer backbone chains will group together, and the polar ionic pendant groups will cluster together. Now as much as the cluster of ionic groups, snobbish as they are, would like to separate themselves completely from the nonpolar backbone chains, they can"t. Remember, they"re just sort of attached to the backbone chains. So what ends up happening is that these clusters of ionic groups serve to tie the backbone chains together, just like a normal crosslink would.
Except for one small difference. If we try, just for fun, to heat up these ionomers, something nifty and rather convenient happens. The ionic clusters will break up. When molecules get hot, they move around more. To be sure, this motion of molecules is heat itself. Moving around like this at high temperatures makes it hard for the ionic groups to stay put in their little clusters. So they break up. Now the ionomer has lost its crosslinks, and can be processed and recycled just like an ordinary polymer. Cool it back down, and the ionic clusters form again, and it acts like a crosslinked polymer again. Nifty, huh?
Block Copolymers
We can make a thermoplastic elastomer another way. That other way is called a block copolymer. A copolymer is a polymer made from more than one kind of monomer, that is, made out of two or more comonomers A block copolymer is a copolymer in which the comonomers are separated into long sections of the polymer backbone chain. Each of these sections, called blocks, looks sort of like a homopolymer.
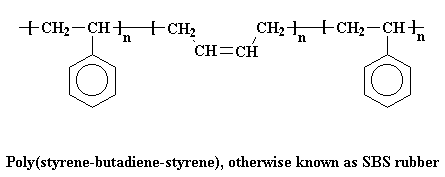
A very common thermoplastic elastomer that is a block copolymer is SBS rubber. SBS stands for styrene-butadiene-styrene, because SBS is made up of a short chain of polystyrene, followed by a long chain of polybutadiene, followed by another short chain of polystyrene. If we could stretch out a chain of SBS, it would look like the picture below.
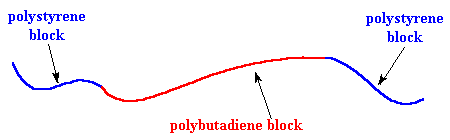
It"s time we let you folks in on a little secret: different polymers don"t mix very well. Remember the old "like dissolves like" rule? Well polymers are even more snobbish than small molecules. It"s very hard to mix two different polymers, even when they are very similar. This holds for the blocks of our SBS just as for any other polymers. So the polystyrene blocks tend to clump together and the polybutadiene blocks tend to clump together. The clusters formed by the polystyrene blocks tie the polybutadiene blocks together. Remember each polybutadiene block has a polystyrene block at each end, and the different polystyrene blocks of the same SBS molecule aren"t necessarily in the same cluster. This means that the different polystyrene clusters will be tied together by the polybutadiene blocks.
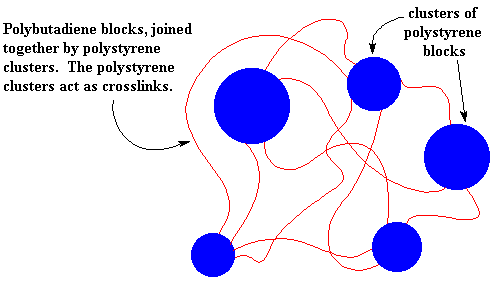
So the polystyrene clusters act as crosslinks for the polybutadiene blocks. And just like the ionic clusters of the ionomers, the polystyrene clusters break up when the SBS is heated, so it can be processed and recycled like a non-crosslinked polymer.
Being green seems to be easier than certain frogs thought!
But you can also make a thermoplastic elastomer using a block copolymer made form only one kind of monomer! I know that makes no sense, a copolymer with only one kind of monomer, but it"s true. You can make polypropylene in which there are blocks of different tacticity. One can make polypropylene with atactic blocks and isotactic blocks using metallocene catalysis polymerization, like this:
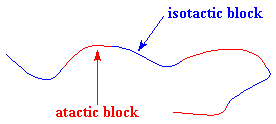
The blocks separate just as they do in SBS rubber. They separate because the isotactic blocks will form crystals, but the atactic blocks are amorphous. The result is something that looks like the picture you see on the right. It behaves as an elastomer for the same reasons as SBS rubber does.
Copyright ©2005 Polymer Science Learning Center Department of Polymer Science The University of Southern Mississippi
متاسفانه مقادیر بالایی از زباله ها مانند: فلزات، کائوچو و پلاستیک نمی توانند خورده و تجزیه شوند و برای صدها سال تجزیه نشده در طبیعت باقی می مانند. حتی اگر این مواد قطعه قطعه و خورد هم شوند باز هم نمی توانند تجزیه شوند و به مرور اتمسفر، زمین و آب را آلوده می کنند.
بعضی از این مواد می توانند بازیافت شوند. زباله هایی که قابل بازیافت نیستند در گودالهایی به نام محل دفن زباله مدفون می شوند. این زباله ها ابتدا تکه تکه و سپس له و خمیر مانند می شوند بنابراین با این کار زباله ها فضای کمتری را اشغال می کنند. اگر نتوانیم به روند بازیافت ادامه دهیم باید روز به روز بر تعداد این گودالها بیافزاییم.
ضرورت بازیافت زمانى بیشتر مشخص مى شود که بدانیم برای تولید یک تن کاغذ جدید، باید 15 درخت تنومند راقطع کنیم. اگر از کاغذ باطله دوباره کاغذ تهیه کنیم در مصرف آب 90 درصد و انرژی 50 درصد سود برده و در کنترل آلودگى هوا 75 درصد موثر بوده ایم
در ایران براى بازیافت کاغذ، اولین کارخانه در سال 1313 در کرج تاسیس شد
بازیافت پلاستیک
در ساخت انواع ظروف و کیسه هاى پلاستیکى از انواع مواد پلیمرى استفاده مى شود. با توجه به قابلیت بازیابى اکثر پلیمرها، مى توان مواد پلاستیکى را پس از مصرف و دور انداختن مجدداً طى فرایند بازیافت مورد استفاده قرار داد. مسئله مهم و اساسى در این میان استفاده از مواد بازیافت شده در مصارف غذایى است. در واقع صحبت از آن دسته از مواد بازیافت شده اى است که براى بسته بندى و نگهدارى مواد غذایى غیرمجاز هستند در ساخت ظروف پلاستیکى مختلف، مواد پلیمرى متفاوتى به کار برده مى شود به عنوان مثال:
?- ظروف نوشابه هاى گازدار از جنس پلى اتیلن تترافتالات (PET)
?-شیشه های شیرخورى کودکان از جنس پلى کربنات ( PC ) به دلیل گران بودن پلى کربنات ها این نوع پلیمرها کمتر در بسته بندى مواد غذایى استفاده شده و بیشتر در ساخت شیشه هاى شیر کودکان به کار مى روند.
?-ظروف بسته بندى لبنیات از جنس پلى اتیلن(PE) ، پلى پروپیلن(PP) و پلى استایرن(PS)
?- ظروف یک بار مصرف از جنس PS وPP
?- کیسه هاى پلاستیکى از جنس پلی اتیلن . این نوع کیسه ها به اشتباه تحت عنوان کیسه هاى نایلونى معروفند.
قابل ذکر است این مواد پلاستیکى مى توانند حاوى رنگ باشند که در آن صورت از رنگدانه پلاستیک (مستربچ) استفاده مى شود
نحوه ساخت کیسه هاى پلاستیکى
گرانول هاى پلى اتیلن را به شکل فیلم هاى نازک درآورده و پس از برش فیلم ها در ابعاد دلخواه به کیسه تبدیل مى کنند. و در صورت تولید کیسه هاى رنگى هنگام تبدیل گرانول پلى اتیلن به فیلم از رنگدانه پلاستیک یا مستربچ (به مقدار یک تا پنج درصد) استفاده مى کنند.
نحوه ساخت ظروف یک بار مصرف
ابتدا مواد پلیمررا به صورت فیلم هایى با ضخامت مورد نظر تبدیل کرده و سپس با استفاده از قالب هایى خاص به اشکال مختلف تبدیل مى شوند.
بازیافت مواد
در فرایند بازیافت مواد پلاستیکى نوع پلیمرى که باید بازیافت شود مدنظر قرار مى گیرد.بدین ترتیب که هر نوع پلیمر جدا از انواع دیگر بازیافت مى شوند، در غیر این صورت فرایند بازیافت با اشکال روبه رو خواهد شد. به عنوان مثال: پلى اتیلن ها با هم، پلى پروپیلن ها با هم و پلى آمیدها با هم بازیافت مى شوند، چرا که هنگام فرایند بازیافت مواد پلاستیکى را خرد سپس ذوب کرده و مجدداً مورد استفاده قرار مى دهند بنابراین اگر ترکیبى از مواد پلاستیکى مختلف نظیر ظروف یک بار مصرف با انواع مختلف خرد و سپس ذوب شوند، با توجه به متفاوت بودن نقطه ذوب ترکیب ناهمگونى ایجاد مى شود. مسئله بعدى نداشتن رنگ در مواد پلاستیکى است که اهمیت بسزایى در فرایند بازیافت دارد. به دلیل اینکه پلیمرهاى رنگى داراى رنگ یکنواختى نیستند پس از بازیافت رنگ تیره پیدا مى کنند در نتیجه کارخانه هاى سازنده براى به دست آوردن یک رنگ ثابت از دوده استفاده کرده سپس مواد پلیمرى مذاب را به صورت فیلم درآورده و به کیسه پلاستیکى تبدیل مى کنند، که ما از آنها به صورت کیسه هاى زباله مشکى استفاده مى کنیم.گاهى به دلیل کاربرد ناصحیح دوده تماس دست با این کیسه ها باعث جذب ذرات دوده از راه دست مى شود. بنابراین در حال حاضر کارخانه هاى صنایع غذایى مجاز نیستند مواد بازیافتى را براى نگهدارى و بسته بندى مواد غذایى به کار ببرند. دلیل اصلى آن نیز عدم رعایت اصول بازیافت مواد پلاستیکى در ایران است. گفتنى است براى تولید کیسه هاى پلاستیکى شفاف از مواد اولیه بکر استفاده مى شود در حالى که اکثریت پلاستیک هاى مشکى موجود در بازار از مواد بازیافتى تهیه مى شود.
مناسب بودن پلاستیک ها در کاربردهاى غذایى
تمامى پلیمرها از بکر تا آنهایى که بازیافتى بوده و همچنین ظروف پلاستیکى حتماً باید قبل از استفاده در صنعت غذایى تحت آزمون Food grade قرار بگیرند( ای.سی.سی) . با انجام آزمون هایى که در اداره کل آزمایشگاه هاى کنترل غذا و دارو نیز قابل اجرا هستند میزان مهاجرت مواد سازنده پلیمرها به سمت مواد غذایى مشابه سنجیده مى شود. در واقع وزارت بهداشت مقاومت و میزان مهاجرت مواد سازنده پلیمرها را در حلال ها یا محلول هاى مشابه مواد غذایى مى سنجد..
بطرى هاى آب و نوشابه از جنس (پت) هستند این ظروف در صورتی که food grade باشند از نظر بهداشتى مشکل ایجاد نمى کنند. تنها مسئله وجود ماده استالدئید در این ظروف است که باعث تغییر طعم و بوى آب و مواد نوشیدنى مى شود البته میزان مهاجرت استالدئید در حدى نیست که خاصیت بیمارى زایى داشته باشد.
مشکل دست زدن به کیسه هاى زباله
پلاستیک هاى مشکى که در حال حاضر در بازار هستند هیچ کدام براى مصارف غذایى مناسب نیستند و مشخص نیست کجا و تحت چه شرایطى تولید شده اند. این مواد در اثر تماس با مواد غذایى آنها را آلوده کرده و عوارضى را براى انسان به دنبال خواهند داشت. گفتنى است اگر مواد پلاستیکى پس از بازیافت براساس پایه پلیمرى خود مشکل نداشته و به آزمون هاى Food grade پاسخ دهند براى نگهدارى و بسته بندى مواد غذایى مناسب خواهند بود.
پلاستیک هایی که بوی بنزین می دهند
یکی از پژوهشگران دانشگاه صنعت نفت موفق به اجرای طرحی شده است که براساس آن 80درصد از پسماندهای موجود در زباله های شهری ، صنعتی و پزشکی طی فرآیندی به سوخت مایع (بنزین و گازوئیل ) تبدیل می شود و به این ترتیب نه تنها به کاربرد مفید ضایعات پلیمری ، بلکه به تامین خوراک راکتورها در صنایع پتروشیمی و نفت نیز کمک می شود.
کسانی که به پژوهش های انجام شده در عرصه های پتروشیمی و نفت علاقه مندند، می دانند که یکی از معضلات اساسی در این صنایع ، بحث کنترل و کاهش اثرات سو زیست محیطی است؛ هر چند طی یک دهه اخیر، موضوع پسماندهای پالایشی و فرآورده های سنگین هیدروکربنی به عنوان یکی از معضلات صنعت پالایشگاهی کشور مطرح بوده است.
بر این اساس تلاش محققان و نیروهای علمی صنعت نفت کشور نیز طی این مدت به تبدیل مواد سنگین هیدروکربنی به مواد سبک مانند بنزین و گازوئیل معطوف شده است.
به طور کلی دو روش اصلی برای حل مشکل زباله های پلاستیکی وجود دارد:
?. بازیافت
?. تولید پلاستیک های زیست تخریب پذیر
بازیافت به فرایندهایی گفته می شود که در آنها از زباله های پلاستیکی به نحوی استفاده می شود.
روش های بازیافت در سه دسته جای می گیرند:
?- بازیافت انرژی
?- بازیافت مکانیکی
?- بازیافت شیمیایی
در بازیافت انرژی زباله به عنوان یک سوخت سوزانده می شود. باید توجه کرد که بازده انرژی (انرژی حاصل از سوختن واحد وزن سوخت) پلاستیک ها نسبت به سوخت های فسیلی مرسوم بیشتر است.
بازیافت مکانیکی ، یعنی خرد کردن و استفاده یک محصول پلاستیکی در ساخت یک قطعه. در این روش باید نکات زیادی رو در نظر گرفت. مثلا برای ساخت قطعات حساس تر سازمان های مربوطه مقدار مجاز پلاستیک بازیافتی در قطعه را تعیین می کنند.
در بازیافت شیمیایی پلاستیک به وسیله روش های شیمیایی به مواد دیگری (اغلب مواد اولیه یا میانی) تبدیل میشود. این روش نسبت به دو روش دیگه جدیدتر است ولی هنوز از نظر اقتصادی به صرفه نیست. اما بسیار مورد توجه هست. به عنوان مثال میشود به تهیه رزین پلی استر از بطری های نوشابه (از جنس پلی اتیلن ترفتالات یا PET ) اشاره کرد.
اما در کنار بازیافت از چندین سال پیش تلاش هایی در جهت تولید پلاستیک های زیست تخریب پذیر شروع شده که الان به نتیجه هم رسیده است. این پلاستیک ها قابلیت بازگشت به طبیعت را طی زمانی قابل قبول دارند.
این پلاستیک ها هم در دو دسته کلی قرار می گیرند:
?- پلاستیک های متداول حاوی مواد تخریب پذیر
?- پلاستیک های تخریب پذیر ذاتی
پلاستیک های متداول حاوی مواد تخریب پذیر آمیزه هایی هستند که در آنها یک ماده تخریب پذیر(مانند نشاسته) به یک پلاستیک متداول (مثل پلی اتیلن) اضافه میشود و تخریب این ماده به افزایش سرعت تخریب پلاستیک کمک می کند. این مواد چند سالی هست که وارد بازار شده اند و با اون که کمک زیادی به کاهش زباله های پلاستیکی کرده اند، اما به دلیل این که اولا در انها از همان پلاستیک های متداول تخریب ناپذیر استفاده شده و دوما استفاده از مقدار زیادی مواد تخریب پذیر در پلاستیک ویژگی ها را تضعیف می کنه، موقعیت چندان محکمی ندارند.
پلاستیک های تخریب پذیر ذاتی موادی هستند که به دلیل ساختمان شیمیایی خاصشان به وسیله باکتری ها، آب یا آنزیم ها در طبیعت تخریب می شوند. مهم ترین پلاستیک از این نوع پلی(لاکتیک اسید) هست که از اسید لاکتیک تهیه میشود. پیش بینی میشود این پلاستیک، که خواص بسیار خوبی هم داره، در آینده رقیبی بسیار جدی برای پلاستیک های متداول امروزی به خصوص در صنعت بسته بندی باشد. مشکل بزرگ این مواد، گران بودنشان است که در حال حاضر تحقیقات برای توسعه یک روش ارزان برای تولیدشان ادامه دارد. جالب این که منابع اصلی تولید این پلاستیک طبیعی هستند و از محصولات نفتی برای ساخت آنها استفاده نمی شود.
پلاستیک های زیستی
اطرافمان انباشته از پلاستیک شده است. هر کاری که انجام می دهیم و هر محصولی را که مصرف می کنیم، از غذایی که می خوریم تا لوازم برقی به نحوی با پلاستیک سرو کار داشته و حداقل در بسته بندی آن از این مواد استفاده شده است.
گرچه بسته بندی پلاستیکی با قیمتی نازل امکان حفاظت عالی از محصولات مختلف خصوصاً مواد غذایی را فراهم می کند ولی متاسفانه معضل بزرگ زیست محیطی حاصل از آن گریبانگیر بشریت شده است. اکثر پلاستیک های معمول در بازار از فرآورده های نفتی و ذغال سنگ تولید شده و غیر قابل بازگشت به محیط هستند و تجزیه آنها و برگشت به محیط چند هزار سال طول می کشد.
به منظور رفع این مشکل، محققان علوم زیستی در پی تولید پلاستیک های زیست تخریب پذیر از منابع تجدید شونده مثل ریزسازواره ها و گیاهان می باشند.
واژه زیست تخریب پذیر یا Biodegradable به معنی موادی است که بسادگی توسط فعالیت موجودات زنده به زیر واحدهای سازنده خود تجزیه شده و بنابراین در محیط باقی نمانند.
استانداردهای متعددی برای تعیین زیست تخریب پذیری یک محصول وجود دارد که عمدتاً به تجزیه 60 تا 90 درصد از محصول در مدت دو تا شش ماه محدود می گردد. این استاندارد در کشورهای مختلف متفاوت است.
اما دلیل اصلی زیست تخریب پذیر نبودن پلاستیک های معمول، طویل بودن طول مولکول پلیمر و پیوند قوی بین مونومرهای آن بوده که تجزیه آن را توسط موجودات تجزیه کننده با مشکل مواجه می کند.
در این بین تولید پلیمرهای زیستی جایگاه خاصی دارند. تولید اینگونه پلیمرها توسط طیف وسیعی از موجودات زنده مثل گیاهان، جانوران و باکتری ها صورت می گیرد. چون این مواد اساس طبیعی دارند، بنابراین توسط سایر موجودات نیز مورد مصرف قرار می گیرند و تجزیه کنندگان از جمله مهم ترین این موجودات زنده در موضوع مورد بحث ما می باشند.
برای بهره برداری از این پلیمرها در صنعت دو موضوع باید مورد توجه قرار گیرد:
الف) دید محیط زیستی: این مواد باید سریعاً در محیط مورد تجزیه قرار گیرند، بافت خاک را بر هم نزنند و به راحتی با برنامه های مدیریت زباله و بازیافت مواد از محیط خارج شوند.
ب) دید صنعتی: این مواد باید خصوصیات مورد انتظار صنعت را از جمله دوام و کارایی را داشته باشند و از همه مهمتر، پس از برابری یا بهبود کیفیت نسبت به مواد معمول، قیمت تمام شده مناسبی داشته باشند.
نکته ای که نباید از نظر دور داشت این است که علی رغم قیمت بالاتر تولید پلاستیک های زیست تخریب پذیر، چه بسا قیمت واقعی آنها بسیار کمتر از پلاستیک های سنتی باشد؛ چرا که بهای تخریب محیط زیست و هزینه بازیافت پس از تولید هیچ گاه مورد محاسبه قرار نمی گیرد.
تقریباً تمامی پلاستیکهای معمول در بازار از محصولات پتروشیمی که غیر قابل برگشت به محیط میباشند، به دست میآیند. راهحل جایگزین برای این منظور، بهرهبرداری از باکتری های خاکزی است . باید منتظر بود تا سرانجام شاهد تولید اقتصادی این محصولات دوستدار محیط زیست در آیندهای نزدیک بود

این پلیمرها بتازگی در بین مواد پلاستیکی ظهور کرده است. این مواد از استحکام ابعادی بسیار خوب ، مقاومت بالا ، مقاومت در مقابل مواد شیمیایی توام با خاصیت سهولت شکل پذیری برخوردار هستند. از این پلیمرها میتوان به پلی اتیلن با چگالی کم قابل مصرف در ساخت عایق الکتریکی ، وسایل خانگی ، لوله و بطریهای یکبار مصرف ، پلی اتیلن با چگالی بالا قابل مصرف در ظروف زبالهها بطری ، انواع مخازن و لوله برای نگهداری و انتقال سیالات ، پلی اتیلن شبکهای ، پلی پروپیلن قابل مصرف در ساخت صندوق ، قطعات کوچک خودرو ، اجزای سواری ، اسکلت صندلی ، اتاقک تلویزیون و... اشاره نمود.
پلیمرهای زیست تخریب پذیر
این پلیمرها در طی سه دهه اخیر در تحقیقات بنیادی و صنایع شیمیایی و دارویی بسیار مورد توجه قرار گرفتهاند. زیست تخریب پذیری به معنای تجزیه شدن پلیمر در دمای بالا طی دوره مشخص میباشد که بیشتر پلی استرهای آلیفاتیک استفاده میشود. از این پلیمرها در سیستمهای آزاد سازی دارویی با رهایش کنترل شده یا در اتصالات ، مانند نخهای جراحی و ترمیم شکستگی استخوانها و کپسولهای کاشتی استفاده میشود.
پلی استایرن
این پلیمر به صورت گستردهای در ساخت پلاتیکها و رزینهایی مانند عایقها و قایقهای فایبر گلاس در تولید لاستیک ، مواد حد واسط رزینهای تعویض یونی و در تولید کوپلیمرهایی مانند ABS و SBR کاربرد دارد. محصولات تولیدی از استایرن در بسته بندی ، عایق الکتریکی - حرارتی ، لولهها ، قطعات اتومبیل ، فنجان و دیگر موادی که در ارتباط با مواد غذایی میباشند ، استفاده میشود.
لاستیکهای سیلیکون
مخلوط بسیار کانی- آلی هستند که از پلیمریزاسیون انواع سیلابها و سیلوکسانها بدست میآیند. با اینکه گرانند ولی مقاومت قابل توجه در برابر گرما به استفاده منحصر از این لاستیکها در مصارف بالا منجر شده است. این ترکیبات اشتغال پذیری نسبتا پایین ، گرانروی کم در درصد بالای رزین ، عدم سمیت ، خواص بالای دی الکتریک ، حل ناپذیری در آب و الکلها و ... دارند به دلیل همین خواص ترکیبات سیلیکون به عنوان سیال هیدرولیک و انتقال گرما ، روان کننده و گریس ، دزدگیر برای مصارف برقی ، رزینهای لایه کاری و پوشش و لعاب مقاوم در دمای بالا و الکلها و مواد صیقل کاری قابل استفادهاند. بیشترین مصرف اینها در صنایع هوا فضاست.
لاستیک اورتان
این پلیمرها از واکنش برخی پلی گلیکولها با دی ایزوسیاناتهای آلی بدست میآیند. مصرف اصلی این نوع پلیمرها تولید اسفنج انعطاف پذیر و الیاف کشسان است. در ساخت مبلمان ، تشک ، عایق - نوسانگیر و ... بکار میروند. ظهور نخ کشسان اسپندکس از جنش پلی یوره تان به دلیل توان بالای نگهداری این نوع نخ زمینه پوشاک ساپورت را دگرگون کرده است.
انواع پلیمرها
پلیمرها را به سه گروه عمده تقسیم میکنند:
• بیوپلیمرها یا پلیمرهای طبیعی مانند سلولز ، نشاسته ، پروتئینها و ...
• پلیمرهای معدنی مانند الماس ، گرافیت ، اکثر اکسیدهای فلزی و ...
• پلیمرهای سنتزی پلیمرهایی هستند که منشا آنها عموما مونومرهایی از نفت خام و قطران زغال سنگ است و ما با انجام فرآیندهایی پلیمرهای بسیار مفید میسازیم که امروزه زندگی بدون آنها ممکن نیست. با این فرایندها بطور کلی آشنا میشویم.
پلیمریزاسیون افزایشی
در این نوع پلیمریزاسیون ، از ترکیباتی که بند دوگانه (C ? C) دارند، پلیمر میسازند. مثل تولید پلی اتیلن از اتیلن.
پلی اتیلن
C2H4 ? (? C2H4 ?)n
این واکنش در اثر حرارت به پلی اتیلن تبدیل میشود. جرم مولکولی پلی اتیلن بین 1000 تا 20000 میتواند متفاوت باشد. یعنی بر حسب شرایط ، درجه پلیمریزاسیون یعنی همان n مولکول پلیمر را میتوان کم یا زیاد کرد.
آکریلان
n(CH2 ? CHCN) ? (? CH2 ? CHCN?)n
این پلیمر نیز از مشتقات اتیلن است. مونومر این پلیمر ، سیانید ونیل (آکریکونیتریل) است.
PVC
CH2 ? CHCl ? (? CH2 ? CHCl)n
پلی وینیل کلراید یا PVC نیز از پلیمریزاسیون کلرید وینیل CH2 ? CHCl بوجود میآید.
کائوچو
کائوچو بر دو نوع است:
• کائوچوی طبیعی :
کائوچوی طبیعی از شیره درختی به نام Hevea بدست میآید، از پلیمریزاسیون هیدروکربنی به نام 2- متیل -3 , 1- بوتادین معروف به ایزوپرن به فرمول CH2 ? C (CH3) ? CH ? CH2 بوجود میآید:
CH2 ? C (CH3) ? CH ? CH2 ? (? CH2 ? C CH3 ? CH ? CH3)n
با توجه به فرمول ساختمانی کائوچوی طبیعی میبینیم که در مونومر آن هنوز یک بند دوگانه وجود دارد.
• کائوچوی مصنوعی :
چون در فرمول ساختمانی کائوچوی طبیعی پیوند دوگانه وجود دارد، به همین دلیل وقتی کائوچو را با گوگرد حرارت دهیم، این مونومرها پیوند ? خود را باز میکنند و ظرفیتهای آزاد شده ، اتم گوگرد را میگیرند. در نتیجه کائوچو به لاستیک تبدیل میگردد. حرارت دادن کائوچو با گوگرد و تولید لاستیک را اصطلاحا ولکانیزاسیون (Vulcanization) مینامند و به همین دلیل لاستیک حاصل را نیز کائوچوی ولکانیزه گویند.
چند نوع کائوچوی مصنوعی نیز ساختهاند که از موادی مانند 3 , 1- بوتا دیان <CH22 و جسمی به نام 2- کلرو 3 , 1- بوتادین معروف به کلروپرن به فرمول CH2 ? CHCl ? CH ? CH2 و جسم دیگری به فرمول CH2 ? C(CH3) ? C(CH3) ? CH2 به نام 3 , 2- دی متیل – 3 , 1- بوتادین به تنهایی یا مخلوط درست شدهاند.
کلروپرن به سهولت پلیمریزه شده و به نوعی کائوچوی مصنوعی به نام نئوپرن تبدیل میشود.
پلیمریزاسیون تراکمی
اگر در یک پلیمریزاسیون ، بر اثر واکنش مونومرها با هم ، مولکولهای کوچکی مثل H2O و NH3 و ... خارج شوند، این نوع پلیمریزاسیون را تراکمی مینامند. مثل پلمیریزاسیون گلوکز در تولید نشاسته و سلولز که منجر به خارج شدن آب میگردد و یا مثل بوجود آمدن نایلون که مانند مواد پروتئینی یک پلی آمید است و پلیمر شدن یک آمین دو ظرفیتی به نام هگزا متیلن دی آمین به فرمول NH2 ? (CH2)6 ? NH2 با یک اسید دو ظرفیتی به نام اسید آدیپیک HOOC ? (CH2)4 ? COOH بوجود میآید. در این عمل ، عامل OH_ اسید از دو طرف با هیدروژن گروه آمین NH2_ تشکیل آب داده و خارج میشوند و باقیماندههای مولکولهای آنها با هم زنجیر پلیمر را بوجود میآورند. به شکل زیر:
... + NH2 ? (CH2)4 ? NH2 ? HOOC ? (CH2 ? COOH + ...
نایلون:nH2O + (? NH ? (CH2)6 ? N(H) ? CO ? (CH2)4 ? CO ?)n
پلیمریزاسیون اشتراکی (کوپلیمریزاسیون)
اگر در عمل پلیمریزاسیون ، 2 مونومر مختلف با هم مشترکا پلیمر شوند و یک پلیمر را بوجود آورند، آن را کوپلیمر مینامند. مثلا یک نوع لاستیک وجود دارد، به نام بونا _ S که از پلیمریزاسیون دو جسم مختلف یکی به نام 3 , 1- بوتا دیان CH2 ? CH ? CH ? CH2 و دیگری به نام وینیل بنزن (استیرن) C6H5 CH ? CH2 بوجود میآید که قسمتی از فرمول ساختمانی آن به شکل زیر است:
--CH2 ? CH ? CH ? CH2 ? CH(C6H5) ? CH2--
شیمی نایلون:
پلی کندانسیون یا پلیمریزاسیون تراکمی
اگر در یک پلیمریزاسیون بر اثر واکنش منومرها باهم ، مولکولهای کوچکی مثل NH3 ، H2O و ... خارج شوند، پلیمریزاسیون را پلی کندانسیون یا تراکمی مینامند. مثل پلیمریزسایون گلوکز در تولید نشاسته و سلولز که منجر به خارج شدن آب میگردد و یا مثل بوجود آمدن نایلون که مانند مواد پروتئینی یک پلی آمید است و از پلیمر شدن یک آمید دو ظرفیتی به نام هگزامتیلن دی آمین به فرمول: NH2 - (CH2)6 - NH2 با یک اسید دو ظرفیتی به نام اسید آدیپیک به فرمول HOOC - (CH2)4 - COOH بوجود میآید.
در این عمل عامل OH – اسید از دو طرف با هیدروژن گروه آمین NH2 – تشکیل میدهند و خارج میشوند و باقیمانده مولکولهای آنها زنجیر پلیمر را بوجود میآوردند. به عبارت دیگر واکنش چند تراکمی از متراکم شدن دو عامل مختلف از دو منومر مختلف و یا از متراکم شدن دو عامل مختلف از یک مولکول با همان مولکول پلیمر سنتز میشود.
پلی آمیدها
پلی آمیدها شامل سه نوع نایلون ، نایلون 6و 6 نایلون 11 میباشد. همانطور که ذکر شد، پلی آمیدها از طریق واکنشهای چند تراکمی یا پلی کندانسیون بوجود میآید.
نایلون 6
نایلون 6 و 6 از باز شدن حلقه کاپرولاکتام در حضور آغازگر N - بنزوئیل ? - پیرولیدون و کاتالیزور سدیم آمید NH2Na بدست میآید. ماده اولیه کاپرولاکتام ، بنزن است. از کاپرولاکتام در محیط عمل به مقدار بسیار زیاد داریم. ولی NH2Na2 ، چون به عنوان آغازگر بکار میرود، تنها به مقدار بسیار اندک داریم که آغاگر حلقه بوده و بعد از آن ، واکنش پیش خواهد رفت.
نایلون 6 و 6
همانطور که گفته شد، نایلون 6 و 6 از متراکم شدن اسید آدیپیک و هگزا متیلن دی آمین در حضور حرارت و حذف یک مولکول آب ایجاد میگردد.
یک مولکول آب + نایلون 6 و 6 <---------- HOOC-(Ch2)4-COOh + NH2-(CH2)6-NH2 + حرارت
نایلون 11
نایلون 11 فرآورده بسیار مهمی است که از متراکم شدن آمینو اندوکانوئیک اسید که از روغن گرچک گرفته میشود، بوجود میآید و پلی آمید Rilsan یا Nylon11 نامیده میشود. از متراکم شدن این ماده نیز در حضور حرارت ، آب آزاد میشود. Rilsan بهترین الیاف پارچه محسوب میشود. چون رنگ پذیری و استحکام بالایی دارد.
خواص و کاربردهای نایلون
بیشترین کاربرد نایلونها در تهیه الیاف پارچه و صنایع نساجی است و در تهیه قطعات صنعتی نیز کاربرد دارند. نایلونها قدرت مکانیکی خوبی دارند و به این علت در این صنایع استفاده میشوند. این پلیمرها ، نقطه ذوب بالایی دارند. چون در بین زنجیرهای پلیمر ، پیوند هیدروژنی ایجاد شده است. این پلیمرها کمتر در حلالها حل میشوند، اما قابل انحلال در اسید فرمیک و پلی آمیدها هستند.