مزایا و معایب پوشش ھای پودری : ?
آنچھ کھ امروزه جایگزین رنگھای عادی کوره ای بر پایھ حلال صنعتی بعنوان پوشش ھای عاری از
حلال شده است ، پوشش ھای پودری می باشند کھ مرتبا با آنھا مقایسھ می شوند . با این وجود سیستمھای
روکش ھای سخت شونده با اشعھ ، (Water Base) مناسب " تکنولوژی پاک " مثل پوششھای بر پایھ آب
برای مقایسھ وجود دارد . (High Solid ) و پوشش ھای با درصد جامد بالا
از مزایای عمده ای کھ پوشش ھای پودری دارند بھ اختصار میتوان بھ موارد ذیل اشاره نمود :
1) آماده برای مصرف و کاربرد
2) سھولت استفاده
3) کاربرد تک لایھ ، لایھ ای ضخیم با یکنواخت بھتر با یکبار پاشش نسبت بھ رنگ مایع بدست می آید.
?) نمونھ برگشتی کمتر
?) سودمندی بالا ، بازیافت مطلوب پودرھای پاشیده شده اضافی بالای 9? % می باشد در حالی کھ برای
رنگھای بر پایھ حلالی کمتر از 1? % می باشد.
?) رسوب یا تھ نشینی ندارد .
7) عاری از حلال می باشد .
8) خطرات سلامتی کمتر ، بعلت عدم وجود حلال و مواد خطرناک آتشگیر و مسموم کننده .
معایب : ?
1) آلودگی ، مانند حضور ذرات خارجی کھ بعد از عمل پخت دیگر نمی توان از بین برد .
2) تغییر رنگ ، دقت در تمیز کاری دستگاھھای اعمال رنگ مثل کابین پاشش و مسیر بازیافت
ضروریست .
3) تنظیم مشخصات پودر در حین ساخت امکان پذیر نیست . برخلاف رنگھای مایع کھ اغلب بھ ھنگام
اعمال میتوان آنھا را تینت نمود ، این کار برای رنگھای پودری امکان پذیر نیست
.
بازار رنگھای پودری : ?
مصارف رنگ ھای پودری را می توان بھ دو گروه مجزا تقسیم کرد :
الف ) مصارف تزئینی :
پوشش تزئینی نھایی را در محصولات ساختھ شده ایجاد می نماید مانند : لوازم خانگی ، ابزار ماشین
الات و ...
ب) مصارف ویژه :
در اینگونھ مصارف کاربرد تزئینی نداشتھ و برای خواص اجرایی ویژه استفاده می شوند مانند: خواص
حفاظت برای لولھ ھا و شیرآلات و اتصالات و ...
فرایند ساخت پوشش ھای پودری ?
روش متداول برای ساخت رنگ ھای پودری ، روش اختلاط مذاب مواد اولیھ مورد استفاده در اکسترودر
می باشد کھ پس از آن بھ ذرات ریز تبدیل می شوند
.
ھشت مرحلھ مشخص برای روش ساخت معمولی ( اختلاط مذاب) وجود دارد :
1) وزن کردن مواد اولیھ
( Premix ) 2) پیش اختلاط
3) اکستروژن
?) سرد نمودن و خرد نمودن
?) آسیاب و کنترل اندازه ذرات
?) فیلتر نمودن ( الک کردن )
(Dry Blending ) 7) ھموژنھ کردن یا اختلاط خشک
8) بستھ بندی
تمامی مراحل فوق مھم است ولی سھ فرایند کلیدی پیش اختلاط ، اکستروژن و آسیاب ، از مراحل اصلی
تولید پوشش پودری م یباشند .
1) پیش اختلاط
ھدف از این مرحلھ ایجاد یک مخلوط ھموژن از مواد اولیھ قبل از مرحلھ اکستروژن می باشد کھ نھایتا
موجب ایجاد ھمرنگی و خواص ویژه در پودر می گردد . بنابر این در این مرحلھ بکمک اکستروژن
آزمایشگاھی ھمرنگی بایستی کنترل شود
2) اکستروژن
سھ نوع اکستروژن برای ساخت رنگ پودری وجود دارد :
- تک پیچھ
- دو پیچھ ھم دوران
Tooth Planetary Roller -
اینھا بگونھ ای طراحی شده اند کھ توزیع ماکزیمم ، حداقل زمان ماندگاری و کنترل دقیق دمای مذاب را
داشتھ باشند .
فرایند ھای متعددی در حین اکستروژن صورت م یگیرد کھ کلا بھ آنھا توزیع یا پراکندگی ذرات اطلاق
می شود . این فرایندھا بطور مجزا عمل نمی کنند و تا حدی ھمزمان صورت می گیرند.
این فرایندھا عبارتند از :
- ذوب ، اختلاط و یکنواختی اجزای رزین
رنگدانھ ھا توسط اجزای رزینی و توزیع افزودنی ھا در مذاب Wetting -
- شکست رنگدانھ ھای بھم چسبیده بطور ایده آل بھ ذرات اولیھ.
حرارت ابتدائی اکسترودر برای اطمینان از ذوب رزین نیاز است ، ولی در خلال تولید پیوستھ انرژی
مکانیکی حاصل از اصطکاک مواد برای تامین حرارت کفایت می کند و جداره داخلی اکسترودر برای
ثابت نگھداشتن دما بایستی سرد نگھ داشتھ شود .
مواد خروجی از اکسترودر باید بلافاصلھ بصورت ورقھ ای نازک سرد شده و بصورت چیپس برای
استفاده در آسیاب خرد گردند .
3) آسیاب و کنترل اندازه ذرات
0- رنگھای پودری الکترواستاتیک برای کاربردھای مرسوم معمولا توزیع اندازه ذراتی در محدوده 100
10 میکرون است . - میکرون دارند ، ولی محدوده ای کھ خواص کاربردی خوبی را ارائھ می دھند ?0
مقادیر زیاد ذرات ریز زیر 10 میکرون ، پودری با بارپذیری کم الکترواستاتیکی و خواص سیالیت
ارائھ م یدھند ، ھمچنین وجود ذرات درشت پوشش ھای با ظاھر نامطلوب (Flowability ) ضعیفی
ارائھ می دھند.
معمولا برای خرد کردن رنگ ھای پودری مورد استفاده قرار می گیرند . آنھا Pindisc آسیاب ھای
شامل یک کلاسیفایر داخلی برای کنترل ماکزیمم اندازه ذرات ھستند و ذرات درشت خارج از اندازه
دوباره بھ آسیاب یر می گردند . یک فن با حجم بالا، ھوا را بھ داخل آسیاب می کشاند ، این امر سبب
اتلاف حرارت ایجاد شده و ھمچنین انتقال ذرات پودر م یگردد . با کنترل زمان اقامت ذره در داخل
آسیاب و سرعت کلاسیفایر توزیع اندازه ذرات می تواند کنترل شود .
جمع آوری پودرھای حمل شده با جابجایی ھوا توسط سیکلون انجام میشود .ذرات بالای 10 میکرون و
مقدار جزئی از ذرات با اندازه کمتر بستھ بھ بازدھی سیکلون از آن خارج شده و بھ عنوان محصول جمع
آوری می شوند .
پودرھای خروجی از سیکلون قبل از ورود بھ محل بستھ بندی از میان یک الک پیوستھ ، عبور داده
از آن جدا گردد . جمع آوری مستقیم ھمھ پودرھا (over site ) میشوند تا ذرات بالای اندازه مورد نیاز
از فیلتر نیز ممکن است .
رزین ھای جایگزین در پوشش ھای پودری
داشت: پایداری اولین پوشش ھای پودری بھ دلیل مصرف زیاد رزین اپوکسی دو مشکل جدی وجود در
در مقابل نور UV رو کاربردھایشان بھ استفاده در داخل و مقاومت زردگرایی آن ھا ضعیف بود. از این
شد. برای غلبھ بر چنین مشکلاتی، تحقیقاتی توسط شرکت ساختمان و مصارف غیر تزئینی محدود می
با ھدف ساخت سامانھ ھای مقاوم تر صورت گرفت. این پژوھش ھا منجر بھ ھای متعدد در دھھ 1970
مورد استفاده قرار رزین ھای پلی استر اشباع شد کھ امروزه در ترکیبات مختلف رنگ ھای پودری تولید
.می گیرد
رزین ھایی با گروه فعال ھیدروکسیل بودند کھ با ھگزامتوکسی سامانھ ھای پلی استر در ابتدا بر پایھ
معایبی بود کھ شبکھ ای می شدند.اما آزاد کردن الکل بھ ھنگام پخت و پخت کند، از جملھ متیل ملامین
کربوکسیلیک بھ ھمراه تری گلیسیدیل مانع از انتخاب آن ھا گردید. در سال 1970 از رزین پلی استر
.شد ایزوسیانات بھ عنوان عامل پخت استفاده
کربوکسیلیک با رزین اپوکسی بیس یک نوآوری در سال 1971 منجر بھ ترکیب رزین ھای پلی استر
فنول A اپوکسی پلی استر شد. پیشرفت ھای بعدی بر پایھ رزین ھای برای تولید سامانھ ھیبرید یا پودر
.کاپرولاکتام بود ھیدروکسیلی پخت شونده با ایزوفورن دی ایزو سیانات بلوکھ شده با پلی استر
کربوکسیل برای پخت با عوامل پخت اکسازولین در ھمان زمان ، رزین ھای آکریلیکی با گروه فعال
بھ جز در بازار ژاپن، پودرھای آکریلیکی با موفقیت کمی ھمراه بودند، وارد بازار شدند. با این حال ،
.آغاز شده است در حال حاضر علاقھ بیشتری بھ استفاده از آن ھا بھ عنوان لایھ شفاف خودرو اگرچھ
در دھھ 1990 با توجھ بھ سمی بودن TGIC ھا در ساخت عوامل پخت جدید بوجود آمد ، برخی پیشرفت
شده بودند.سامانھ ھای پلی استری جدید کھ جنبھ تجارتی پیدا کردند، کھ نیازمند رزین ھای جدید یا اصلاح
لوریل و اکسیران آنھایی ھستند کھ عوامل پخت آن ھا بر پایھ ھیدروکسی الکیل آمید، گلیکول شامل
.آلیفاتیک می باشند
.مواد اولیھ پوشش ھای پودری
مواد اولیھ پوشش ھای پودری
:در ترکیبات پوشش ھای پودری رنگدانھ دار شش گروه مواد اولیھ وجود دارد
رزین پایھ کھ مھمترین آن ھا عبارتند از انواع اپوکسی ھای بیس فنول - 1 A نووالاک، پلی استرھای و
.گردند اشباع شده و آکریلیک ھا ، کھ بھ شکل جامد عرضھ می
:عوامل پخت کھ دارای خواص ذیل باشند - 2
.در دمای پخت با رزین خوب ترکیب شوند -
.در دمای محیط پایدار باشند - 3
.در دمای فرایند، بخصوص در طول فرایند اکستروژن تقریباً پایدار باشند -
.در حالت جامد بھ طور کامل قابل جاری شدن باشند -
.نقطھ ذوبی نزدیک بھ نقطھ ذوب رزین داشتھ و با آن امتزاج پذیر باشند -
.بھ عنوان یک ماده اولیھ در طول مدت اکستروژن یا پخت ، نبایستی مواد خطرناک یا فرار آزاد کنند -
رنگدانھ ھا- 4
عوامل جاری ساز- 5
سایر افزودنی ھا- 6
فیلر ھا- 7
با نام ھای پودری بھ طور مرسوم بر اساس نوع رزین و عامل پخت مصرفی بھ چندین گروه رنگ
آکریلیکتجاری اپوکسی، ھیبرید، پلی استر، پلی یورتان، ھیبرید آکریلیک، GMA و آکریلیک طبقھ بندی
.می گردند
پودرھای سخت شونده با پرتو UV
نظیر پلاستیک بودن دمای پخت در پوشش ھای پودری کاربرد آن ھا در روی مواد حساس بھ گرما بالا
سخت شونده با ھا، کامپوزیت ھای چوب و چوب طبیعی محدود می سازد. پوشش ھای UV این محدودیت
.را از بین می برند
شونده با در سامانھ ھای پخت UV دو نوع واکنش پخت آغازگر فتونی مطرح است:سامانھ ھای رادیکال
اترھا و یک اسید لوئیس آزاد و کاتیونی.برای سامانھ ھای کاتیونی، رزین ھای اپوکسی جامد و وینیل
استفاده می شود. در سامانھ رادیکال آزاد، پخت تولید شده بت فوتون جھت شروع واکنش شبکھ ای شدن
ھای پلی استر غیر اشباع یا مخلوط پلی استر با آکریلیتھا با رادیکال آزاد بر اساس پلیمرازیسیون رزین
برای شرایط مایع مناسب شده از تابش فوتون استوار است. از میان دو سامانھ فوق سامانھ رادیکال آزاد
.تر است
بعد از اعمال پوشش ، از آنجاییکھ پرتو UV نمی تواند گرما تولید کند بھ یک منبع گرمایی جھت ذوب
بھ چسبندگی آن بھ صورت یک لایھ مورد نیاز است، از این رو لامپ ھای مادون قرمز شدن پودر و
نقطھ ذوب موجب کاھش منظور افزایش دما استفاده می شوند. بالا بردن دمای پوشش دمای بالاتر از
گرانروی قبل از آغاز پخت توسط نور UV این حداکثر سیالیت و ھم سطحی اتفاق می می گردد. بنابر
.افتد
آغاز واکنش پخت تاثیر می گذارند کھ البتھ دلیل آن می تواند ناشی از جذب رنگدانھ ھا ، روی زمان
پرتوھای UV باشد. از این رو تا بھ امروز پوشش ھای پودری UV .رشد است بھ سرعت در حال
مزایا ی پوشش ھای پودری
:از میان مزایایی کھ پوشش ھای پودری دارند بھ اختصار می توان موارد زیر را نام برد
.سھولت استفاده: استفاده از پودر راحت تر از رنگ مایع بوده و نیاز بھ آموزش کارگر در آن کمتر است
ھای مایع مورد برای مصرف و کاربرد: ھیچ گونھ اختلاط، ھمزدن یا رقیق کردن بھ مانند رنگآماده
داخل بستھ مستقیماً مورد استفاده قرار نیاز نیست، تجھیزات کاربردی بھ راحتی می توانند پودر را از
.دھند
راحتی استفاده از پودر، ھم بھ شکل دستی و ھم بھ صورت خودکار، نمونھ :نمونھ ھای برگشتی کمتر
.غیر قابل قبول کمتری را نسبت بھ رنگ مایع می دھد ھای
.کاربرد تک لایھ: لایھ ای ضخیم با یکنواختی بھتر و تنھا با یکبار پاشش بھ دست می آید
سودمندی بالا: بازیافت پودرھای پاشیده شده اضافی بالای 95 % است، در حالیکھ برای رنگ ھای مایع
.کمتر از 15 % می باشد
.خطرات سلامتی: بھ علت عدم وجود حلال ھا یا مواد خطرناک فرار، خطرات سلامتی کاھش می یابد
.مواد غیر قابل بازیافت: رسوب یا تھ نشینی از رنگ پودری تولید نمی شود
تولید و نیز وجود حلال: حذف حلال در رنگ پودری منجر بھ کاھش آتش سوزی در سالن ھای عدم
جرقھ نیازی نیست. ھمچنان مشکلات مکان ھای کاربرد آنھا شده و بھ این خاطر بھ دستگاه ھای ضد
.زیست محیطی کمتری را بھ ھمراه دارند
نیازمندی جا و مکان: فضای کمتری جھت کاربرد مورد نیاز است
درباره وب
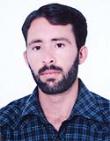
http://www.telegram.me/sajjadshafiee_ir . . . رشته مهندسی پلیمر نسبت به رشتههای مهندسی دیگر تقریبا جوان است و شکوفایی آن از زمان جنگ جهانی دوم آغاز شده است. اما به دلیل کاربرد روزافزون پلیمر در صنایع مختلف، این رشته به سرعت رشد کرده و امروزه جزو یکی از رشتههای مهم کشورهای صنعتی پیشرفته میباشد. هدف رشته مهندسی صنایع پلیمر تولید کلیه محصولات پلیمری از قبیل لاستیک، پلاستیک، الاستومر، چسبها، رزین و سایر مواد مورد نیاز صنعت است. برای مثال طراحی و تولید تایر ماشین در صنایع لاستیک، لولههای پلیاتیلن در صنایع پلاستیک و انواع فایبرگلاسها در کامپوزیت به یاری متخصصان مهندسی صنایع پلیمر انجام میگیرد یا حتی در این رشته شکلدهی رزینها نیز مطرح است که برای مثال میتوان به ساخت ملامین اشاره کرد.حتی کیسههای پلاستیکی و روکش ظروف نچسب ( تفلون ) از مواد پلیمری میباشند. در واقع در رشته مهندسی صنایع پلیمر هر آنچه که به این مواد بر میگردد، مورد مطالعه و بررسی قرار میگیرد. البته پلیمرها فقط کاربرد صنعتی ندارند بلکه کاربرد پزشکی نیز دارند. مثلا اگر کشکک زانوی یک نفر آسیب ببیند و ترمیم آن امکانپذیر نباشد، شبیه به همان کشکک زانو را با مواد پلیمری درست میکنند و بر روی زانو قرار میدهند و یا دندان مصنوعی و لنزهای چشمی همه از مواد پلیمری ساخته میشوند که به این مواد پلیمری «پلیمرهای زیستی» میگویند. فرصتهای شغلی: در صنعت پوشاک پلیمرها در تولید پاپوشها، تنپوشها و کفپوشها بسیار موثر هستند. در صنایع حمل و نقل زمینی (خودروسازی، قطار و ... )، هوایی ( هواپیما و بالگرد) و دریایی (کشتیها و ...) پلیمرها حضوری چشمگیر دارند، و بالاخره در صنایع نظامی، پزشکی، کشاورزی و بستهبندی کاربرد مواد پلیمری بسیار گسترده است.بدر صنعت پوشاک نیز پلیمرها در تولید پاپوشها، تنپوشها و کفپوشها بسیار موثر هستند. در صنایع حمل و نقل زمینی (خودروسازی، قطار و ... )، هوایی ( هواپیما و بالگرد) و دریایی (کشتیها و ...) پلیمرها حضوری چشمگیر دارند، و بالاخره در صنایع نظامی، پزشکی، کشاورزی و بستهبندی کاربرد مواد پلیمری بسیار گسترده است. باتوجه به کاربرد وسیع پلیمرها در صنایع، فارغالتحصیلان این رشته تواناییهای کافی در زمینههای ایجاد و برنامهریزی واحدهای تولیدی تبدیل پلیمر خام به مواد مصرفی و اشتغا
جستوجو
ویژه مدیریت وب
نویسندگان
لینک دوستان
برچسبها وب
مدیریت (23)
عکس (4)
مدیریت در اسلام (4)
اندروید (3)
فناوری نانو (2)
و (2)
یراق کابینت (1)
کائــوچو (1)
کائوچو طبیعی (1)
کاندیدای (1)
کوبه (1)
نوستالژی (1)
قفل حیاطی (1)
قفل لوکس (1)
قفل یونیک (1)
قفل کتابی (1)
قفل کمدی (1)
گالری یراق کوبه (1)
لاهیجان (1)
مجلس (1)
مدیر موفق (1)
مرد و زن (1)
مرودشت (1)
مزایای بیوپلیمر (1)
ملامین چیست (1)
مدیریت دانش (1)
انقلاب صنعتی (1)
ایام (1)
ایران (1)
اکسترودر (1)
پاسارگاد (1)
پلی اتیلن ، (1)
پلی پروپیلن (1)
پلی ونیل کلراید (1)
ارسنجان (1)
اسلامی (1)
اسلحه پلیمری (1)
امیرکبیر (1)
پی وی سی - PVC (1)
تاسوعا (1)
تسلیت (1)
تولدم مبارک (1)
جزوه الاستومر (1)
حسینی (1)
داستان (1)
داستانهای زیبا (1)
در (1)
دستگیره درب (1)
دهمین (1)
دوره (1)
سوپر جاذب (1)
شعر (1)
شهرستان های (1)
شورای (1)
عاشورا (1)
حامیان بلک اسکین
تاریخ : دوشنبه 89/6/29 | 10:11 عصر | نویسنده : مهندس سجاد شفیعی | نظرات ()