مترجم: حبیب الله علیخانی
مهندسی سطحی امروز
نواحی عمومی مربوط به فعالیت های مهندسی سطحدر طی 50 سال گذشته ، مهندسی سطح، متحمل توسعه های دینامیک گسترده ای شده است.
هر سال بیش از 50 کنفرانس علمی برگزار می شود که در مورد مهندسی سطح و زمینه های خاص مربوطه می باشد. هر ساله، چندین کتاب در مورد این موضوع، به چاپ می رسد که عمدتاً در مورد مباحث مطرح شده در این کنفرانس هاست. ژرنال های علمی و فنی کارهای خاص انجام شده در این زمینه را پوشش دهی می کند. تعداد مقاله های چاپ شده در این زمینه، هر ساله رو به افزایش است.
نشریات دوره ای در زمینه ی مهندسی سطح، منتشر شده اند. همچنین هندبوک ها، کتاب های مرجع و تک پژوهش های مختلفی در این زمینه منتشر شده است که در آن، مشکلات مختلف مربوط به مهندسی سطح، پوشش دهی شده است. سازمان های علمی مختلفی تأسیس شده اند که هدف از تأسیس آنها، بررسی جنبه های مختلف مهندسی سطح می باشد. مهندسی سطح به عنوان یکی از زمینه های علمی و فنی مطرح است.
در واقع، یک یکپارچگی، میان روش های شکل دهی و خواص خاص سطحی، وجود دارد. یک گسترش ملموس در تمام زمینه های مهندسی سطح ایجاد شده است که در واقع این مسئله در تشکیل، طراحی، بررسی و استفاده از لایه های سطحی، مشاهده می شود. پیشرفت بیشتر در زمینه ی روش های تولید لایه های سطحی، انجام شده است، در حالی که زمینه های مرتبط با این مسئله، در واقع آزمون هایی است که در مورد این موضوع می باشد. یک تعداد روز افزون از گزاراش ها در مورد استفاده از لایه های سطحی، انتشار یافته است. این گزارش ها بیشتر در مورد تحقیقاتی است که بر روی تربیولوژی و ماشین کاری می باشد.
تشکیل یا تولید لایه های سطحی
در زمینه ی روش های تولید، مهندسی سطح درگیر جایگزین نمودن لایه های سطحی است که معمولاً این جایگزینی در شکل ماده انجام می شود. در واقع در اینجا، یک کامپوزیت، تولید می شود. در این زمینه، مهندسی سطح، به عنوان هسته ی مرکزی تلقی می شود و برهکنش های انجام شده در این میان، هم فیزیکی و هم شیمیایی است. با در نظر گرفتن جنبه ی لایه های سطحی و پوشش ها، تمایزات زیر باید در نظر گرفته شود:• لایه های تکنولوژیکی
تولید این لایه ها به عنوان نتیجه ای از استفاده از روش های مختلف، می باشد. بسته به نوع اثرهای مورد استفاده در این زمینه، روش های تولید لایه های سطحی، ممکن است به 6 گروه، تقسیم شوند: روش های مکانیکی، روش های ترومو- مکانیکی، روش های الکتروشیمیایی، روش های فیزیکی و شیمیایی. در هر گروه، روش های مختلفی برای تولید لایه های سطحی با ضخامت و خواص متمایز، مورد استفاده قرار می گیرد.• لایه های تولید شده در حین سرویس دهی
این لایه ها، به عنوان نتیجه ای از استفاده از لایه های تکنولوژیکی در شرایطی، تولید می شوند که یا طبیعی یا مصنوعی است. شرایط خاص تولید این لایه ها، موجب می شود تا این لایه ها، خواصی داشته باشند که نسبت به لایه های اولیه و تکنولوژیکی، متفاوت باشند.دقیقاً همانگونه که خواص لایه های تکنولوژیکی بوسیله ی فرایند تولید، تحت تأثیر قرار می گیرد، این ممکن است که لایه های تولید شده در حین سرویس دهی و خواص آنها، تغییر کند.
تولید لایه های سطحی از لحاظ تاریخی، قدیمی ترین مورد گزارش شده در این زمینه است. این زمینه، یکی از زمینه های با رشد سریع در مورد مهندسی سطح است. حتی امروزه، این زمینه تا حدی به طور مستقیم یکی از زمینه های خاص مهندسی سطح، محسوب می شود.
• طراحی لایه های سطحی
این زمینه ی مهندسی سطح، در واقع در مورد طراحی لایه های سطحی است به نحوی که این لایه ها، می توانند الزامات مربوط به سرویس دهی را برطرف کنند. این زمینه از مهندسی سطح، کمتر توسعه یافته است. طراحی یک فرایند به گونه ای که موجب تولید یک ساختار و خاصیت غالب در لایه های سطحی شود، موجب می شود تا رابطه ی بین خواص تکنولوژیکی با خواص سرویس دهی قابل استفاده، و تصمیم گیری نهایی در مورد یک چنین تولیدی، تنها در برخی موارد استثنایی، قابل حصول باشد. در اغلب موارد، اگر چه این مورد به ندرت عملی می شود، مدل سازی ریاضی خواص لایه ی سطحی موجب می شود تا روش های فنی شناخته و عملی تر شوند.• بررسی لایه های سطحی
این زمینه از مهندسی سطحی درگیر تحقیق عملی بر روی ساختار و خواص لایه های سطحی، پارامترهای مختلف، ارتباط فنی این لایه ها با شرایط سرویس دهی و نیاز به دانستن اطلاعات در مورد اثرات مربوطه و اصول کاربردی، می باشد. نتایج این تحقیق با نتایج مربوط به فرایندهای تولید، ترکیب می شود و با توجه به این پارامترها و اطلاعات موجود در دیتابیس ها، لایه های سطحی کامپوزیت ها، طراحی می شود. انجام این تحقیق، نیازمند اجرای جدیدترین روش های بررسی، شامل بررسی های فیزیکی، شیمیایی، بیولوژیکی، خوردگی، استحکام و تریبولوژی است.• استفاده از لایه های سطحی در هنگام سرویس دهی
این ناحیه از مهندسی سطح، شامل دو گروه از مشکلات است:آزمون های سرویس دهی
آزمون های سرویس دهی رفتار لایه های سطحی در شرایط کاری مختلف، مورد استفاده قرار می گیرد. معمولاً این آزمون ها، تغییرات ایجاد شده در رفتار ماده در زمان سرویس دهی را پوشش دهی می کنند. به دلیل اینکه بررسی خواص لایه ها در طی سرویس دهی، با مشکلات متعددی روبروست، این لایه ها، معمولاً بعد از یک دوره ی زمانی خاص، و بعد از سرویس دهی، بررسی می شوند. این آزمون های بعد از سرویس دهی، با روش هایی انجام می شود که مشابه روش های مورد استفاده برای لایه های سطحی می باشد. تنها تفاوت این است که این روش ها، در طی سرویس دهی، اعمال می شود. بررسی ساختار و خواص مربوط به لایه های سطحی در طی سرویس دهی، نیازمند روش های فیزیکوشیمیایی خاص است که البته همه ی آنها به خوبی، توسعه نیافته اند.• لایه های تشکیل شده در حین سرویس دهی
تولید این لایه ها، در طی سرویس دهی قطعه در محل مورد نظر خود، رخ می دهد. علت این تشکیل، در واقع برهمکنش میان این مواد و مواد موجود در محیط می باشد.اهمیت مهندسی سطح
توسعه ی مهندسی سطح حالت پویا دارد. علت این مسئله در اصل به دلیل این حقیقت است که این زمینه از علوم و تکنولوژی، انتظارات علوم مدرن را برطرف می کند. این انتظارات، یکی افزایش بازده استفاده از ماده و انرژی و دوستدار محیط زیست بودن، می باشند. علاوه بر این حقیقت که این زمینه از تکنولوژی موجب می شود تا محققین با یک ماجراجویی علمی جالب، مواجه شوند، موجب می شود تا حقیقت های عملی جالبی را کشف کنند. هر فرد به طور روزانه با محصولاتی در تماس است که در آنها از مهندسی سطح استفاده شده است. در واقع همه ی ما باید از مهندسی سطح، تشکر کنیم. مهندسی سطح، موارد زیر را برای ما مهیا کرده است:• امکان تولید ابزارها، قطعات ماشین و وسایل از مواد با خواص پست تر و ارزان تر اصلاح سطح آنها با مهندسی سطح. این کار در برخی زمان ها، موجب کاهش وزن، و میزان انرژی مصرفی برای تولید آنها می شود. همچنین اعمال مهندسی سطح بر روی این قطعات، موجب بهبود خواص تریبولوژیکی، دکوراسیونی و سایر خواص این وسایل می شود.
• بهبود قابلیت اطمینان به ابزارها، اجزای ماشین و کاهش میزان خطاهای ایجاد شده در آنها. طراحی نامناسب و شرایط کاری نامطلوب، موجب می شود تا 15 % قطعات قبل از اتمام طول عمرشان، خراب شوند. در واقع انتخاب نامناسب و تولید ضعیف لایه های سطحی، در 85 % از موارد، موجب بروز این اشکال ها می شود.
• کاهش اتلاف های انرژی ایجاد شده به دلیل اصطکاک و بهبود خواص تریبولوژیکی سطوح مالشی. معمولاً 15 تا 25 % از برق مصرفی برای فایق آمدن بر اصطکاک مصرف می شود. این مورد در صنعت نساجی، تا 85 % نیز می رسد.
• کاهش در میزان جایگزینی ابزارها و قطعات معیوب و همچنین کاهش میزان ساعات خرابی دستگاه ها.
• کاهش 15 تا 35 % در اتلاف های ایجاد شده به دلیل خوردگی. این مورد در زمانی نمود دارد که بدانید اثر خوردگی بر روی اقتصاد، 5 % تولید ناخالص ملی است.
• کاهش در مصرف انرژی بوسیله ی صنایع. این مسئله به دلیل این حقیقت است که روش های مورد استفاده در مهندسی سطح، معمولاً روش های با مصرف انرژی پایین است. در واقع در روش های با مصرف انرژی بالاتر، مثلاً عملیات حرارتی، تنها بخش های انتخابی از نمونه، تحت عملیات حرارتی قرار می گیرد (بدون آنکه نیاز باشد تمام قطعه عملیات حرارتی شود). همچنین زمان استفاده از این روش ها، بسیار کوتاه است معمولا در حد چند ثانیه می باشد.
• به حداقل رساندن آلودگی های محیط زیستی در اصل به دلیل کاهش در میزان مصرف انرژی و همچنین امکان استفاده از روش های بازیافت برای قطعات فرسوده. گازهای حاصل از احتراق سوخت، حاوی گازهای گلخانه ای و مقادیری اکسید گوگرد و نیتروژن، هیدوکربن های فرار و مواد مخرب دیگر می باشد.
جهت دهی در زمینه ی مهندسی سطح
در زمان های آینده، مهندسی سطح به سرعت رشد خواهد کرد. مهندسی سطح از جمله علومی است که بر پایه ی علوم و کشفیات روز دنیا، گسترش می یابد. این انتظار وجود دارد که این علم، به عنوان یکی از علوم پیشگام در آینده باشد.به کمال رسیدن و ترکیب شدن روش های تولید لایه های سطحی
توسعه ی روش های تولید لایه های سطحی، به طور قابل توجهی، به روش های مورد استفاده و اهمیت توسعه ی تکنولوژی وابسته است. در واقع مزیت های حاصله از این روش ها، یک موضوع مهم در این توسعه می باشد.
رویه های عمومی مربوط به توسعه ی روش های تولید لایه های سطحی، ممکن است به صورت زیر خلاصه شود:
1) استفاده از اثر هم افزایی با کاربرد:
• روش هایی که اجازه ی توسعه ی لایه های ساندویچی را فراهم می آورد. این لایه ها با روش های مشابه با روش های تولید لایه های معمولی تولید می شوند، تنها تفاوت اندکی در زیرلایه، وجود دارد.
• روش های دوتایی، سه تایی و چند تایی به منظور بدست آوردن لایه های سطحی با خواص کاربردی مطلوب و عمر مفید بالا (مثلا استفاده از پوشش های فلزی- رنگی با طول عمر 25 الی 40 سال، بدون نیاز به نوسازی در مکان هایی که طول عمر پوشش های رنگی، تنها چند سال است. این پوشش ها با روش اسپری گرمایی و رنگ آمیزی با روش پنیوماتیک یا الکترواستاتیک، اعمال می شوند. مثال دیگر، استفاده از نیتریداسیون پیش از سخت کاری زیرلایه و سپس رسوب دهی پوشش های تیتانیم نیترید. مثال دیگر، ترکیب پرداخت سطوح سخت کاری شده با روش های حرارتی و ترموشیمیایی. از جمله موارد دیگر می توان به ترکیب نیتریداسیون و بمباران با یون نیتروژن و یا یون های بور می باشد.
2) کاهش در مصرف انرژی در روش های تولید لایه های سطحی و حذف روش های با مصرف انرژی بالا. مثلا بازگردانی و استفاده ی مجدد از حرارت ایجاد شده در اتاق های رنگ کاری پوشش های آلی؛ استفاده از روش های جدید حرارت دهی الکتریکی آلومینیوم، آلیاژها و سایر حمام های نفوذی، حذف حمام نمک و جایگزینی آن با بسترهای سیال، اتمسفر و خلأ. استفاده از روش های با انرژی بالا مانند لیزر، پلاسما و باریکه ی الکترونی. استفاده از روش های مختلف پرداخت و جایگزینی آنها با عملیات های ترموشیمیایی.
3) کاهش در میزان مصرف مواد اولیه ی مورد استفاده در تولید لایه های سطحی؛ مثلاً جایگزینی اسپری های پنیوماتیک رنگ آمیزی با رسوب دهی الکترواستاتیک رنگ های مایع یا پودری و یا استفاده از روش های نفوذی تخلیه ی درخشان به جای استفاده از حمام نمک و عملیات های گازی.
4) افزایش دقت آماده سازی زیرلایه برای افزایش پذیرش پوشش. در نظر گرفتن فعالیت شیمیایی و استفاده از روش های تمیزکاری و شستشو مانند روش التراسونیک و رسوب دهی لایه های واسط.
5) استفاده از تکنولوژی های دوستار محیط زیست و اقتصادی. این کار موجب کاهش میزان تولید آلودکی و اثرات نامطلوب بر روی محیط زیست می شود. این کار موجب کاهش میزان انتشار گازهای گلخانه ای و گازهای مضر برای لایه ی ازون و گازهای ایجاد کننده ی باران های اسیدی، می شود. این مسئله در رویه ی جایگزینی رنگ های پودری با رنگ های مایع و همچنین استفاده از حلال های آبی به جای استفاده از حلال های آلی، نمود دارد. یکی دیگر از این کارها، استفاده از پوشش های ضد خوردگی است که در فرایند خشک شدن، به طور خود به خود، لایه ای می شوند و به صورت یک لایه ی سطحی و یک لایه ی پرایمر، تشکیل می شوند. حذف فرئون که زمانی به عنوان محیط شستشو مورد استفاده قرار می گرفت، حذف حمام های نمک مورد استفاده برای سخت کاری و جایگزینی آن با مواد پلیمری، از جمله مواردی هستند که برای محافظت از محیط زیست، انجام شده است.
6) تمرکز بر روی روش های تولید لایه ی سطحی برای استفاده در بخش های خاص صنعتی مانند فولاد سازی، به منظور حذف حمل و نقل غیر ضروری و استفاده از حرارت های اضافی ایجاد شده در طی این فرایندها، می باشد. در کشورهای اروپایی، 5 تا 15 % از فولاد نورد سرد شده، میله های پروفیل، میله های با سطح مقطع مدور و سیم ها، بوسیله ی پوشش های ایجاد شده با روش اسپری حرارتی، روش الکترولیتی، و سایر روش ها، پوشش دهی می شوند. در اکثر کشورهای اروپای شرقی و مرکزی، خطوط پوشش کاری پیوسته ی مربوط به فولاد سازی، تنها در برخی از بخش ها، مشاهده می شود. البته روش های تولید پوشش بر روی این صفحات نیز گاهی اوقات، هزینه بر هستند و موجب آلودگی محیط زیستی می شود.
7) مکانیزه کردن و اتوماتیک کردن و حتی استفاده از روبات در تولید لایه های سطحی، مخصوصاً در روش های اسپری حرارتی و اسپری با حلال های آلی. این مسئله به دلیل ایجاد آسیب هایی است که این مواد به سلامت اپراتور، وارد می کنند.
8) رشد استفاده از میکروپردازنده ها و کنترلرهای کامپیوترهای نه تنها در سیستم های منفرد، بلکه در کل بخش های خط تولید. در آینده، می توان انتظار داشت که کل بخش تولید، بواسطه ی کامپیوتر، کنترل شود.
9) افزایش استفاده از روش های بازیافت (هم استفاده از مواد ضایعاتی و هم بازگشت مواد زائد خط تولید به داخل چرخه ی تولید). مثلاً استفاده از رسوبات زائد در فرایند آبکاری و رنگ کاری
آزمون های میکرومتری و نانومتری
آزمون های انجام شده بر روی لایه ها، شامل تعیین خواص فیزیکی و شیمیایی مختلف و همچنین استفاده از روش های بررسی است که در مهندسی و علم مواد، مرسوم است. این پیش بینی می شود که برخی از روش ها، به صورت ترکیبی برای بررسی خواص استفاده شوند. این مسئله شامل موارد زیر است:• استفاده ی ترکیبی از آن دسته از روش هایی که معمولاً در بررسی های تریبولوژیکی، بررسی های مربوط به استحکام ماده و بررسی های مربوط به حفاظت در برابر خوردگی، استفاده می شوند.
• روش های نانومتری ظریف برای بررسی ساختارهای لایه ای و اتمی و بررسی پدیده های فیزیکی در مقیاس میکرمتری، استفاده می شوند.
کاربرد منطقی لایه های سطحی
کاربردهای منطقی مربوط به لایه های سطحی، نیازمند داشتن اطلاعات مناسب در زمینه ی ویژگی های آنهاست. در واقع هم ویژگی های بالقوه و هم ویژگی های آنها در حین سرویس دهی. وظایف اصلی، عبارتند از:• کاهش در مصرف انرژی و ماده در حین استفاده از قطعات و وسایل، تحت شرایط تریبولوژیکی، خستگی و خوردگی نامناسب. این مسئله بر این دلالت دارد که کاربرد این لایه های سطحی و استفاده از آنها تحت این شرایط، موجب مینیمم شدن نرخ مصرف انرژی و اتلاف های مربوط به خوردگی می شود. در اینجا، ترجیح استفاده از سطوح با سایش مینیمم است.
• آنالیز تشخیصی حالت لایه های سطحی مورد استفاده برای قطعات کار کرده به نحوی که راهی برای جمع آوری اطلاعات مربوط به این لایه ها، فراهم آید.
• انتخاب لایه های سطح برای شرایط سرویس دهی خاص مانند بخش های متحرک که متحمل سایش سطحی می شوند.
منبع:راسخون
از دست رفت ارتفاع در پمپهای گریزازمرکز
در تحلیلهائی که در قسمت قبل برروی عملکرد پمپهای گریز ازمرکز انجام شد، پمپ گریز از مرکز یک ماشین ایده ال فرض گردیده و از دست رفت انرژی (ارتفاع) در آن ناچیز در نظر گرفته شد.
ولی درپمپهای واقعی همواره مقداری از انرژی (ارتفاع) در داخل آن بشکلهای مختلف بهدر رفته و موجب میشود تا منحنی مشخصه H-Q واقعی پمپ درزیرمنحنی مشخصه تئوریک پمپ گریزازمرکزدرشرایط ایده ال قرار گیرد.
شناخت عوامل مؤثر در از دست رفت ارتفاع در پمپ، ضمن اینکه میتواند در شناخت منحنی مشخصه واقعی آن کمک کند، بلکه در زمینه اعمال اصلاحات لازم در طراحی و ساخت پمپ و کاهش از دست رفت ارتفاع و افزایش راندمان آن نیز مفید واقع شود. بطوری که امروزه راندمان پمپهای گریزازمرکزبه پیش از 90 درصد نیز رسانیده شدهاست. عمدهترین عوامل ازدست رفت ارتفاع در پمپهای گریزازمرکز عبارتند از:
از دست اتلاف ناشی از اصطکاک
همانطوری می دانیم، ازدست رفت ناشی از اصطکاک در اثر عبور مایع از درون مجاری (پوسته پمپ) تابعی از دبی بوده که با رابطه ی زیر نشان داده شدهاست:
که در آن n به نوع جریان بستگی داشته (غالباً n=2 در نظر گرفته میشود) و K تابعی از طول مسیر مایع در پمپ، شعاع هیدرولیکی (نسبت سطح مقطع جریان مایع به محیطتر شده توسط آن)، سطح مقطعهای جریان مایع در پمپ و نسبت آنها و ضریب اصطکاک (و عوامل مؤثر برروی آن نظیر زبری سطح، ویسکوزیته مایع و...) بستگی دارد.
ازدست رفت ناشی از جریان گردابی
پروانه عبارتاست از تعدادی تیغه که بصورت منحنی در آمده تا جریان مایع در پمپ آرام و بدرون اغتشاش صورت پذیرد. با افزایش تعداد تیغهها، هدایت جریان مایع در پمپ بنحو مطلوبتری صورت پذیرفته، در صورتی که با کاهش آن، از دست رفت انرژی در اثر جریان گردابی و گردشی در پروانه افزایش مییابد. همانطوری که بعداً به آن اشاره خواهد شد، زاویه لبه تیغه پروانه تأثیر بسزائی برروی عملکرد پمپ های گریزازمرکز میگذارد.
درهنگام طراحی پروانه و تعیین زاویههای ورودی و خروجی تیغههای آن، دبی معینی بنام “دبی طراحی”در نظر گرفته شده وبدنبال آن مشخصههای ابعادی پروانه محاسبه ودرساخت آن مورداستفاده قرار میگیرد. بدیهیاست که اگر دبی واقعی پمپ با دبی طراحی مغایرت داشته باشد، پمپ نمیتواند رفتاری مشابه با شرایط طراحی داشته باشد، که عوارض آن بصورت مختلف و ازجمله بهم خوردن زاویه بردار سرعت نسبی در قسمتهای ورودی وخروجی پروانه یا بعبارت دیگر بروز پدیده جریان گردابی خود را نشان میدهد. همانطوری که در شکل 1 مشاهده میشود میزان جریان گردشی در دو سمت BEP غیر قابل چشم پوشی بوده ولی در BEP به صفر میرسد. اساساًهرگونه انحراف در زوایای ورودی و خروجی مایع در پروانه در مقایسه با زوایای
یا بعبارت دیگر تغییر بردار سرعت نسبی مایع به پروانه میتواند موجب بروز جریان گردابی شده که اصطلاحاً اتلاف شوکی نیز نامیده میشود.
جریان گردشی
اولر در تحلیل عملکرد پمپهای گریزازمرکز، فرض نمود که تعداد تیغههای پروانه بینهایت باشد. اجرای فرضیه فوق در عمل غیر ممکن بوده و تعداد تیغههای پروانه بین 3 تا 10 (عموماً 5 تا 7)میباشد. کاهش تعداد تیغههای پروانه باعث میشود تا زاویه واقعی بردار سرعت مایع خروجی از پروانه β_2^" نتواند با مقدار فرض شده β_2 یکسان گردد. مغایرت فوق باعث میشود تا مثلث سرعت در لبه خروجی پروانه تغییر کرده (شکل 2) و مقداری مایع قبل ازخروج ازپروانه مجدداً به قسمت مکش آن برگشت مییابد(شکل 3).
پدیده فوق میتواند باعث کاهش بردار سرعت خروجی از پروانه و نهایتاً کاهش ارتفاع قابل دسترس در پمپهای واقعی در مقایسه با پمپهای ایده ال گردد.
بدیهیاست در دبیهای کم بعلت بالا رفتن اختلاف فشار بین قسمتهای مکش و دهش و وجود لقی بین پروانه و پوسته پمپ، میزان جریان گردشی در مقایسه با مواردی که دبی پمپ بیشتراست، زیادتر میباشد.
نقطه بهترین راندمان
همانطوری که مشاهده شد، در یک نقطه معینی از دبی بهره برداری از پمپ، اختلاف فاصله بین دو منحنی واقعی و ایده ال که همان از دست رفت ارتفاع در پمپ میباشد به حداقل خود رسیده یا بعبارت دیگر راندمان پمپ در این نقطه به حداکثر مقدارخود میرسد. این نقطه را نقطه بهترین راندمان یا باختصار BEP مینامند. بنابر یکی از اصول اساسی علوم مهندسی هرماشین هنگامیدارای حداکثر راندماناست که در شرایط طراحی خود بکارگرفته شود. بنابراین BEP را میتوان همان نقطه طراحی پمپ دانست. هرچند که بلحاظ ویژگیهای خاص جریان گردشی و اصطکاک، مقادیر ازدست رفتهای ارتفاع مربوط به هریک ازعوامل فوق در BEP حداقل نمیباشد ، ولی بلحاظ کاهش شدید از دست رفت ارتفاع ناشی از پدیده جریان گردابی، کل ازدست رفت ارتفاع در پمپ در BEP به حداقل رسیده و به همین خاطر مغایرت ارتفاع تئوریک و واقعی کمترین مقدار خود را نشان میدهد.
راندمان پمپ
فرض میشودکه ازکل دبی پمپ
، مقداری ازآن (Q_l ) بلحاظ وجود لقی بین لبه نافی چشمه پروانه و پوسته پمپ از قسمت فشار قوی به قسمت فشار ضعیف (چشمه پروانه) برگشت نماید. در این صورت دبی واقعی پمپ
برابراست با:
بنا بر تعریف راندمان حجمیپمپ برابراست با نسبت دبی واقعی به دبی کل:
همانطوری که قبلاً گفته شد به لحاظ وجود مغایرتهائی بین شرایط بهره برداری و شرایط طراحی وحتی بصورت دقیقتر مغایرت با پیش فرضهای اولر، ارتفاع واقعی پمپ
ازارتفاع تئوریک
آن کمتر بوده که نسبت آنهارا راندمان هیدرولیکی پمپ مینامند:
راندمان مکانیکی پمپ برابراست با:
که در آن FHP از دست رفت انرژی ناشی از اصطکاک در یاطاقانها، سیستم آب بندی کننده و اصطکاک دیسکی می باشد.
راندمان کلی پمپ عبارتاست از نسبت توان داده شده به مایع مورد پمپاژ (WHP) به توان داده شده به شافت پمپ (BHP) که برابراست با حاصلضرب راندمانهای حجمی، هیدرولیکی و مکانیکی.
کاویتاسیون
فشار بخار
بنا بر تعریف دمائی که مایع به گاز (و بالعکس) تبدیل میشود را دمای اشباع مینامند. دمای اشباع هر مایع به فشار آن بستگی دارد. مثلاً آب در فشار یک اتمسفر (0133/1 بار) در دمای 100 درجه سانتیگراد بجوش میآید. تعریف فوق را میتوان به صورت دو گزاره زیر بیان کرد:
الف: دمای اشباع آب در فشار 0133/1 بار، 100 درجه سانتیگراداست.
ب: فشار بخار آب در دمای 100 درجه سانتیگراد 0133/1 بار میباشد .
همانطوری که از جدول 1 پیداست دمای اشباع آب با کاهش فشار کاهش مییابد (و بالعکس) ویا فشار بخار آب با کاهش درجه حرارت کاهش مییابد (و بالعکس). فشار بخار جزء خواص فیزیکی هر سیال میباشد. پدیده کاویتاسیون در پمپها هنگامیبوقوع میپیوندد که فشار مایع در قبل از چشمه پروانه، (وحتی در مواردی در داخل پروانه) از فشار بخار آن در دمای پمپاژ کمتر گردد (شکل 4).
در شکل 4a، حداقل فشار در چشمه پروانه و بخش ابتدائی تیغهها در حدیاست که از فشار بخار مایع در دمای انتقال بالاتر بوده و لذا پمپ فارغ از بروز پدیده کاویتاسیون بکار خود ادامه میدهد. ولی در شکل 4b در مناطقی از قسمت مکش و یا چشمه پروانه و حتی در قسمتهای ابتدائی تیغههای پروانه، فشار مایع میتواند آنقدر کاهش یابد که از فشار بخار آن در دمای پمپاژ کمتر گردیده و همین امر میتواند موجب بروز پدیده کاویتاسیون شود. بنابراین میتوان نتیجه گرفت که بروز پدیده کاویتاسیون در انتقال هرمایع در درجه نخست به دمای مایع مورد پمپاژ و میزان فشار در مسیر جریان مایع از قسمت مکش تا داخل پروانه بستگی دارد. ولی درکنار آن عوامل دیگری نظیر مشخصههای رفتاری پمپ(پروانه) نیز در بروز این پدیده مؤثر بوده که بطور جامع در قسمتهای بعد بدان اشاره خواهد شد.
خالص ارتفاع مثبت در قسمت مکش NPSH
پدیده کاویتاسیون در پمپهای گریزازمرکز هنگامیبوقوع میپیوندد که خالص ارتفاع مثبت در قسمت مکش پمپ از آنچه که شرکت سازنده پمپ توصیه نمودهاست کمتر شده باشد. بنا براین برای تحلیل شرایط بروز این پدیده در پمپهای گریزازمرکز لازماست که هم شرایط قسمت مکش پمپ از نظر فشار (ارتفاع) و هم مشخصههای پمپ مورداستفاده از نظر وجود حداقل شرایط مورد نیاز جهت ممانعت از بروز این پدیده مورد بررسی قرار گیرد.
جهت سهولت در تحلیل فوق NPSH به دو دسته تقسیم میشود:
خالص ارتفاع مثبت قابل دسترس در قسمت مکش پمپ (NPSHA)
خالص ارتفاع مثبت مورد نیاز در قسمت مکش پمپ (NPSHR)
NPSHA جزء مشخصههای سیستم پمپاژ بوده و به عوامل متعددی نظیر فشار جو، خواص فیزیکی مایع مورد پمپاژ (درجه حرارت، وزن مخصوص، فشار بخار در دمای انتقال، ویسکوزیته و... .)، اختلاف سطح انرژی پتانسیل (فشار یا ارتفاع) در منبع مکش تا دهانه چشمه پروانه، تعداد و نوع اتصالات مورداستفاده در قسمت مکش، طول و قطر لوله مکش، دبی جریان و... بسنگی دارد. بنابراین تعیین آن بعهده طراحان سیستم پمپاژمیباشد.
NPSHR به مشخصههای رفتاری و طراحی، دبی جریان، سرعت دورانی و... پمپ بستگی داشته که از سوی شرکت سازنده پمپ و بصورت یک دسته منحنی سهمیگونه صعودی برای قطرهای مختلف پروانههای مورداستفاده در پمپ بر حسب تغییرات دبی پمپ تهیه شده و در اختیار مشتریان قرار داده میشود (شکل 5) . وجه مشترک NPSHR با NPSHA وابستگی هر دو آنها به دبی جریان مایع میباشد. با این تفاوت، در حالی که NPSHR با افزایش دبی افزایش مییابد، NPSHA با افزایش دبی کاهش یافته و همین مغایرت رفتاری باعث میشود که بتوان اذهان داشت که یکی از عوامل اصلی بروز کاویتاسیون در پمپهای گریزازمرکز بالا بودن دبی جریان میباشد.
بررسی وضعیت شروع پدیده کاویتاسیون در پمپها
تا زمانی که NPSHA در حدی باشد که پمپ را از بروز پدیده کاویتاسیون مصون نگهدارد، مقدار آن نمیتواند بر عملکرد هیدرولیکی پمپ تأثیر بگذارد، یا بعبارت دیگر ارتفاع قابل دسترس توسط پمپ مقداری ثابت و مستقل از NPSHA خواهد بود (شکل 6).با کاهش NPSHA ارتفاع کل پمپ در دبی ثابت تغییری نخواهد کرد ولی در نقطه ای مانند NPSHi، اولین حبابهای بخار در پروانه پمپ تشکیل میشود که اصطلاحاً آن کاویتاسیون مقدماتی یا ابتدائی مینامند. با وجود تشکیل حباب، منحنی مشخصه پمپ و ارتفاع اعمال شده توسط آن تغییر نمیکند. با استمرار کاهش NPSHA، در وضعیت خاصی بلحاظ افزایش میزان حبابهای تشکیل شده، شرایطی بوجود میآید که ارتفاع کل پمپ شروع به کاهش مینماید.
علائم بروز کاویتاسیون در پمپهای گریزازمرکز
پدیده کاویتاسیون همانند هر عارضه دیگری دارای نشانهها و علائمیبوده که بکمک آن میتوان بروز پدیده کاویتاسیون در پمپ را شناسائی کرده و سپس براساس دستورالعملهائی که در ادامه این بخش ارائه خواهد شد، تصمیم مناسب جهت غلبه بر آن اتخاذ نمود.همانطوری که قبلاً گفته شد، شروع کاویتاسیون در پمپ هنگامیاست که در اثر کاهش NPSHA، ارتفاع پمپ به میزان 3 درصد کاهش یابد. اما واقعیت امردرایناست کهاستناد به تعریف فوق برای شناخت بروز پدیده کاویتاسیون درپمپها کافی نبوده وگاهی اوقات غیرقابل تشخیص میباشد، به نحوی که غالباً، هنگامیاپراتورها ویا تعمیرکاران به وقوع این پدیده نامطلوب در پمپها پی میبرند که پمپ دچارخسارات جبران ناپذیری گردیدهاست. بنابراین لازماست کلیه افرادی که بنحوی باپمپها سروکاردارند، به علائم مشخصه بروزکاویتاسیون درپمپها آشناشده تابه محض مشاهده آنها باانجام یک سری عملیات اصلاحی، مانع ازپیشرفت کاویتاسیون درپمپهاوبروزصدمات شدیددرساختارمکانیکی آن گردند. مهمترین علائم مشخصه بروز کاویتاسیون درپمپهای گریزازمرکزعبارتند از تشکیل حباب در پروانه و پوسته، ایجاد سروصدا، افزایش لرزش، کاهش ارتفاع و دبی و راندمان پمپ، کاهش فشار دهش، لرزش در فشار سنجهای مکش و دهش، خرابی زودرس یاطاقانها، آسیب دیدگی قطعات داخلی پمپ و... .
تشکیل حباب
همانطوری که قبلاً اشاره شده، بروز پدیده کاویتاسیون با تشکیل حبابهای بخار شروع میشود. برای این منظور میتوان از تجهیزاتی که قادر به نشان دادن شرایط داخلی پمپ نظیرEndoscope میباشد، استفاده کرد.سروصدا
تشکیل حباب وترکش آنها در اثر پدیده کاویتاسیون همواره با بروز سروصدای غیر عادی (صدائی نظیر عبور ماسه از درون پوسته پمپ) توأم خواهد بود.در شناخت کاویتاسیون اندازه گیری مقدار سروصدا (میزان مطلق آن) لازم نبوده و بلکه تغییر سطح (Level) آن باید معیار تشخیص قرار گیرد. این روش اجازه میدهد تا براساس آن بتوان سیستمهای هشداردهنده را براساس سطح فشار صوتی ناشی از کاویتاسیون برای تشخیص وضعیت هشدار، توقف و یا کنترل پیش بینی کرده و از آن جهت کنترل شرایط یهره برداریاستفاده نمود.
لرزش
لرزشی که در زمان بروز کاویتاسیون در پمپ پدید میآید ناشی از سه پدیده زیر میباشد:بعلت وجود تفاوتهای اجتناب ناپذیردر تیغهها، دنباله کاویتاسیون در تمامیتیغهها یکسان نمیباشد، در نتیجه جریان مایع در اطراف تیغهها در حال تغییر بوده و همین امر باعث نابالانسی در پروانه گردیده که لرزش پمپ را بدنبال خواهد داشت.
دنباله کاویتاسیون دائماً در حال تغییر بوده و همین امر باعث بروز کاویتاسیون با فرکانس زیاد و در حال تغییر خواهد شد.
اگر گسترش دنباله کاویتاسیون درحدی باشدکه جریان مایع بطور چشم گیری پخش شود(کاهش ارتفاع)، جریان مایع خروجی از پروانه یکنواخت نبوده و میتواند باعث بروز پدیده جدا شدن در قسمت پائین دستی مجرای هر تیغه گردد. هرچه جریان مایع در اثر کاویتاسیون در پروانه بیشتر پخش شود، مایعی که به گلوئی پوسته پمپ میرسد دارای نوسان بیشتری خواهد بود. فرکانس لرزش در این حالت برابراست با فرکانس دوران ضربدر تعداد تیغههای پروانه. در اینجا ذکر این نکته ضروریاست که بروز کاویتاسیون ابتداء با تشکیل مقادیر جزئی حباب شروع گردیده و در این مرحله فقط قسمتی از پروانه توسط حباب پر خواهد شد که اصطلاحاً آنرا ُ ُکاویتاسیون جزئی ُ ُ مینامند. بعد از گسترش کاویتاسیون، پروانه از حبابهای گاز پر شده و کاویتاسیون حالت کلی را بخود میگیرد. در حالت کاویتاسیون جزئی هرچند که لرزش ناشی ازترکش حبابها در مقایسه با کاویتاسیون کلی کمتر میباشد ولی بخاطر غیر یکنواختی توزیع سیالات (مایع و بخار) در آن، لرزش ناشی از نابالانسی در پروانه زیادتر از کاویتاسیون کلی خواهد بود. به همین خاطر در تحلیل فرآیند کاویتاسیون کاهش لرزش را نباید یک عامل بهبود شرایط عملکرد سیستم (رفع کاویتاسیون) تلقی کرد، بلکه خود میتواند تأئیدی بر پیشرفت و گسترش کاویتاسیون در پمپ باشد.
کاهش ارتفاع قابل دسترس، دبی و راندمان پمپ
در مواردی که NPSHA درحدی باشد که پمپ دچار کاویتاسیون نگردد، نقطه کار پمپ، محل تلاقی منحنی مشخصه سیستم با منحنی مشخصه پمپ خواهد بود. عدم بروز کاویتاسیون باعث ثبات منحنی مشخصه پمپ گردیده و لذا ارتفاع قابل دسترس، دبی وراندمان پمپ مقادیر قابل قبول را خواهند داشت. ولی در شرایط بروز کاویتاسیون، منحنی مشخصه پمپ دچار تغییرات نامطلوبی گشته و قادر به اعمال ارتفاع همانند شرایط عادی نخواهد بود و همین امر باعث کاهش ارتفاع قابل دسترس، دبی و راندمان پمپ خواهد شد (شکل 7).همانطوری که در شکل 8 مشاهده میشود بروز کاویتاسیون در پمپ باعث انتقال محل تلاقی منحنی مشخصه پمپ با منحنی مشخصه سیستم بسمت چپ (دبی کمتر) شده و نقطه کار دارای ارتفاع، دبی و راندمان کمتری در مقایسه با حالتی که NPSHA در حد کافی میباشد، میگردد.
هر چندکه در منابع علمیاشاره چندانی به تأثیر کاویتاسیون برروی توان مصرفی در پمپ تحت شرایط بروز کاویتاسیون نگردیده ولی با بررسی روابط قبل شاید بتوان نتیجه گرفت که با توجه به کاهش همزمان دو پارامتر Q وH در صورت و کاهش راندمان در مخرج کسر نباید انتظار افزایش توان مصرفی را داشته و احتمال کاهش توان مصرفی بیشتری میباشد. ولی در هر حال اظهار نظر قطعی در این زمینه نیازمند تعیین مقادیر Q ، H وη بوده تا براساس آن بتوان نظر قطعی را در زمینه تأثیر کاویتاسیون برروی توان مصرفی در پمپ اعلام کرد.
کاهش فشار دهش
با توجه به رابطه زیر میتوان نتیجه گرفت:
بروز پدیده کاویتاسیون ضمن کاهش ارتفاع قابل دسترس، باعث تشکیل حبابهای بخار گردیده که دارای وزن مخصوص کمتری نسبت به فاز مایع میباشند.
نوسان شدید عقربه فشار سنجهای مکش و دهش
درمواردی که پمپ دچارپدیده کاویتاسیون میگردد، فاقد رفتار یکنواخت وپایدارخواهد شد. یکی ازمهمترین ناهماهگنی رفتاری آن نوسان شدید درفشار مکش و دهش بوده که بصورت نوسان شدید در عقربههای فشارسنجهای مکش ودهش میتوان آنرامشاهده کرد.خرابی زودرس یاطاقانها
پمپهای گریزازمرکز غالباً دارای دونوع یاطاقان میباشند که یکی از آنها برای بار شعاعی بوده ودیگری برای تحمل بار محوری میباشد. بروز پدیده کاویتاسیون درپمپها موجب تغییرات شدید بارهای وارده بریاطاقانها گردیده وهمین تغییرات شدید بار وارده، موجب تغییرات شدید در بردار نیروهای وارده بریاطاقان ها خواهد شد که نهایتا باعث کاهش عمر مفید و خرابی زودرس یاطاقان ها می شود.بروز صدمات وخرابی درپروانه وپوسته یک پمپ
تشکیل حباب در هنگام بروز پدیده کاویتاسیون درداخل پروانه پمپ غالباً درقسمت فشارضعیف تیغه پروانه صورت پذیرفته وبدیهیاست هنگامیکه این حبابها به مناطقی بافشار زیادمیرسند، وارد شدن فشاربراین حبابها موجب ترکیدن آنها خواهد شد.ترکیدن حبابها همواره باآزادشدن مقدارزیادی انرژی توأم بوده که همان انرژی نهان تبخیر مایع میباشد که در زمان تبخیر، به مایع داده شدهاست. انرژی آزادشده، بر روی سطوحی که حباب ها برروی آن میترکندنیرو واردکرده ومیتواندباعث کنده شدن ذرات فلز از بدنه پروانه وپوسته گردد. کنده شدن فلز از بدنه پروانه را اصطلاحاً جوش زدن مینامند (شکل 9).آثار تخریبی کاویتاسیون نه در محل تشکیل حبابها و بلکه در نواحی با فشار بالا که در اثر افزایش فشار، حبابها میترکند بوقوع میپیوندد. اگرترکش حبابها در حین جریان مایع بوقوع بپیونددآسیبی به پمپ وارد نمیشود ولی در نزدیکی دیواره قطعات و در اثر پدیده ضربه جت (Jet Impact)، در ابتدای امر فقط سطح قطعه آسیب دیده ولی بمرور زمان در عمق آن نفوذ خواهد کرد. در شکل 10 نقاطی که میتوانند در معرض آسیب دیدگی ناشی از کاویتاسیون قرار گیرند با پیکان نشان داده شدهاست که شامل تیغههای پروانه اندکی دورتر از لبه هدایت کننده و در قسمت پشتی آن، نقاطی که لقی متحرک وجود دارد، قسمت ورودی پروانه جائی که تغییر ناگهانی مسیر جریان بروزمیکند و در تیغههای هدایت کننده بعدی بوقوع میپیوندد.
لازم به ذکراست که در زمان تعمیرات پمپها غالباً مسئولین تعمیرات با خرابیهایی برروی پروانه وپوسته پمپ مواجه میشوند که درابتدای امر به نظرمیرسد ناشی ازبروزپدیده کاویتاسیون میباشد. حا ل آنکه خرابیهای موجودممکناست ناشی ازپدیده خوردگی و یا سایش و یا مجموعه از دو یا سه پدیده فوق باشد. شناخت علت خرابی پروانه و پوسته پمپ و یافتن راه حل مناسب برای برطرف کردن و یا جلوگیری از آن اهمیت بسزائی دارد که در قسمتهای بعدی همین بخش مورد بررسی قرار خواهد گرفت.
روش های غلبه بر کاویتاسیون
پدیده کاویتاسیون هنگامیدر پمپهای گریزازمرکز بوقوع میپیوندد که شرایط قسمت مکش (فشار مایع) در حد مطلوب نبوده، بنحوی که مایع قبل از ورود بداخل پروانه (و درمواردی حتی درقسمتهای ابتدائی پروانه) به بخار تبدیل نشود. لذا جهت جلوگیری از بروز این پدیده لازماست که شرایط مایع در دهانه ورودی پمپ در حدی باشد که مایع مورد انتقال در طول عبور از مسیر مکش تا قسمت خروجی پروانه بصورت بخار تبدیل نشود. برای این منظور از نظر تئوریک کافیاست که NPSHA از NPSHR پمپ در دبی بهره برداری بیشتر باشد. اکثر سازندگان پمپهای گریزازمرکز توصیه میکنند که جهت اطمینان از بروز پدیده کاویتاسیون بهتراست که NPSHA حداقل 0. 5 متراز NPSHR بیشتر باشد در بعضی از مراجع توصیه شدهاست که NPSHA برای آب حدود 20 در صد و برای هیدروکربورها حداقل 10 درصد از NPSHR بیشتر بوده ولی مقدار اختلاف نباید از 0. 5 متر کمتر باشد:بهر حال ممکناست شرایطی در سیستم انتقال مایع بوجود آید که عملاً شرایط فوق برقرار نبوده و پمپ در معرض کاویتاسیون قرار گیرد. همانطوری که قبلاً گفته شد NPSH (مورد نیاز و قابل دسترس) مقادیر ثابتی نبوده و خود تابعی از دبی جریان در سیستم میباشند.
منحنی تغییرات NPSHA و NPSHR بر حسب دبی، شکلی سهمیگونه دارند. NPSHA با افزایش دبی کاهش یافته (بجهت افزایش از دست رفت ناشی از اصطکاک در سیستم)، در عوض NPSHR با افزایش دبی پمپ کاهش مییابد. در شکل 11 تغییرات NPSHA و NPSHR برحسب دبی نشان داده شدهاست.
برای غلبه بر کاویتاسیون میتوان از روشهای زیراستفاده کرد:
افزایش NPSHA
کاهش NPSHR
افزایش مقاومت مکانیکی قطعات پمپ در مقابل کاویتاسیون
روشهای افزایش NPSHA
NPSHA جزء مشخصههای سیستم و مایع مورد پمپاژ میباشد. بنابر این جهت افزایش آن باید در شرایط طراحی و بهره برداری از سیستم و مشخصههای فیزیکی مایع مورد انتقال تجدید نظر بعمل آورد. بنا بر تعریف NPSHA از رابطه زیر و در دهانه مکش پمپ محاسبه میشود:
ارتفاع سرعتی + ارتفاع معادل فشار بخار مایع - ارتفاعاستاتیکی مکش = NPSHA
ارتفاع معادل از دست رفت انرژی در قسمت مکش - اختلاف ارتفاع مایع تا منبع مکش
رابطه فوق را میتوان بصورت زیر خلاصه نمود:
که در آن:
بار فشار مطلق در منبع مکش
بار فشار بخارمایع در دمای پمپاژ
متر بر ثانیه سرعت مایع در دهانه مکش پمپ
=
متر اختلاف ارتفاع سطح مایع تا دهانه مکش پمپ Z=
متر جمع از دست رفت انرژی در لوله مکش
وزن مخصوص مایع SG =
تذکر: اگر سطح مایع از دهانه مکش پمپ بالاتر باشد (Head)، علامت Z مثبت بوده و اگر از دهانه مکش پمپ پائینتر باشد ، علامت Z منفی خواهد بود. در حالتی که مایع و دهانه مکش پمپ در یک سطح قرار دارند Z=0 میباشد. جهت افزایش NPSHA لازماست که در روابط مقادیر مثبت افزایش داده شده و یا مقادیر با علامت منفی کاهش داده شود. افزایش NPSHA موجب افزایش هزینههای ثابت (هزینههای لوله کشی)در سیستم میگردد. .
روشهای غلبه بر کاویتاسیون از طریق افزایش NPSHA
همانطوری که قبلاً اشاره شد، جهت افزایش NPSHA لازماست که در رابطه مقادیر منفی را کاهش و یا مقادیر مثبت را افزایش داد. برای این منظور میتوان از روشهای زیراستفاده کرد:افزایش فشار در منبع مکش
این روش برای مواردی که پمپ مایع مورد انتقال را ازمخزنی بسته دریافت میکند قابل اجراء میباشد. افزایش فشار منبع مکش میتواند با تزریق گاز به بالای سطح مایع و افزایش فشار مایع موجود در منبع بطور مستقیم صورت پذیرد. گاز مورداستفاده باید سازگاری لازم را با مایع مورد انتقال داشته باشد. در شرایط عادی غالباً از هوا و در شرایط خاص (ضرورت خنثی بودن گاز مورداستفاده) عموماً از ازت استفاده میشود.کاهش فشار بخار مایع از طریق سرد کردن آن
همانطوری که دربالا اشاره شد، فشار بخار مایعات تابعی از دمای آن بوده و با افزایش درجه حرارت افزایش مییابد (و بالعکس). در مواقعی که امکان کاهش درجه حرارت مایع موردانتقال مجازباشد، بااستفاده از مبدل حرارتی و یا تزریق مایع سرد به قسمت مکش پمپ میتوان درجه حرارت مایع و در نتیجه فشار بخار آنرا کاهش داد.در صورتاستفاده از مبدل حرارتی از آنجائی که عبور مایع مورد انتقال از درون مبدل حرارتی خود باعث کاهش فشار مایع در قسمت مکش پمپ میشود که چندان مطلوب نمیباشد. بنابراین مبدل حرارتی باید طوری طراحی شود که افت فشار مایع بهنگام عبور از آن حتی الامکان کم بوده و در حدی باشد که نتایج حاصل از کاهش دمای مایع را که منجر به کاهش فشار بخار آن میشود خنثی نسازد.
تزریق مایع سرد به مایع مورد انتقال حتی در مقادیر کم میتواند نتایج بسیار مطلوبی را در پی داشته و به همین خاطر در اکثر موارد برای کاهش فشار بخار مایع از این روشاستفاده میشود. در سیستمیکه برای انتقال آب گرم (با دمای 163? ( طراحی شدهاست، تزریق آب با دمای 79? به میزان 4 درصد باعث افزایش NPSHA به میزان 20 فوت (6. 1 متر) میشود. در شکل 12 نحوه تزریق مایع سرد به قسمت مکش پمپ نشان داده شدهاست.
بالا بردن سطح مایع در منبع مکش
شاید در نظر اول بالا بردن سطح مایع در منبع مکش جهت افزایش NPSHA راه حل ساده ای بنظر برسد ولی در خیلی از موارد این امر تقریباً غیر ممکن میباشد. مثلاً اگر پمپ برای انتقال آب از رودخانه و یا دریاچه بکارگرفته شود و یا هزینه بالا بردن منبع مکش زیاد باشد، امکان اجراء این دستورالعمل تقریباً غیر ممکن خواهد بود. با این وجود در مواردی که این اقدام عملی باشد، افزایش جزئی ارتفاع سطح مایع ضمن حل مشکل کاویتاسیون این امکآنرا مهیا میسازد تا بتوان ازپمپ ارزانتر وباراندمان بیشتراستفاده کرد که در نهایت منجر به کاهش هزینه خرید، هزینههای بهره برداری (مصرف انرژی) و تعمیرات خواهد شد.پائین بردن پمپ
در اکثر موارد پائین بردن پمپ و کاهش میزان مکش و یا افزایش ارتفاع آسانتر از بالابردن سطح مایع میباشد. نتایج حاصل از این اقدام همانند حالت قبل خواهد بود. یک روش جایگزین و مشابه آناستفاده از پمپهای عمودی که پروانه آن در قسمت زیرین پمپ و پائینتر از سطح زمین قرار دارد میباشد. مشکل این روش در روانکاری یاطاقانهای پمپ خواهد بود. باید بررسی شود که آیا مایع مورد انتقال قابلیت روانکاری مطلوب یاطاقانها را دارا میباشد یا خیر؟ امروزه با پیشرفتهائی که در طراحی و انتخاب مواد اولیه یاطاقانها حاصل شدهاست مشکل روانکاری یاطاقانها تقریباً حل شدهاست. با این وجود نباید انتظار داشت که عمر مفید یاطاقانها حتی هنگامیکه باروغن ویا گریس روانکاری میشوند در حد عمر پمپ باشد. در هر حال این روش موجب افزایش میزان تعمیرات مورد نیاز برای پمپ میگردد.کاهش ازدست رفت انرژی در لوله مکش
جریان مایع از منبع مکش تا دهانه چشمه پروانه همواره با از دست رفت انرژی (افت فشار)توام میباشد. بنابراین هر اقدامیدر زمینه کاهش افت فشار ناشی از عبور مایع از درون لوله و اتصالات موجود در مسیر مکش پمپ میتواند در افزایش NPSHA مؤثر واقع گردد که عمدهترین آنها عبارتند از:کاهش دبی پمپ
کاهش طول مسیر مکش
کاهش تعداد اتصالات
افزایش قطر لوله مکش
استفاده از اتصالات با از دست رفت انرژی کمتر
هریک از اقدامات فوق تأثیری جداگانه در کاهش از دست رفت انرژی در لوله مکش(افزایش NPSHA) باقی میگذارد. از دست ارتفاع در سیستمهای لوله کشی با مربع دبی جریان (و یا بعبارت صحیحیتر با Q^1.85) رابطه مستقیم دارد. از سوی دیگر کاهش دبی موجب کاهش NPSHR نیز خواهد شد.
همانطوری که مشاهده میشود، با کاهش دبی، فاصله NPSHA از NPSHR زیادتر شده و عملکرد پمپ در جهت بهره برداری با شرایط امنتر هدایت میشود. برای کاهش دبی پمپ میتوان از روشهای مختلفی نظیر تغییر سرعت دورانی، ایجاد مقاومت در قسمت مکش و یا ایجاد مقاومت در مسیر دهش (استفاده از شیر کنترل دبی) و... استفاده کرد.
ایجاد مقاومت در قسمت مکش هرچند که باعث کاهش دبی جریان در لوله مکش میگردد ولی باتوجه به اینکه خود باعث افزایش افت فشار در لوله مکش میشود روش منطقی نبوده و به هیچ وجه توصیه نمیشود. تغییر سرعت دورانی جهت کاهش دبی پمپ در صورت قابلیت اجراء روش مطمئنی میباشد. ایجاد خفگی در مسیر دهش پمپ جهت کاهش دبی روش ساده ای بوده و لذا جهت حل مقطعی مشکل بروز کاویتاسیون میتوان آنرا بهترین روش دانست.
البته کاهش دبی خود عوارض جدیدی را بدنبال داشته که عمدهترین آن بروز جریان گردشی در قسمت مکش پمپ میباشد، لذا نباید این روش را بعنوان یک راه حل قطعی تلقی نمود.
کاهش طول مسیر مکش از طریق نزدیک کردن پمپ به منبع مکش هرچند که روی ارتفاع کل مورد نیاز در سیستم تأثیری نمیگذارد ولی باعث کاهش ازدست رفت انرژی در لوله مکش و افزایش NPSHA میگردد. به همین خاطر در طراحی سیستم لوله کشی بویژه در مواردی که احتمال بروز کاویتاسیون زیاد میباشد اکیداً توصیه میشود که پمپ در نزدیکترین محل نسبت به منبع مکش نصب گردد. تأثیر طول مسیر برروی افت فشار یک رابطه خطی بوده و لذا میزان ازدست رفت انرژی در لوله مکش با کم کردن طول آن بطور خطی کاهش مییابد.
افزایش قطر لوله و سایر اتصالات موجود در لوله مکش تأثیر زیادی برروی کاهش ازدست رفت انرژی باقی میگذارد. بطوری که مثلاً با 2 برابر کردن قطر لوله مکش، میزان افت انرژی در آن حدود 32 برابرکاهش مییابد.
در اکثر سیستمهای انتقال حتی در مواردی که احتمال بروز کاویتاسیون کم میباشد توصیه میشود که لوله مکش حدود یک تا دو اندازه (Size)، از لوله دهش بزرگتر در نظر گرفته شود. با کاهش تعداد اتصالات وحذف قطعات غیر ضروری در مسیر مکش میتوان NPSHA را افزایش داد. مثلاً باید از پیچ وخم دادن غیر ضروری مسیر مکش خودداری کرد و یا در مواقعی که منبع مکش در پائینتر از دهانه ورودی پمپ قرار دارد نیازی به نصب شیر تعمیراتی در لوله مکش نمیباشد.
اتصالات براساس کیفیت طراحی و ساختمان آنها دارای از دست رفت انرژی مختلفی میباشند، مثلاً از دست رفت انرژی در زانوئی شعاع بلند در مقایسه با زانوئی استاندارد بسیار کمتر بوده، و یا افت فشار در هنگام عبور مایع از درون شیر کشوئی (Gate Valve) چندین برابر کمتر از شیر توپی (Globe Valve) میباشد. به همین خاطر در انتخاب اتصالات برای نصب در قسمت مکش پمپها باید سعی شود از اتصالاتیاستفاده شود که از دست رفت انرژی در آن در حداقل ممکن باشد.
و: استفاده از پمپ تقویتی (Booster Pump) درقسمت مکش
این روش بویژه برای مواردی که پمپ اصلی برای اعمال ارتفاع (فشار) زیاد طراحی شدهاست بسیار مؤثر میباشد، چرا که اجازه میدهد تا پمپ اصلی با سرعت بیشتری کارکرده و همین امر ضمن کاهش قیمت پمپ اصلی، موجب افزایش راندمان، کاهش تعداد مراحل و افزایش قابلیت اعتماد در سیستم میگردد.پمپهای تقویتی عموماً پمپهای با سرعت و ارتفاع کم و از نوع یک مرحله ای با NPSHR کم میباشند که با افزایش جزئی فشار مایع، NPSHA در دهانه مکش پمپ اصلی را افزایش میدهند.
مترجم: حبیب الله علیخانی
پمپ ماشینی است که از آن برای جابجائی سیالات تراکم ناپذیر مانند مایعات استفاده میشود و پمپاژ عبارت است از افزایش انرژی فشار مایعات جهت انتقال آن از نقطه ای به نقطه دیگر. افزایش فشار مایعات در فرآیند پمپاژ، میتواند بدلایل زیر باشد:
غلبه بر اصطکاک موجود در سیستم (شبکههای آب رسانی شهری).
غلبه بر مقاومت (فشار) موجود در مقابل جریان مایع (پمپ تغذیه دیگ بخار).
ذخیره سازی مایعات در سطح انرژی پتانسیل (ارتفاع یا فشار) بالاتر (منابع هوائی آب)
انجام کار مکانیکی (سیستمهای هیدرولیک)
دسته بندی پمپها
پمپها برحسب مکانیسم عملکرد آن به دو دسته تقسیم میشوند:
پمپهای با جابجائی مثبت
در پمپهای جابجائی مثبت، مقدار معینی از مایع در لای دو قطعه گیر انداخته شده و سپس با جابجائی قطعه (یا قطعات) متحرک پمپ، مایع مورد پمپاژ تحت فشار خروجی از پمپ به خارج رانده میشود. در این پمپها، فاصله ی باز بین قطعات متحرک و پوسته بسیار ناچیز بوده و لذا جابجائی مایع در جهت رو به جلو صورت میپذیرد. پمپهای جابجائی مثبت خودبه دودسته تقسم میشوند:
بکارگیری پمپهای جابجائی مثبت جنبه عمومی نداشته و فقط در شرایط ویژه ای مورداستفاده قرار میگیرند. مثلاً وقتی که فشار خروجی بالا مورد نظر بوده ویا اینکه مایع مورد جابجائی دارای ویسکوزیته زیاد باشد، ترجیح داده میشود که ازپمپهای دورانی استفاده شود. ازسوی دیگر بعلت حساسیت شدید دبی جریان در پمپهای گریزازمرکزبه ارتفاع کلی موجوددر سیستم، در مواردی که ثبات نسبی دبی در سیستم مورد نظر باشد، بعلت تغییرات اندک دبی جریان در پمپهای جابجائی مثبت و عدم وابستگی نسبی آن به فشار سیستم ، ترجیحاً باید از پمپهای جابجائی مثبتاستفاده شود.
پمپهای گریز از مرکز
بعلت ویژگیهای مطلوب پمپهای گریزازمرکز، امروزه بیش از60 %پمپهای مورداستفاده در دنیا از نوع گریز از مرکزمیباشند. پمپهای گریز ازمرکز جزء ماشینهای جنبشی بوده، چرا که در اثر حرکت دورانی پروانه، انرژی جنبشی مایع بطورعمده و انرژی پتانسیل (فشار) آن بطور جزئی افزایش یافته، آنگاه بخش اعظمیاز انرژی جنبشی اعمال شده در یک مجرای گشاد شونده بنام حلزونی به انرژی پتانسیل تبدیل میشود. از آنجائی که انرژی داده شده به مایع به سرعت آن بستگی دارد، لذا افزایش انرژی پتانسیل مایع ، با دبی آن تغییر میکند. بر همین اساس، عملکرد پمپها با منحنی مشخصه آن که معرف تغییرات دبی در مقابل مقاومت موجوددر سیستم فشار یا ارتفاع میباشد، نشان داده میشود (شکل 1).
همانطوری که از شکل فوق پیداست، دبی پمپهای گریز ازمرکز در مقابل تغییرات مقاومت موجود در سیستم بشدت تغییر نموده و بر همین اساس میتوان ظرفیت آن را با تغییر مقاومت در سیستم کنترل کرد. حال آنکه دبی (ظرفیت) پمپهای جابجائی مثبت تقریباً ثابت بوده و هر چند که ظرفیت آن را نمیتوان با تغییر مقاومت در سیستم تغییرداد، ولی در عوض ویژگی فوق اجازه میدهد تا در مواردی که لازم باشد، سیستم پمپاژ با ظرفیت تقریباً ثابت کارکرده و با تغییر شرایط موجود در سیستم، دبی پمپ تغییر چندانی نکند، پمپهای جابجائی مثبت (بویژه پمپهای دیافراگمی) انتخاب مناسبی میباشند.
پمپهای گریز از مرکز را میتوان ازنظر مکانیکی ماشینی ساده و ازنظر هیدرولیکی ماشین پیچیده ای دانست که از قسمتهائی نظیر پروانه که در داخل پوسته یا پیچک میچرخد، سیستم آب بندی ، یاطاقانها و شافت تشکیل شده است.
گشتاور داده شده به شافت از طریق تیغههای پروانه به مایع مورد پمپاژمنتقل شده و باعث افزایش سرعت مایع میگردد. ولی از آنجائی که هدف از بکارگیری پمپها، افزایش فشار مایعاتاست ونه سرعت آن، بنابراین لازماست که حتی الامکان، انرژی جنبشی (سرعت) به انرژی پتانسیل (فشار) تبدیل شود. این امر در یک مجرای گشاد شونده بنام حلزونی صورت میپذیرد.در شکل 2 تغییرات سرعت مطلق مایع درمسیرجریان ازدرون پوسته پمپ (از دهانه مکش تا دهانه خروجی) نشان داده شدهاست.
مایع مورد پمپاژ با سرعت کم و تحت تأثیر فشار مکش وارد پروانه شده و با چرخش پروانه، شتاب، سرعت وتا حدودی فشار آن افزایش مییابد، بنحوی که در قسمت لبه تیغهها سرعت آن به حد اکثر خود رسیده و بعد از خروج از پروانه، وارد پوسته شده و بتدریج سرعت آن کاهش و فشار آن افزایش مییابد. هرچند که راندمان پمپهای گریزازمرکز از پمپهای جابجائی مثبت کمترمیباشد ولی پائین بودن قیمت اولیه آن عیب فوق را میپوشاند. در بعضی از پمپهای جابجائی مثبت (بویژه پمپهای تناوبی) مایع خروجی از پمپ دارای ضربان است، ولی مایع خروجی از پمپهای گریز ازمرکز دارای جریان پیوسته و یکنواخت بوده وفاقد ضربان میباشد.
در طی 80 سال گذشته دامنه بهره برداری از پمپهای گریزازمرکز چه از نظر فشار و چه از لحاظ دبی قابل دسترس، گسترش وسیعی پیدا نمودهاست. بزرگترین پمپ گریزازمرکز با دبی 417600 متر مکعب در ساعت با ارتفاع 387 متر و توان مصرفی 410 مگاوات در Bath County آمریکا در حال بهره برداری میباشد. در یک ایستگاه فضایی واقع در سیاتل آمریکا از یک پمپ گریز از مرکز با دبی 3400 مترمکعب در ساعت با ارتفاع 56700 متر جهت تأمین سوخت مورداستفاده قرار میگیرد. این پمپ با سرعت دورانی 37000 دور در دقیقه و توان مصرفی 52 مگاوات در حال بهره برداریاست. هرچند که دامنه بکارگیری از پمپهای گریز از مرکز در زمینه ظرفیت بسیار وسیع میباشد ولی نامحدود نیست.دریک جمع بندی کلی پمپهای گریزازمرکز برای دبی زیاد وارتفاع کم تازیاد وپمپهای جابجائی مثبت برای دبی کم وارتفاع (فشار) زیاد مناسب میباشند .
دبی (ظرفیت)
بنا بر تعریف مقدار حجمیاز مایع که در واحد زمان توسط پمپها جابجا میشود را دبی یا ظرفیت پمپ مینامند. دبی پمپ که عموماً با Q نشان داده میشود، دارای واحدهای مختلفی بوده که عمده ترین آنها عبارتاست از متر مکعب در ساعت، متر مکعب در ثانیه ، لیتر در ثانیه و گالن دردقیقه (GPM). در جدول 1 تبدیل واحدهای ظرفیت به یکدیگر ارائه شدهاست. جدول1 دسته بندی انواع پمپها و در شکل 3 محدوده بکارگیری آنها نشان داده شدهاست.
ارتفاع
سازندگان پمپهای گریز ازمرکز همواره علاقمندند که منحنی مشخصه پمپها را طوری تهیه و در اختیار خریداران قرار دهند که به خواص فیزیکی مایع مورد پمپاژ (بویژه وزن مخصوص) بستگی نداشته باشد. برای این منظور بجای استفاده از فشار، از اصطلاحی به نام ارتفاع استفاده میشود.
در پمپهای گریز ازمرکز، در صورت ثابت بودن قطر و سرعت دورانی پروانه، مقدار انرژی که به واحدوزن مایع داده میشود، مقداری ثابت بوده و مستقل از وزن مخصوص آن میباشد. به همین خاطر، در بیان عملکرد پمپهای گریز ازمرکز، منحنی مشخصه آن بصورت منحنی H-Q (دبی - ارتفاع) ارائه میگردد. فرض میشود که ستونی از آب سرد (با وزن مخصوص واحد) ساخته شود. برای اعمال یک بار فشار، ستون فوق باید حدود 2/10 متر ارتفاع داشته باشد. بدیهیاست که اگر وزن مخصوص مایع از آب بیشتر باشد، ارتفاع فوق کاهش مییابد (و برعکس) برای تبدیل فشاربه ارتفاع برای مایعی باوزن مخصوص SG توان از رابطه زیر استفاده کرد.
لازم به ذکراست که منحنی مشخصه پمپهای گریز از مرکز (منحنی H-Q) عموماً برای آب تهیه میشود. هرچند که منحنی فوق به وزن مخصوص مایع مربوط نمیباشد و لی با توجه به تأثیر ویسکوزیته برروی عملکرد دینامیکی پمپهای گریزازمرکز منحنی مشخصه ارائه شده برا ی مایعاتی با ویسکوزیته بیشتر از ویسکوزیته آب صادق نبوده و فقط در نقطه Q=0 (Shut Off Point)که سیستم حالتاستاتیکی دارد ارتفاع قابل دسترس برای مایعات مختلف یکسان میباشد، ولی در سایر مقادیر دبی، بلحاظ عملکرد دینامیکی پمپ ، منحنی مشخصه آن با منحنی مشخصه پمپ در حالت انتقال آب مغایرت داشته ودر این صورت کارآئی پمپ کاهش یافته که بطور مفصل در بخشهای بعدی مورد اشاره قرار خواهد گرفت.
با توجه به موارد فوق میتوان نتیجه گرفت:
منحنی مشخصه H-Q هر پمپ گریز از مرکز با قطر و سرعت دورانی ثابت، برای تمامیمایعات مستقل از وزن مخصوص آن میباشد.
در صورت مغایرت ویسکوزیته مایع مورد پمپاژ با ویسکوزیته آب، منحنی مشخصه پمپ دارای شکل نزولی خواهد بود (در Q≠0، به ازاء دبی ثابت، پمپ برای مایعات با ویسکوزیته بیشتر، ارتفاع کمتری را اعمال میکند).
فرض میشود که پمپی باید فشاری برابر با 9/6 بار(psi100) را در قسمت دهش اعمال نماید، اگر سیال مورد پمپاژ آب باشد، ارتفاع خروجی پمپ معادل 4/70 متر (261 فوت) بوده، در صورتی که برای ایجاد فشار فوق توسط آب نمک با وزن مخصوص 2/1، ارتفاع ستون به 8/58 متر (193 فوت) کاهش مییابد. در عوض همین فشار با ستونی به ارتفاع 96 متر (308 فوت) توسط نفت سفید (با وزن مخصوص 75/0) ایجاد میشود. در شکل 4 تأثیر وزن مخصوص مایع برروی ارتفاع جهت دست یابی به فشار معین برای آب، آب نمک و نفت سفید نشان داده شدهاست.
ارتفاع سیستم
ارتفاع کلی هر سیستم شامل اجزاء زیر میباشد:
ارتفاعاستاتیکی
ارتفاع ناشی از اختلاف فشار بین منبع مکش و دهش
ارتفاع اصطکاکی
از دست رفت ارتفاع ناشی از ورود و خروج مایع به درون لوله
ارتفاع سرعتی
ارتفاعاستاتیکی
ارتفاعاستاتیکی، همان اختلاف ارتفاع سطح مایع دردومنبع مکش ودهش سیستم پمپاژ میباشد (شکل 5).
ارتفاعاستاتیکی خود از دو بخش تشکیل میگردد، ارتفاعاستاتیکی دهش و ارتفاعاستاتیکی مکش. در چنین حالتی، دهانه مکش پمپ بعنوان خط مرجع در نظر گرفته میشود.
اگرسطح مایع در منبع مکش پائین تر از پمپ قرار داشته باشد، اصطلاحاً Lift نامیده و اگر بالاتر از پمپ قرار گرفته باشد، اصطلاحاً آن را Head مینامند. ارتفاعاستاتیکی برابراست با:
که در آن:
ارتفاعاستاتیکی کل
ارتفاعاستاتیکی دهش
ارتفاعاستاتیکی مکش
در حالت Lift علامت بین دو بخش مثبت و در حالت Head منفی در نظر گرفته میشود.
گاهی اوقات سیستم انتقال مایع بصورت شکل 6 میباشد. در مورد نحوه تأثیر گذاری
برروی ارتفاعاستاتیکی سیستم دو نظریه مختلف وجود دارد. برخی اعتقاد دارند که برای انتقال مایع به منبع، ارتفاع
نیز باید منظور گردد ولی از آنجائی که ارتفاع فوق در اثر پدیده سیفون (Siphon) قابل بازیابی میباشد ارتفاع فوق نباید در برخی بر این با ورند که ارتفاع فوق نباید در محاسبهاستاتیکی کل منظور گردد.
اما به نظر میرسد که تصمیم گیری نهائی در این زمینه به شرایط سیستم انتقال مایع بستگی خواهد داشت. اگر ارتفاعاستاتیکی سیستم و تأثیر آن برروی عملکرد پمپ حالت نعیین کننده ای داشته باشد، با توجه به اینکه به هرحال در زمان راه اندازی، پمپ باید قادر باشد که مایع را به منبع برساند،
باید در محاسبه ارتفاعاستاتیکی منظور شود. هرچند که این امر باعث میشود تا بعد از راه اندازی پمپ، ارتفاعاستاتیکی واقعی سیستم در اثر بازیابی انرژی در اثر پدیده سیفون کاهش یافته و همین امر موجب افزایش دبی در سیستم انتقال مایع میگردد.
در سایر موارد که پمپ قابلیت لازم را در زمان راه اندازی جهت تأمین ارتفاع
دارا میباشد، بهتراست که مقدار آن را در محاسبه ارتفاعاستاتیکی منظور نکرده و بدیهیاست که دبی پمپ در هنگام شروع بهره برداری از پمپ از مقدار مورد انتظار کمتر بوده ولی در مدت کوتاهی بلحاظ بازیابی انرژی داده شده به مایع، به حالت عادی بر میگردد.
ارتفاع ناشی از اختلاف فشار بین منبع مکش و دهش
اگر فشار در منبع مکش پمپ
و در منبع دهش پمپ
باشد، ارتفاع ناشی از اختلاف فشار در دو منبع مکش ودهش (
) بر اساس رابطه زیر برابراست با:
از آنجائی که ارتفاعاستاتیکی و ارتفاع ناشی از اختلاف فشار بین دو منبع مکش و دهش هردو مستقل از دبی جریان میباشند، لذا میتوان جمع آن دو را ارتفاع استاتیکی کل منظور کرد. در این صورت ارتفاع استاتیکی کل برابراست با:
ارتفاع اصطکاکی
ارتفاع اصطکاکی، مقدار انرژی لازم برای غلبه بر اصطکاک موجود در لوله و اتصالات (شیر، زانوئی، سه راهی و...) میباشد که با علامت
نشان داده میشود. مقدار
به عوامل متعددی نظیر دبی، قطر لوله، جنس لوله، طول لوله، تعداد اتصالات، نوع اتصالات،ویسکوزیته مایع، وزن مخصوص مایع و... بستگی دارد. رابطه
با دبی سیستم بصورت زیرمیباشد:
که در آن K مقداری ثابت بوده و به عوامل ذکر شده در بالا (بجزدبی) بستگی دارد. n تابعی ازرژیم جریان مایع در سیستم بوده که بصورت زیر تعریف میشود:
جریان آشفته 2-85/1=n جریان آرام 1=n
از دست رفت ناشی از ورود و خروج مایع
بجز در موارد خاص، اغلب پمپها، مایع مورد پمپاژ را از یک منبع ذخیره دریافت میکنند. در محل ورود مایع بدرون لوله مکش، همواره مقداری از دست رفت انرژی وجود داشته که آن را از دست رفت ناشی از ورود مایع به لوله مینامند و مقدار آن به طراحی دهانه ورود مایع بدرون لوله بستگی داشته و با اصلاح آن (نظیر شکل زنگوله ای) میتوان آن را کاهش داد.
به همین ترتیب در قسمت خروجی مایع از لوله دهش، مقداری از انرژی مایع به هدر رفته که آن را از دست رفت خروجی مینامند. در قسمت خروجی، مایع دارای سرعتی مانندV بوده وارتفاع معادل با آن (
) به هدر خواهد رفت. در بعضی از مراجع ترجیح میدهند که از دست رفتهای ورودی وخروجی را جزء از دست رفت ناشی ازاصطکاک منظورنمایند. البته بهتراست که جهت تعیین نقش آنها در از دست رفت انرژی در سیستم هریک را بطور جداگانه محاسبه و در ارتفاع کل سیستم منظور نمود. در بعضی از طرحها سعی میشود که بااستفاده از تبدیل مخروطی طولانی، سرعت را بمقدار زیادی کاهش داده و از این طریق بخش اعظمیاز انرژی را قبل از به هدر رفتن باز یابی کرد.
ارتفاع سرعتی
ارتفاع سرعتی، بیانگر انرژی جنبشی مایع مورد پمپاژ بوده که برحسب ژول بر کیلوگرم (یا متر) بیان میشود. اگر مایعی با سرعت V به سمت بالا پرتاب شود، تا ارتفاعی مانند
بالا خواهد رفت، رابطه
با V بصورت زیر میباشد:
ارتفاع مایع در هر نقطه از لوله برابراست با ارتفاع سرعتی به علاوه ارتفاع فشاری. لازم به ذکراست که فشارسنجها فقط فشار اضافی مایع را نشان داده، در صورتی که انرژی واقعی مایع جمع انرژیهای پتانسیل (فشار) و جنبشی (سرعت) آن میباشد.در پمپهای با ارتفاع زیاد، ارتفاع سرعتی ناچیز بوده ولی در پمپهای با ارتفاع کم نمیتوان از ارتفاع سرعتی صرف نظر کرد.
منحنی مشخصه سیستم
منحنی مشخصه سیستم، تغییرات ارتفاع کلی سیستم را بر حسب دبی جریان مایع نشان میدهد. ارتفاع کلی در سیستم برابراست با جمع جبری ارتفاعاستاتیکی کل و ارتفاع دینامیکی:
اگر ارتفاعاستاتیکی در طی بهره برداری در اثر تغییرات سطح مایع یا فشار در قسمتهای مکش ودهش پمپ تغییر کند، مقدار H_st را باید در دو دامنه حداقل و حداکثر آن در نظر گرفته و منحنی مشخصه سیستم را برای دو مقدار فوق رسم نمود تا دامنه دبی سیستم در دو حالت فوق مشخص گردد. منحنی مشخصه سیستم بر حسب H_st میتواند به شکلهای زیر باشد (شکل 7).
محل تلاقی منحنی مشخصه سیستم با منحنی مشخصه پمپ را نقطه کار مینامند (شکل 8). اکثر مشکلات سیستمهای پمپاژ به قسمت مکش پمپ مربوط میباشد، به همین خاطر در انتخاب و نصب پمپ باید دقت شود تا شرایط قسمت مکش پمپ بنحوی باشد که هیچگاه فشارمایع در این قسمت از فشار بخار آن در دمای انتقال کمتر نشود، چرا که در غیر این صورت پمپ دچار پدیده کاویتاسیون خواهد شد که بطورکامل دربخش هشتم موردبررسی وتجزیه و تحلیل قرار خواهد گرفت.
منحنی مشخصه پمپهای گریز از مرکز
برخلاف پمپهای جابجائی مثبت، پمپهای گریز از مرکز اگر با سرعت ثابتی کار کنند، نمیتوانند دبی ثابتی را در سیستم بر قرار کنند و مقدار آن میتواند ازصفرتا مقدار معینی که به اندازه، طراحی و شرایط پمپ بستگی دارد تغییر کند.ارتفاع کلی قابل دسترس، توان مصرفی وراندمان نیز بادبی پمپ تغییر میکند. البته غالباً منحنیهای فوق برای پروانههای با قطر مختلف ودر مواردی برای سرعتهای مختلف پمپ از سوی شرکت سازنده پمپ تهیه میشود. در شکل 9 نمونه ای از منحنی مشخصه یک پمپ گریزازمرکز نشان داده شدهاست. بعضی از شرکتها جهت سهولت در انتخاب یک پمپ، منحنی مشخصه دسته ای از پمپهای هم خانواده را در یک مجموعه گردآوری ودراختیار مشتریان قرار میدهند. مجموعه فوق میتواند در انتخاب پمپ مناسب در کمترین مدت ممکن مورداستفاده قرار گیرد. بعداز انتخاب پمپ مورد نظر، اطلاعات تکمیلی را میتوان از منحنی مشخصه پمپاستخراج کرد.
دسته بندی منحنی مشخصه پمپهای گریزازمرکز:
منحنی مشخصه پمپهای گریزازمرکز (منحنی دبی - ارتفاع) را میتوان بصورت زیر دسته بندی کرد:منحنیهای صعودی
درپمپهای بامنحنی صعودی با افزایش ارتفاع سیستم،دبی پمپ بطورپیوسته کاهش مییابد (شکل a12).منحنیهای نزولی
در پمپهای با منحنی مشخصه نزولی، ارتفاع قابل دسترس در نقطه Q=0 حداکثر ارتفاع نبوده و گاهی اوقات آن را منحنی Looping مینامند (شکلb 12).منحنیهای تیز
منحنیهای تیز نوعی منحنی صعودی بوده که تغییرات ارتفاع بین نقطه کار و شرایطی که شیر خروجی کاملاً بسته باشد(Q=0)بسیارزیاداست. البته این امر میتواند فقط در یک دامنه خاصی از منحنی مشخصه پمپ مثلاً بین دبی برابر 100 درصد تا 50 درصد دبی طراحی وجود داشته باشد (شکلc12).منحنیهای تخت
در این پمپها تغییرات ارتفاع در یک دامنه وسیعی از دبی بسیار ناچیز میباشد. این نوع منحنیها میتوانند نزولی و یا صعودی باشند. در تمامیمنحنیهای نزولی همواره در قسمتی از آن، ارتفاع قابل دسترس تقریباً ثابت بوده و به همین خاطر آن را تخت مینامند. (شکلd12)منحنیهای پایدار
در پمپهای با منحنی مشخصه پایدار همواره به ازاء ارتفاع معین، میتوان یک ظرفیت برای پمپ قائل شد.بعبارت دیگر اگر خطی با ارتفاع ثابت (موازی محور طولها) رسم شود، منحنی مشخصه پمپ را فقط در یک نقطه قطع میکند. اساساًاین منحنیها از نوع صعودی میباشند (شکلهای a12وc12).
منحنیهای ناپایدار
در بعضی از پمپها ممکن است به ازاء ارتفاع معین، پمپ در بیش از یک دبی کار کند، یا بعبارت دیگر اگر خطی به موازات محور طولها رسم شود، منحنی مشخصه پمپ رادر بیش از یک نقطه قطع مینماید (شکل های b12 و e12). البته ناپایدار بودن منحنی فقط در یک دامنه معینی از ارتفاع صادق بوده، لذا باید دقت شود که از این پمپها فقط در منطقه پایداراستفاده شود.دسته بندی منحنیهای توان مصرفی
اگر منحنی توان مصرفی بصورتی باشد که در دبیهای کم شکل صعودی داشته و بعد از رسیدن به نقطه با حد اکثر راندمان (BEP) مجدداً شکل نزولی را بخود بگیرد اصطلاحاً آن را غیر بار اضافی مینامند. در حالی که اگر منحنی توان مصرفی با افزایش دبی بطور پیوسته شکل صعودی داشته باشد، منحنی با وضعیت بار اضافی نامیده میشود (شکل 13 و 14).توان مصرفی:
برای محاسبه توان مصرفی در پمپ میتوان جدا از منحنی P-Q ارائه شده از سوی شرکت سازنده پمپ، از رابطه زیر استفاده کرد:که در آن:
توان مصرفی = P
دبی =Q
ارتفاع کل H_t=
راندمان η=
وزن مخصوص SG=
لازم به ذکراست که توان بدست آمده از رابطه فوق، توان ترمزی بوده و برای انتخاب الکتروموتور لازماست که اولاً قدرت الکتروموتور برمبنای حداکثر توان مصرفی در دامنه دبی مجاز تعیین گردیده، ضمناً ضرایب اطمینان زیر برای انتخاب نهائی آن منظور شود.
20% کیلو وات 7.5-0
15% کیلو وات 40-7.5
10% کیلو وات 40 >
منحنی مشخصه پمپهای جابجائی مثبت
به لحاظ ویژگیهای ساختاری،این پمپها آب بند دینامیکی بوده بنحوی که قسمت دهش آن از قسمت مکش تقریباً جدا شدهاست، به همین خاطر از نظر تئوریک دبی آنها با حجم جارو شده قطعات پمپاژ کننده تقریباً یکسان میباشد.دبی این پمپها به سرعت دورانی وحجم هرواحدپمپاژکننده (مثلاً حجم هر سیلندر در هر کورس) بستگی دارد و به همین خاطر آنها را میتوان پمپهای با ظرفیت تقریباً ثابت دانست که دبی آن به ابعاد و سرعت پمپ بستگی داشته و مستقل از فشار دهش میباشد. ولی در عمل بعلت وجود نشتی داخلی، ظرفیت واقعی آن از ظرفیت تئوریک کمتر خواهد بود. در شکل 15، منحنی مشخصه پمپهای جابجائی مثبت از نظر تئوریک و واقعی و نشتی داخلی در آن نشان داده شدهاست.راندمان حجمیاین پمپها (نسبت ظرفیت واقعی به تئوریک) میتواند بین 50 تا 98 درصد باشد. پمپهائی که خوب طراحی شده باشند غالباً با راندمان حجمی85 تا 95 درصد کار میکنند. علاوه بر کیفیت طراحی پمپ (لقی بین قطعات پمپاژ کننده)،
عوامل دیگری نظیر اختلاف فشار قسمتهای دهش و مکش پمپ، ویسکوزیته مایع، سرعت دورانی پمپ نیز میتواند برروی راندمان حجمیآن اثر بگذارد، بنحوی که با افزایش فشار، راندمان حجمی پمپ کاهش یافته، در عوض با افزایش ویسکوزیته مایع و سرعت دورانی پمپ میزان نشتی کاهش (راندمان حجمیافزایش) مییابد.
پمپهای فوق از نظر هیدورولیکی نیز مشکل چندانی در مقابل بالا بردن فشار نداشته و اگر از نظر مقاومت مکانیکی خوب طراحی شده باشند، دارای سقف محدود کننده اعمال فشار نخواهند بود. درصورتی که پمپهای گریزازمرکز اگر با سرعت دورانی و پروانه معینی مورد بهره برداری قرار گیرند،حداکثر فشار (ارتفاع) قابل دسترس آن محدود میباشد. علت این تفاوت اساسی بین پمپهای جابجائی مثبت و گریز ازمرکز را میتوان بصورت زیر بیان کرد. اعمال انرژی جهت افزایش فشار (ارتفاع) در پمپهای گریزازمرکز نخست از طریق افزایش انرژی جنبشی مایع مورد پمپاژ صورت پذیرفته و آنگاه در پوسته پمپ بخش اعظمیاز انرژی جنبشی به انرژی پتانسیل تبدیل میشود. از آنجائی که انرژی جنبشی داده شده به مایع تابعی از سرعت و قطر پروانه پمپ میباشد، لذا در یک پمپ گریزازمرکز بامشخصههای ثابت، حداکثر ارتفاع (فشار) قابل دسترس محدود میباشد. حال آنکه در پمپهای جابجائی مثبت، افزایش فشار از طریق کاهش حجمیاز مایع به تله افتاده در بین فضای تراکم صورت میگیرد و تا زمانی که پمپ بتواند بر مقاومت موجود در مقابل خود غلبه نماید، افزایش فشار ادامه مییابد.
پمپهای جابجائی مثبت خود به دو دسته تقسیم میشوند. پمپهای دورانی و پمپهای تناوبی (رفت و برگشتی). دامنه مجازاستفاده از انواع پمپها بطور کامل در شکل 16 نشان داده شدهاست.
منحنی مشخصه پمپهای دورانی
پمپهای دورانی را میتوان به 5 دسته اصلی تقسیم کرد:پمپ دنده ای
پمپ مارپیچ
پمپ گوشواره ای
پمپ تیغه ای
پمپ روتورهای مارپیچی خروج ازمرکز تقسیم کرد.
در شکل 17 انواع پمپهای فوق نشان داده شده اند.
در شکل 18، منحنی مشخصه یک پمپ دنده ای در سرعتهای مختلف نشان داده شدهاست. همانطوری که قبلاً گفته شد، عملکرد این پمپها به ویسکوزیته مایع مورد پمپاژ نیز وابسته میباشد. با افزایش ویسکوزیته مایع، نشتی داخلی پمپ کاهش یافته و به همین خاطر دبی آن افزایش مییابد، درعوض با وجود افزایش راندمان هیدرولیکی دراثر کاهش نشتی، از لحاظ افزایش اصطکاک داخلی، راندمان کلی و توان مصرفی آن افزایش مییابد (شکل 19).
منحنی مشخصه پمپهای تناوبی
پمپهای تناوبی شامل پمپهای پیستونی، انگشتی و دیا فراگرامیمیباشد. بعلت شرایط خاص طراحی و عملکردآنها، مایع خروجی از این پمپها دارای ضربان (Pulsation) خواهد بود. به همین خاطر منحنی مشخصه آنها دارای شکلی تناوبی (سینوسی) میباشد. اگر از یک سمت قطعه متحرک (مثلاً پیستون) برای جابجائی مایعاستفاده شود پمپ را یک طرفه (Single Acting) مینامند ، در صورتی که اگراز دو طرف قطعه متحرک برای پمپاژ مایعاستفاده شود، پمپ دو طرفه (Double Acting) نامیده میشود.در شکل 20c ، شیب منحنی، همان شتاب جریان مایع از پمپ میباشد. اگر شتاب مایع در پمپ (a) و جرم آن m و سطح مقطع لوله دهش A باشد، در این صورت ضربان فشار(
) برابراست با:
رابطه بالا نشان میدهد که با کاهش شتاب مایع میتوان ضربان فشار را کاهش داد. این امر از طریق کاهش شیب منحنی مشخصه پمپ یا بعبارت ساده تر با افزایش تعداد سیلندرها امکان پذیراست. تأثیر نظریه فوق را میتوان در جدول 2 مشاهده کرد.
روشهای دیگری نظیراستفاده از منبع ذخیره، فیلتر آکوستیک نیز میتواند در کاهش میزان ضربان مؤثر باشند.
مخزن ذخیره حاوی مایع مورد پمپاژ و مقداری گاز (درتماس مستقیم و یا غیر مستقیم با مایع)است. انتخاب ابعاد صحیح و موقعیت نصب مناسب آن بسیار مهم بوده وبی توجهی به آن نه تنها مشکل ضربان را حل نخواهد کرد، بلکه میتواند مشکلات موجود در سیستم را افزایش دهد. در شکل 21 انواع روشهای کاهش ضربان بکمک مخزن ذخیره نشان داده شدهاست.
فیلترآکوستیک ازدومخزن که توسط لولههای کوچکی به یکدیگر متصل شده اندساخته میشود(شکل 22).
عملکردپمپهای گریز ازمرکز
منحنی مشخصه (H-Q) پمپهای گریز ازمرکز در شرایط ایده البررسی تئوری عملکرد پمپهای گریز ازمرکز مبحث پیچیده ای از علم مکانیک سیالات بوده که بطور مفصل در کتابها و مقالات مربوطه بدان اشاره شدهاست. لئونارد اولر(Leonard Euler) دانشمند وریاضیدان نامیسوئیسی (1783-1707) در تحلیلهای خود در این زمینه و با فرض اینکه پروانه قطعه ایاست که از تعداد زیادی تیغه شعاعی با عرض ناچیز و فاصله نزدیک به صفر ساخته شده، ثابت کرد که اگر پروانه ای به شعاع r وعرض b، با سرعت زاویه ایω (رادیان برثانیه)در پوسته پمپی بچرخد، بطوری که زاویه بین لبه تیغه پروانه و خط مماس بر دایره ای که لبه پروانه روی آن دوران میکند β_2 باشد(شکل 23)، در این صورت ارتفاع قابل دسترس توسط پمپ برابراست با:
که درآنg شتاب ثقل زمین، A وB مقادیرثابت میباشند. برای
، پروانه را اصطلاً روبعقبو برای
، پروانه را رو به جلو مینامند. همانطوری که از رابطه بالا پیداست، H وQ با هم رابطه خطی داشته و برحسب مقادیر مختلف β_2 میتواند. نزولی، صعودی ویا موازی محور طولها باشد.
برای پمپهای واقعی میتواند بین 15 تا 35 درجه تغییر کند ولی غالباً آنرا بین 20 تا 25 درجه درنظر میگیرند. در طراحی پروانه، زاویه ورودی مایع بدرون پروانه (
) نیز غالباً بین 15 تا 50 درجه منظور میگردد. انرژی داده شده به مایع با رابطه زیر نمایش داده میشود:
که در آن:
توان داده شده به مایع =
مقادیر ثابت که به طراحی پمپ بستگی دارند =
دبی پمپ = Q
اگر
=0 باشدتغییرات توان داده شده به مایع نسبت به دبی پمپ یک خط مستقیم بوده که ازمرکز مختصات میگذرد. برای
، منحنی توان مصرفی، سهمیشکل و مماس برخط فوق که در قسمت فوقانی آن قرار داشته و برای
منحنی توان مصرفی سهمیشکل و مماس برخط فوق که درقسمت زیرآن قرارمیگیرد (شکل 25).
همانطوری که از رابطه بالا پیداست، ارتفاع ایجاد شده توسط پمپ گریز ازمرکز مستقل از وزن مخصوص مایع مورد پمپاژ بوده، در صورتی که فشار مایع به وزن مخصوص بستگی دارد. به همین دلیل برای راه اندازی پمپ های گریز از مرکز نخست باید آن را هواگیری کرد. اگر در هنگام راه اندازی پمپ، پوسته آن پر از هوا باشد، فشار دهش پمپ به نسبت وزن مخصوص هوا به آب کاهش یافته و به همین خاطر قادر به غلبه بر مقاومت موجود در قسمت دهش پمپ نبوده و پمپ نمیتواند مایعی را جابجا نماید.
درباره کسب و کار چهار شرکت مشهور حوزه فناوری
نویسنده: کسری کریمی طار
بسیاری از شرکتهای بزرگی که امروز در حوزه فناوری مشغول به کارند، کسب و کاری پشت پرده دارند؛ بعضی از آنها کار خود را به عنوان شرکتی متفاوت آغاز کردند و در نهایت به سمت فناوری متمایل شدند. در هر دو صورت بسیاری از مخاطبان از راز پشت پرده این ابر کمپانیها بی خبرند. همین دلیلی شد تا نحوه تاسیس و کسب و کار چهار شرکت بزرگ حوزه فناوری را مورد بررسی قرار دهیم؛ شرکتهایی که قطعا پیش از این نام آنها را شنیده و احتمالا از خود پرسیده اید چه اتفاقی رخ داد که این شرکتها به امپراتوریهای امروزی تبدیل شدند. این همان سوالی است که پاسخ آن را میتوانید با مطالعه این مطلب دریابید.
IBM
سال تاسیس: 1911، ارزش برند: 49/8 میلیارد دلارSAMSUNG
سال تاسیس: 1938، ارزش برند: 37/9 میلیارد دلار
AppIe
سال تاسیس: 1976، ارزش برند: 145/3 میلیارد دلار
نخست اپل1، سپس اپل 2، لیزا و مکینتاش که آخری با وجود مشخصاتش، به علت جلوتر بودن نسبت به زمان، حکم اخراج جابز را امضا کرد. پس از ورود دوباره جابز به شرکت، اکوسیستمی جدید پایه گذاری شد. او میدانست که محصولاتش فقط در صورتی موفق میشوند که چه از منظر سخت افزاری و چه از منظر نرم افزاری قدرتمند و یکپارچه کار کنند. راز موفقیت محصولاتی همچون مک، آی پاد، آی فون، آی پد و حتی اپل واچ نه فقط سخت افزار و ظاهرشان بلکه نرم افزار یا همان سیستم عامل بود که بسیار قانومند و در عین حال ساده طراحی شده بود. اپل با استفاده از قدرت نرم افزاری اش مردم را مجبور به خرید محصولات کرد و سپس کاربران با هجوم به برنامههای اپل، سود سرشاری را روانه جیب سهامداران کردند. با عرضه نسخه ششم آی فون، اپل همچنان جایگاه خود را به عنوان بزرگ ترین شرکت جهان حفظ کرده و حالا آن قدر پول نقد در بانک دارد که میتواند به یک باره دو کشور یونان و آرژانتین را خریدار کند! آنها به تازگی «اپل واچ» را روانه بازار کرده اند، شاید فروش اپل واچ رویایی نباشد، اما زمینه را برای نسلهای بعدی این محصول و عرضه محصول پرفروش دیگری مهیا کرده است. از گوشه و کنار خبر میرسد که مسئولان اپل از حالا به فکر ورود به صنعت خودرو و احتمالا ساخت اتومبیل خود ران هستند. بعضی سیب گاززده را به دلیل جاه طلبی اش شماتت میکنند؛ اما سوال اینجاست با این همه پولی که این شرکت در اختیار دارد، چه باید بکند؟ شاید بهترین جواب این باشد سرمایه گذاری روی آینده.
NOkIA
سال تاسیس: 1871، ارزش برند: 3/2 میلیارد دلار
نوکیا هم مانند بسیاری از شرکتهای حوزه مخابرات کار خود را با ساخت و فروش تجهیزات آغاز کرد، هر چند این شرکت در ابتدای تاسیس خود به فروش کاغذ و سپس لوازم اتومبیل مشغول بود. مسئولان این شرکت اوایل قرن بیستم آن را به چند بخش مختلف تقسیم کردند؛ بخشهایی که از لوازم برقی و دوچرخه تا تایر و کاغذ تولید میکردند. ورود جدی نوکیا به بخش مخابرات باز میگردد به سال 1967/1346 که این قسمت از نوکیا تفکیک شد و به صورت جداگانه شروع به کار کرد. آنها پس از این تفکیک، روی بخشهای مختلفی از جمله ارتباط از راه دور، کابلهای ارتباطی، سیم کشی الکترونیکی و تلفنهای همراه مشغول به کار شدند. مهندسان این شرکت در اوایل دهه 70 میلادی شبکه گوشیهای همراه را در فنلاند توسعه دادند طوری در اواخر این دهه، فلناند تنها کشوری بود که تمامی نقاط آن از این شبکه بهره میبرد و مردم میتوانستند با استفاده از تلفنهای همراه مخصوص خودرو، با یکدیگر مکامله کنند. آنها در سال 1363/1984 اولین تلفن کاملا همراه خود را معرفی کردند، رویدادی که باعث شد نوکیا برای چند دهه به سلطان بلامنازع این صنعت بدل شود شرکت فنلاندی در این مدت همچنان در بخشهای دیگر فعال بود و به همین دلیل است که با وجود افت شدید بخش موبایل و فروش آن در سالهای اخیر، همچنان یکی از شرکتهای مهم فعلی دنیا به شمار میآید. این شرکت اوایل دهه 90 میلادی خود را به عنوان یکی از مهم ترین بازیکنان صنعت نوین موبایل معرفی و تا پیش از ظهور تلفنهای هوشمند و به تبع آن سیستم عاملهای iOSو اندروید، این مقام را حفظ کرد. آنها تا همین چند سال پیش هم به لطف ساخت مدلهای ارزان قیمت، بزرگ ترین تولید کننده تلفنهای همراه شناخته میشدند تا اینکه سامسونگ در این بخش گوی سبقت را هم از آنها ربود. البته نوکیا می توانست در بازار رقابتی باقی بماند اما با حضور استفان الوپ در راس امور، نوکیا به سمت مایکروسافت و سیستم عامل ویندوزفون دست دوستی دراز کرد. الوپ که در آن هنگام رویای ریاست غول ردموند ( لقبی که به مایکروسافت اعطا شده) را در سر میپروراند به عنوان بازوی اصلی استیوبالمرد در نوکیا مشغول به کار شد. ما حصل این اتفاق در نهایت به خریداری بخش موبایل نوکیا در پاییز سال 1392/ 2013 منتهی شد. براساس قرارداد منعقد شده مایکروسافت بیش از 7 میلیارد دلار به نوکیا برای تصاحب بخش موبایل آن و استفاده از نام نوکیا برای 10 سال پرداخت میکرد. البته بخش تلفنهای همراه نوکیا همان زمان که نامش به نام ویندوزفون گره خورد، نابود شد، اما نوکیا به لطف این قرارداد توانست حق استفاده نامش را برای تبلتها نگه دارد و در نتیجه آنها هنوز هم در بازار تبلتها با نام نوکیا فعالیت میکنند. نوکیا همچنان عمده تمرکزش را روی تجهیزات مخابراتی گذاشته و در این بین یکی از بزرگ ترین سرویسهای نقشه به نام Here را در اختیار دارد.
با حضور رئیسجمهور در عسلویه
فازهای 15 و 16 پارس جنوبی با اقتدار افتتاح شد/ پاتک سنگین سپاه به تحریم های آمریکا
در اوج تحریم های آمریکا پالایشگاه فازهای 15 و 16 پارس جنوبی به همت قرارگاه سازندگی خاتمالانبیا(ص) سپاه با حضور رئیسجمهور افتتاح شد.

به گزارش خبرگزاری فارس از عسلویه، در مراسمی که صبح امروز (21 دی ماه) با حضور حجتالاسلام حسن روحانی رئیس جمهور، بیژن نامدار زنگنه، سردار عبادالله عبداللهی فرمانده قرارگاه سازندگی خاتم الانبیاء (ص) سپاه و جمعی از فرماندهان و نیز مسئولین و مدیران حوزه نفت و گاز در عسلویه برگزار شد، پالایشگاه فازهای 15 و 16 پارس جنوبی به طور رسمی افتتاح شد. بنابراین گزارش پالایشگاه فازهای 15 و 16 پارس جنوبی به عنوان ایرانی ترین پالایشگاه، از پیشرفتهترین پالایشگاه های کشور به شمار میرود که تمامی مراحل از مطالعه تا راه اندازی و تولید آن با بهره گیری از توان و ظرفیت داخلی و به دست توانمند متخصصان ایرانی در مجموعه قرارگاه سازندگی خاتم الانبیاء سپاه اجرا شده است. با افتتاح پالایشگاه 15 و 16 پارس جنوبی تولید روزانه بیش از 50 میلیون متر مکعب گاز شیرین، 77 هزار بشکه میعانات گازی، 400 تن گوگرد، 2700 تن اتان، 2900 تن پروپان و بوتان محقق میشود. افتتاح رسمی پالایشگاه فازهای 15 و 16 پارس جنوبی در حالی صورت می گیرد که تمامی واحدهای این پالایشگاه در بهره برداری کامل قرار دارد. گفتنی است قرارگاه سازندگی خاتم الانبیاء (ص) سپاه با استفاده از تجهیزات مدرن و پیشرفته و بهرهمندی از نیروی انسانی متعهد و متخصص توانسته است در شرایط تحریم جایگزین مناسبی برای شرکت های خارجی در عرصه نفت، گاز و پتروشیمی و اجرای موفق فازهای 15 و 16 پارس جنوبی در بستر تحریم ظالمانه غرب علیه ملت ایران آن هم بدون هیچ گونه وابستگی به مهندسان خارجی و با تکیه بر توان داخلی از مصادیق توانمندی و حضور موفق قرارگاه در این عرصه هست. درخواست تزریق 2.2 میلیارد دلار برای تکمیل 9 ابرپروژه/ با افتتاح ستاره خلیج فارس نیازی به بنزین خارجی نداریم سردار عبادالله عبداللهی فرمانده قرارگاه سازندگی خاتمالانبیاء (ص) در مراسم افتتاح فازهای 15 و 16 پارس جنوبی که صبح امروز انجام شد با بیان اینکه ما برای انجام پروژهها نیازی به مهندسین خارجی نداریم، گفت: این پروژه با مهندسی صددرصد ایرانی طراحی، تجهیز، تامین کالا، ساخت و بهرهبرداری شد. وی با بیان اینکه این فازها با بهترین کیفیت آماده شدهاند، گفت: تدبیر خوبی بود که پروژه تکمیل شود بعد افتتاح صورت گیرد و الا اگر میخواستیم 4 ترین را راه بیندازیم قبل از سال 93 کار تمام شده بود. عبداللهی ادامه داد: در زمان بهرهبرداری این فازها 16 میلیارد و 370 میلیون متر مکعب گاز به شبکه سراسری منتقل شده و 15 میلیون بشکه میعانات گازی نیز به دست آمده که اگر ما به مبنای قیمت هزار و 400 تومان حساب کنیم این پروژه دو برابر بیشتر از خودش را مستهلک کرده است. فرمانده قرارگاه سازندگی خاتمالانبیاء (ص) گفت: در جلسهای که با آقای زنگنه داشتیم با توجه به اینکه در مورد گاز با ترکمنستان به مشکل خورده بودیم او ناراحت بود و من عرض کردم تا قبل از سال 92 و در زمانی که تعیین کردهایم میتوانیم کسری گاز را تامین کنیم که این کار نیز عملی شد. وی افزود: توانمندی که امروز در کل کشور وجود دارد میتواند کشور را بسازد که این کار با حمایت مدیران انجام خواهد شد. عبداللهی با اشاره به 9 پروژه بزرگ قرارگاه خاتمالانبیاء گفت: ما به آقای جهانگیری نامه زدیم و راجع به این پروژهها جلسه گذاشتیم. ما در این 9 پروژه 25 میلیارد دلار هزینه کردهایم و 85 درصد پیشرفت فیزیکی داریم و اگر 2.2 میلیارد دلار به آنها تزریق شود سالیانه 35 تا 40 میلیارد دلار عاید کشور میشود. وی با اشاره به دیگر پروژههای قرارگاه اظهار داشت: یکی از این پروژهها ستاره خلیجفارس است که 360 هزار بشکه و 60 میلیون لیتر میعانات گازی دارد. ما کاری نداریم که چرا این پروژه اولویتبندی نشده چون به ضرر کشور است اما الان تمام لولهها و مخازن ما پر است و اگر یک ترین از این پروژه راهاندازی میشد نیازی به بنزین خارج از کشور نداشتیم. عبداللهی با بیان اینکه هر قولی که ما به آقای زنگنه دادهایم انجام شده است، گفت: قرارگاه خاتمالانبیاء با اعتقاد بسیجی و روحیه انقلابی پای کار است. فرمانده قرارگاه سازندگی خاتمالانبیاء (ص) ادامه داد: در پروژه راهآهن قطار سریعالسیر نیز میتوانیم در این دولت بخش اصفهان تا قم که زیرسازی آن تکمیل شده را روسازی و تحویل دهیم. وی افزود: در بحث آبهای مرزی نیز ما بهترین وضعیت را داریم و 5 هزار دستگاه ماشینآلات و 10 هزار نفر در طول خط از ارومیه تا کردستان و ایلام و ... مشغولند و اگر مشکلات سر راه تونل 40 کیلومتری رفع شود میتوانیم آب سیروان را به روی زمین بیاوریم. فرمانده قرارگاه سازندگی خاتمالانبیاء (ص) گفت: وقتی همه فازها راهاندازی شود حدود 200 میلیون مترمکعب گاز آزاد خواهیم داشت و با توجه به خط گازی عسلویه تا ایرانشهر درخواست داریم برای حل مشکل ایران مرکزی که طرح به نام طرح ناب برای آن نوشتهایم مشابه این فازها در آنجا نیز ایجاد شود و با احداث 4-5 نیروگاه هم آب را شیرین کنیم و هم برق را بفروشیم وگرنه هیچ راهی جز آوردن آب از خلیجفارس تا فلات مرکزی نداریم. عبداللهی تاکید کرد: ما از رئیسجمهور، دولت و وزرا درخواست داریم تا ما را در این 9 ابرپروژه همراهی کنند تا کمتر از دو سال به نتیجه برسد و 40 میلیارد دلار عاید کشور شود.
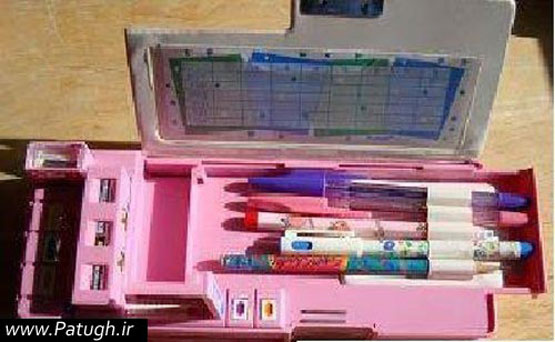
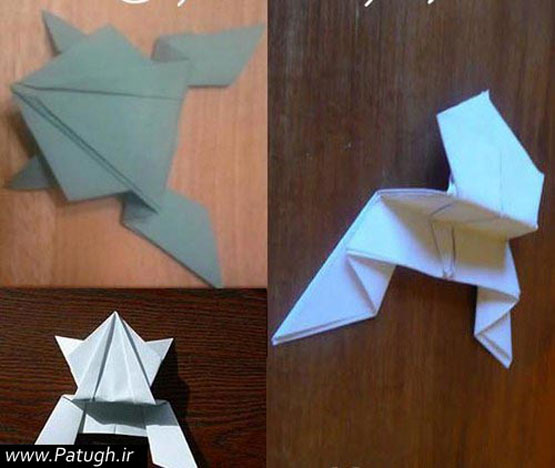
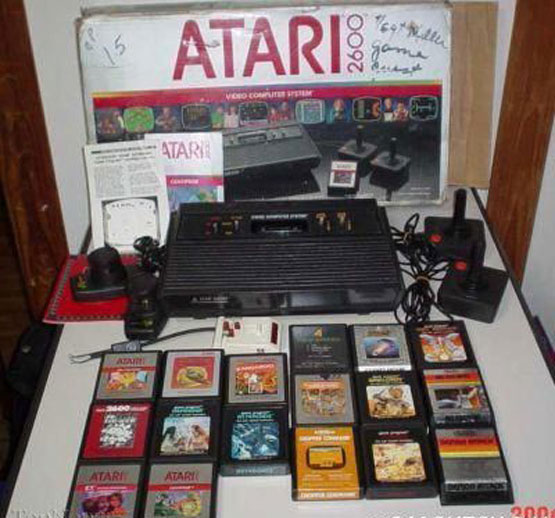
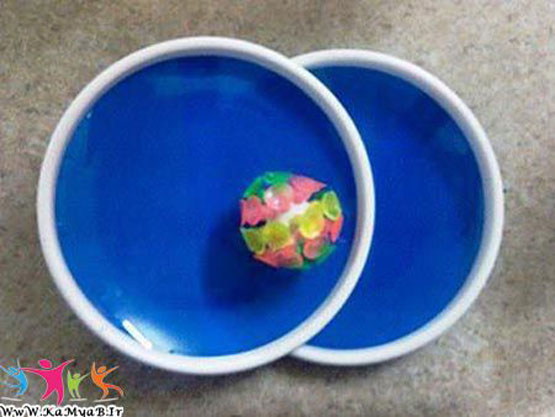
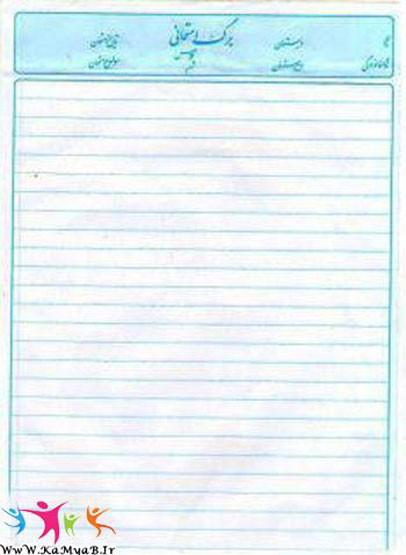
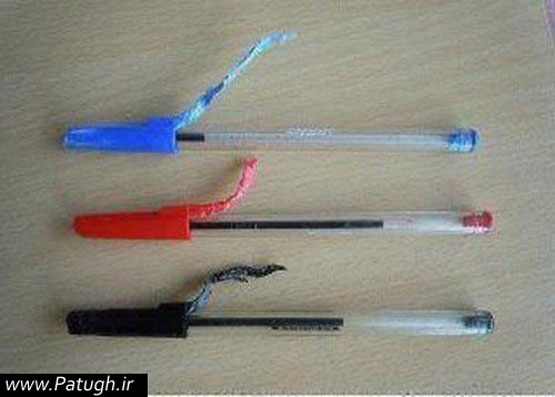
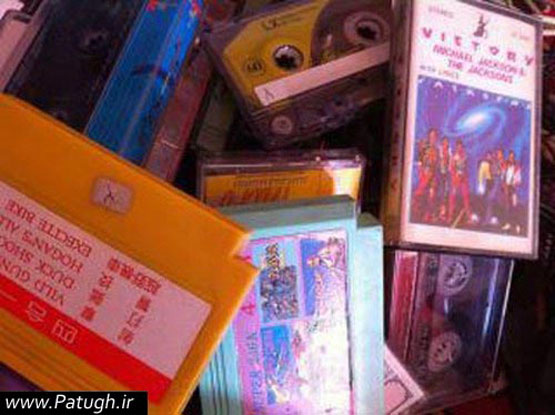
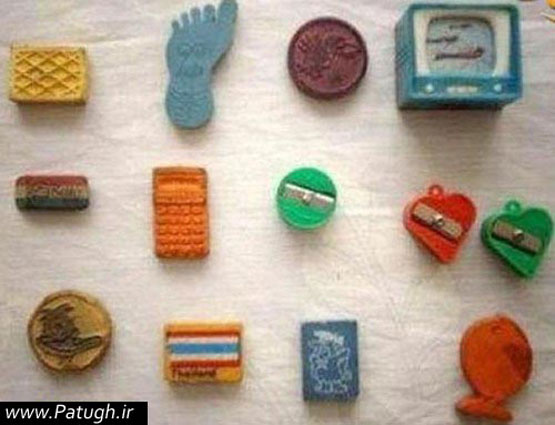
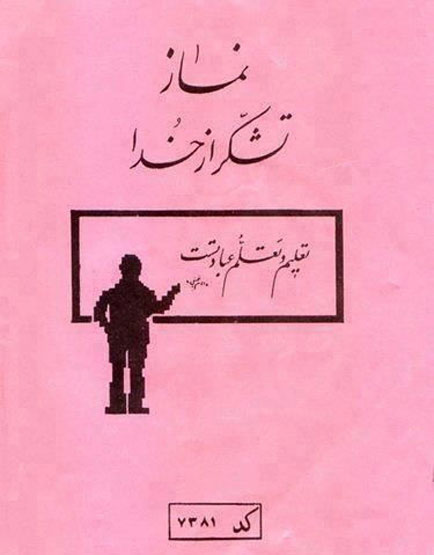
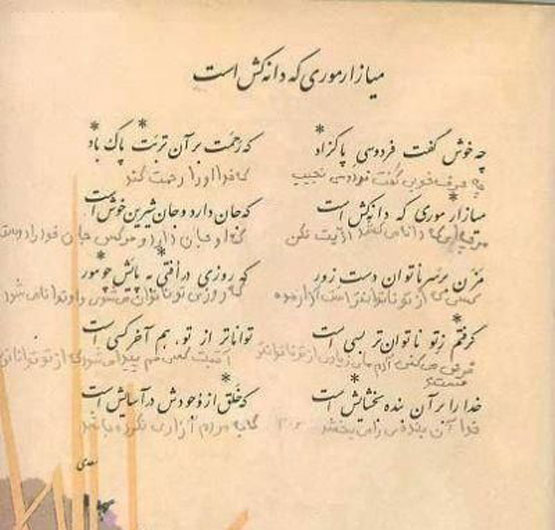
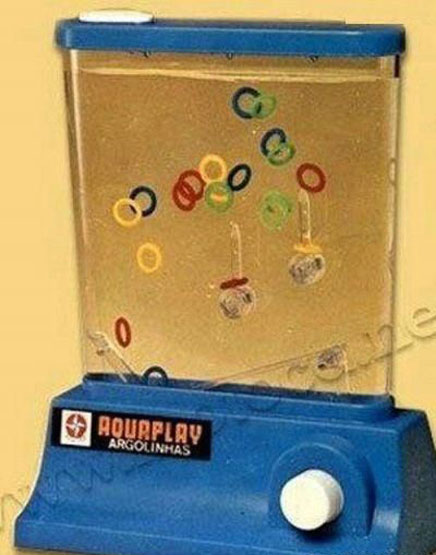
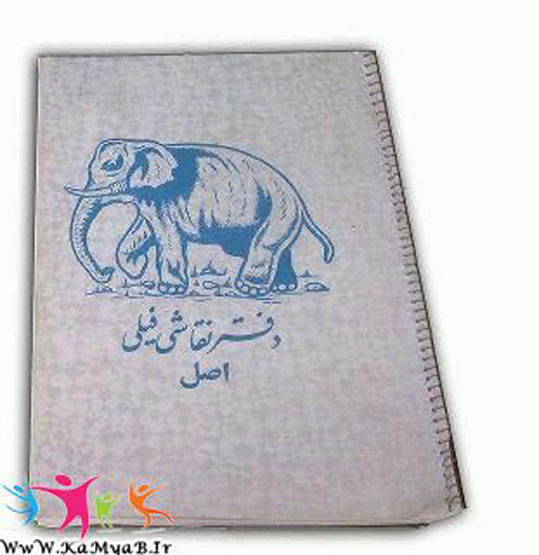
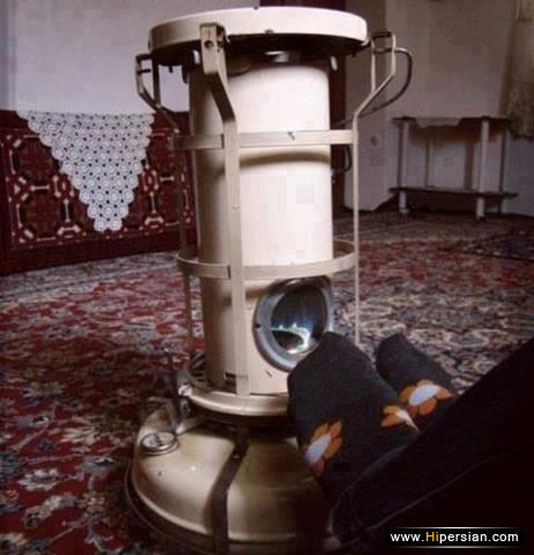
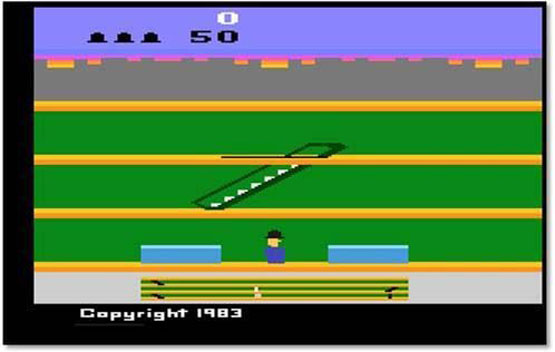
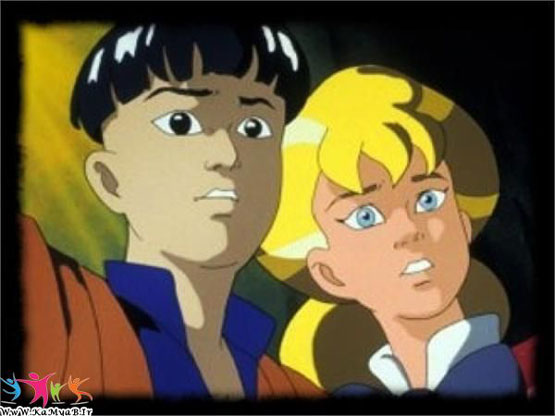