نویسنده : کیوان اسدی | |||||
نگهداری و تعمیر قالبهای تملیکی تولیدکننده که بهصورت امانی در نزد تأمینکنندگان است توسط تأمینکنندگان بهشرح ذیل باید مدیریت شود: - تدوین و آموزش دستورالعمل فرایندهای نگهداری و تعمیر لازم روی قالب در بازه زمانی -مشخص و گزارشدهی از فرایندهای انجام شده روی آن - تدوین دستورالعملهای اپراتوری شامل مونتاژ قالب، تمیزکاری، روغنکاری اجزای آن و آموزشهای لازمه - تصمیمگیری در نحوه انجام فرایندهای موردنیاز اصلاحات و تغییرات - تصمیمگیری در مسئولیت و نحوه پرداخت هزینههای نگهداری و تعمیرات قالبها - نحوه تأیید کیفی قالبها - مسئولیتدهی و قدرتدادن به پرسنل برای انجام وظایف مرتبط با تعمیرها تأیید نهایی تعمیرات قالب و بررسی کیفی آن بهعهده ساپکو است. قالبساز و تأمینکننده، مسئول عیوب ساختی نظیر مونتاژ اشتباه قطعات اینسرتی، مسیرهای خنککاری، انتخاب نامناسب فولاد، ترک روی محفظه و عیوب ناشی از کارهای دستی، هستند. ادامه مطلب... تاریخ : جمعه 89/7/9 | 11:33 عصر | نویسنده : مهندس سجاد شفیعی | نظرات ()
|
درباره وب
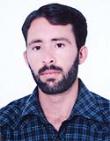
http://www.telegram.me/sajjadshafiee_ir . . . رشته مهندسی پلیمر نسبت به رشتههای مهندسی دیگر تقریبا جوان است و شکوفایی آن از زمان جنگ جهانی دوم آغاز شده است. اما به دلیل کاربرد روزافزون پلیمر در صنایع مختلف، این رشته به سرعت رشد کرده و امروزه جزو یکی از رشتههای مهم کشورهای صنعتی پیشرفته میباشد. هدف رشته مهندسی صنایع پلیمر تولید کلیه محصولات پلیمری از قبیل لاستیک، پلاستیک، الاستومر، چسبها، رزین و سایر مواد مورد نیاز صنعت است. برای مثال طراحی و تولید تایر ماشین در صنایع لاستیک، لولههای پلیاتیلن در صنایع پلاستیک و انواع فایبرگلاسها در کامپوزیت به یاری متخصصان مهندسی صنایع پلیمر انجام میگیرد یا حتی در این رشته شکلدهی رزینها نیز مطرح است که برای مثال میتوان به ساخت ملامین اشاره کرد.حتی کیسههای پلاستیکی و روکش ظروف نچسب ( تفلون ) از مواد پلیمری میباشند. در واقع در رشته مهندسی صنایع پلیمر هر آنچه که به این مواد بر میگردد، مورد مطالعه و بررسی قرار میگیرد. البته پلیمرها فقط کاربرد صنعتی ندارند بلکه کاربرد پزشکی نیز دارند. مثلا اگر کشکک زانوی یک نفر آسیب ببیند و ترمیم آن امکانپذیر نباشد، شبیه به همان کشکک زانو را با مواد پلیمری درست میکنند و بر روی زانو قرار میدهند و یا دندان مصنوعی و لنزهای چشمی همه از مواد پلیمری ساخته میشوند که به این مواد پلیمری «پلیمرهای زیستی» میگویند. فرصتهای شغلی: در صنعت پوشاک پلیمرها در تولید پاپوشها، تنپوشها و کفپوشها بسیار موثر هستند. در صنایع حمل و نقل زمینی (خودروسازی، قطار و ... )، هوایی ( هواپیما و بالگرد) و دریایی (کشتیها و ...) پلیمرها حضوری چشمگیر دارند، و بالاخره در صنایع نظامی، پزشکی، کشاورزی و بستهبندی کاربرد مواد پلیمری بسیار گسترده است.بدر صنعت پوشاک نیز پلیمرها در تولید پاپوشها، تنپوشها و کفپوشها بسیار موثر هستند. در صنایع حمل و نقل زمینی (خودروسازی، قطار و ... )، هوایی ( هواپیما و بالگرد) و دریایی (کشتیها و ...) پلیمرها حضوری چشمگیر دارند، و بالاخره در صنایع نظامی، پزشکی، کشاورزی و بستهبندی کاربرد مواد پلیمری بسیار گسترده است. باتوجه به کاربرد وسیع پلیمرها در صنایع، فارغالتحصیلان این رشته تواناییهای کافی در زمینههای ایجاد و برنامهریزی واحدهای تولیدی تبدیل پلیمر خام به مواد مصرفی و اشتغا
جستوجو
ویژه مدیریت وب
نویسندگان
لینک دوستان
برچسبها وب
مدیریت (23)
عکس (4)
مدیریت در اسلام (4)
اندروید (3)
فناوری نانو (2)
و (2)
یراق کابینت (1)
کائــوچو (1)
کائوچو طبیعی (1)
کاندیدای (1)
کوبه (1)
نوستالژی (1)
قفل حیاطی (1)
قفل لوکس (1)
قفل یونیک (1)
قفل کتابی (1)
قفل کمدی (1)
گالری یراق کوبه (1)
لاهیجان (1)
مجلس (1)
مدیر موفق (1)
مرد و زن (1)
مرودشت (1)
مزایای بیوپلیمر (1)
ملامین چیست (1)
مدیریت دانش (1)
انقلاب صنعتی (1)
ایام (1)
ایران (1)
اکسترودر (1)
پاسارگاد (1)
پلی اتیلن ، (1)
پلی پروپیلن (1)
پلی ونیل کلراید (1)
ارسنجان (1)
اسلامی (1)
اسلحه پلیمری (1)
امیرکبیر (1)
پی وی سی - PVC (1)
تاسوعا (1)
تسلیت (1)
تولدم مبارک (1)
جزوه الاستومر (1)
حسینی (1)
داستان (1)
داستانهای زیبا (1)
در (1)
دستگیره درب (1)
دهمین (1)
دوره (1)
سوپر جاذب (1)
شعر (1)
شهرستان های (1)
شورای (1)
عاشورا (1)
حامیان بلک اسکین
تاریخ : سه شنبه 89/7/13 | 11:53 عصر | نویسنده : مهندس سجاد شفیعی | نظرات ()